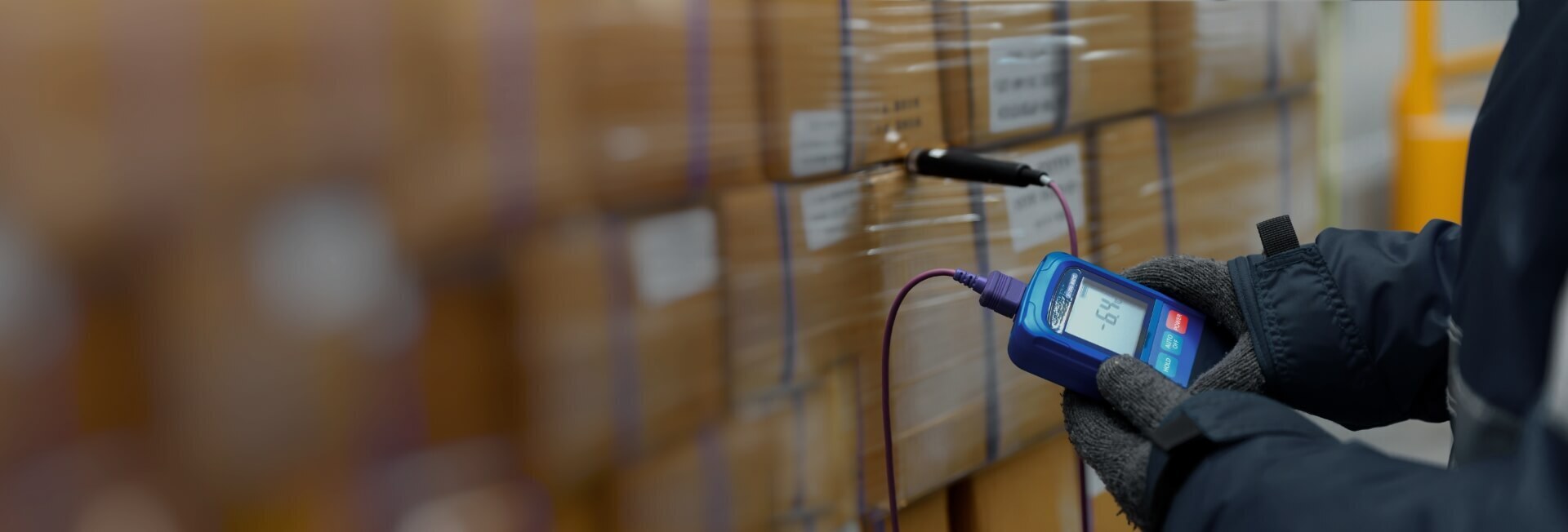
The benefits of implementing kanban systems in manufacturing operations
- Home
- Resources
- Cooling Unit Manufacturing Insights
- The benefits of implementing kanban systems in manufacturing operations
The Benefits of Implementing Kanban Systems in Manufacturing Operations
Kanban, a Japanese word meaning "visual signal" or "card," is a lean manufacturing system that has gained popularity in recent years. Originally developed by Toyota in the 1940s, kanban systems aim to improve efficiency in production and distribution by streamlining the flow of materials and information. By implementing kanban systems, manufacturing operations can optimize their supply chain, reduce waste, and improve overall productivity. In this article, we will explore the benefits of implementing kanban systems in manufacturing operations and how it can lead to manufacturing efficiency.
1. Supply Chain Optimization
One of the main benefits of implementing kanban systems in manufacturing operations is supply chain optimization. Kanban systems help manufacturers identify and address bottlenecks in the supply chain, ensuring that materials and components are available when needed. By using visual signals, such as kanban cards, manufacturers can track inventory levels and trigger replenishment orders in a timely manner. This helps prevent stockouts and reduces the need for excess inventory, ultimately improving the flow of materials and reducing lead times.
Moreover, kanban systems promote collaboration and communication between different departments within a manufacturing organization. By using visual boards and cards, everyone in the organization can easily see the status of ongoing projects and the availability of resources. This transparency allows for better coordination and decision-making, leading to a more efficient supply chain.
2. Waste Reduction
Another significant benefit of implementing kanban systems in manufacturing operations is waste reduction. Kanban systems are designed to minimize waste in all forms, including excess inventory, overproduction, waiting time, defects, and unnecessary transportation. By implementing kanban systems, manufacturers can identify and eliminate these sources of waste, leading to cost savings and improved efficiency.
For example, by using kanban cards to control the flow of materials, manufacturers can avoid overproduction and reduce the risk of excess inventory. This not only saves storage space but also prevents the accumulation of obsolete or perishable goods. By having a clear understanding of customer demand and production capacity, manufacturers can produce only what is needed, reducing waste and improving overall production efficiency.
3. Improved Production Efficiency
Implementing kanban systems can significantly improve production efficiency in manufacturing operations. By using visual signals and limiting work in progress, kanban systems help manufacturers identify and resolve bottlenecks in the production process. This leads to smoother production flows, reduced lead times, and improved on-time delivery.
Moreover, kanban systems promote a culture of continuous improvement by encouraging employees to identify and address inefficiencies in the production process. By visualizing the workflow and making it transparent, kanban systems empower employees to take ownership of their work and contribute to process improvements. This not only boosts morale but also leads to increased productivity and better overall performance.
4. Enhanced Customer Satisfaction
By implementing kanban systems, manufacturers can improve customer satisfaction by ensuring on-time delivery and consistent product quality. Kanban systems help manufacturers gain better visibility into customer demand and production capacity, allowing them to meet customer expectations more effectively.
Additionally, kanban systems enable manufacturers to respond quickly to changes in customer requirements or market conditions. By having a flexible and responsive production system, manufacturers can adapt to fluctuations in demand, reduce lead times, and deliver products faster to customers. This agility in manufacturing operations can give manufacturers a competitive edge and enhance customer satisfaction.
Conclusion
In conclusion, implementing kanban systems in manufacturing operations offers numerous benefits, including supply chain optimization, waste reduction, improved production efficiency, and enhanced customer satisfaction. By using visual signals and promoting transparency, kanban systems help manufacturers streamline their production processes, reduce waste, and improve overall productivity. As manufacturing operations continue to seek ways to improve efficiency and sustainability, kanban systems provide a proven framework for achieving these goals. By implementing kanban systems, manufacturing operations can optimize their supply chain, reduce waste, and enhance their competitiveness in the market.
Related Blogs
The importance of education and awareness in promoting the adoption of green cooling technology
Read More