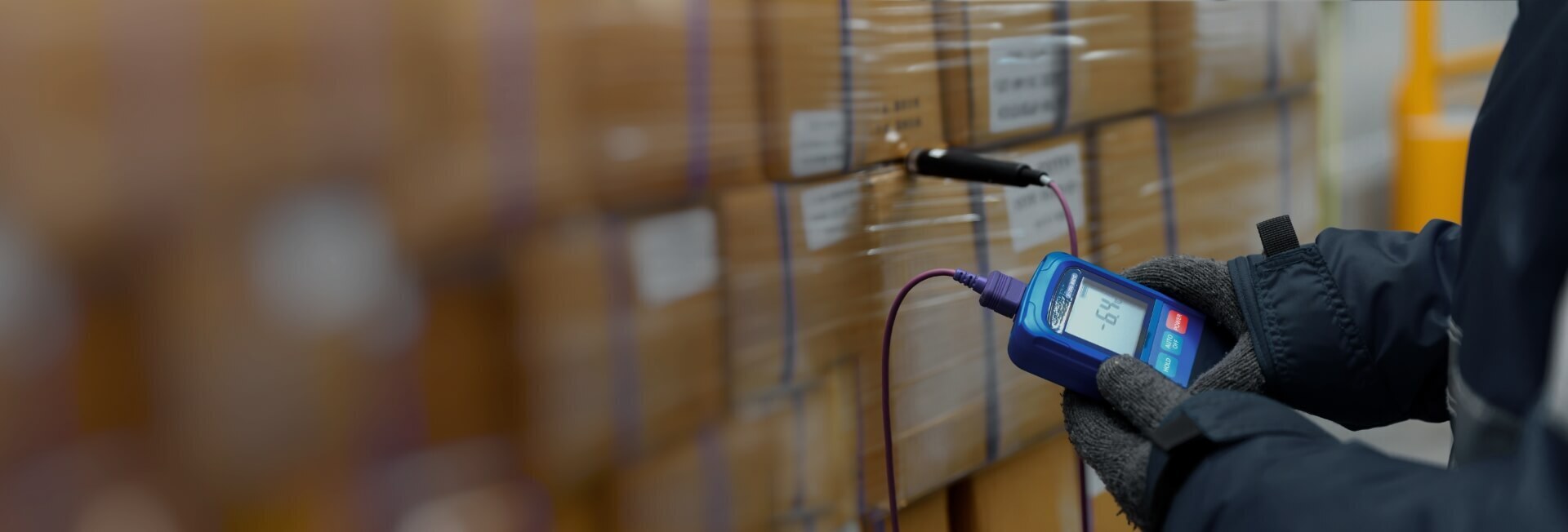
The benefits of implementing error-proofing techniques in manufacturing processes
- Home
- Resources
- Cooling Unit Manufacturing Insights
- The benefits of implementing error-proofing techniques in manufacturing processes
The Power of Error-Proofing Techniques in Manufacturing Processes
In today's highly competitive manufacturing industry, efficiency and quality play a vital role in the success of any business. One way to achieve these goals is by implementing error-proofing techniques in manufacturing processes. Error-proofing, also known as poka-yoke, is a method that focuses on preventing mistakes and defects from occurring rather than relying on detection and correction.
Improving Efficiency and Reducing Waste
One of the key benefits of implementing error-proofing techniques is the improvement in manufacturing efficiency. By eliminating errors and defects at the source, the need for rework and quality control is significantly reduced. This not only saves time but also reduces waste and lowers production costs.
For example, in a production line where components need to be assembled in a specific order, error-proofing can be achieved by incorporating foolproof mechanisms such as color-coding or shape-matching. These visual cues make it easy for operators to identify and place the components correctly, eliminating the need for rework due to incorrect assembly.
Furthermore, error-proofing techniques can also minimize the risk of equipment breakdowns and accidents. By implementing safety measures such as sensors and alarms, potential hazards can be detected and addressed before they cause major disruptions to the manufacturing process.
Enhancing Product Quality
Another significant advantage of error-proofing techniques is the enhancement of product quality. By preventing errors and defects from occurring, the final products are more likely to meet or exceed customer expectations.
For instance, in the automotive industry, error-proofing techniques are commonly used to ensure the correct installation of critical components such as airbags. Sensors and automated checks are employed to verify the proper alignment and connection of these safety devices. This reduces the risk of faulty installations that could compromise the performance and safety of the vehicle.
Moreover, error-proofing can also improve product consistency and uniformity. By standardizing processes and implementing error-proofing mechanisms, variations in product quality due to human error can be minimized. This leads to greater customer satisfaction and loyalty.
Implementing Error-Proofing Techniques
There are several error-proofing techniques that can be implemented in manufacturing processes, depending on the specific requirements of the industry and product. Some common techniques include:
1. Sensory Alert Systems
Sensory alert systems use sensors to detect errors or abnormalities in the manufacturing process. These sensors can be programmed to trigger alarms, stop the production line, or initiate corrective actions when deviations from the standard process are detected.
For example, in a food processing plant, sensory alert systems can be used to detect contaminants in the product. Metal detectors and x-ray machines are commonly employed to identify foreign objects that may have accidentally entered the production line. By promptly identifying and removing these contaminants, product quality and safety are ensured.
2. Foolproof Mechanisms
Foolproof mechanisms are designed to prevent errors and mistakes from occurring in the first place. These mechanisms can take the form of physical or visual cues that guide operators through the correct steps of the manufacturing process.
For instance, in electronics manufacturing, foolproof mechanisms such as polarized connectors and color-coded wires are used to ensure the proper alignment and connection of components. This reduces the risk of incorrect installations and improves product reliability.
3. Error Detection and Feedback Systems
Error detection and feedback systems are used to identify errors and provide immediate feedback to operators. These systems can include automated inspections, quality control checks, and real-time monitoring of key process parameters.
For example, in the pharmaceutical industry, error detection systems can be implemented to verify the correct dosage and composition of medications. Automated checks and barcode scanning can ensure that the right ingredients are used in the manufacturing process, reducing the risk of medication errors.
4. Standardized Work Instructions
Standardized work instructions provide clear and concise guidelines for operators to follow during the manufacturing process. These instructions can include step-by-step procedures, visual aids, and quality checkpoints.
By standardizing the work instructions, variations in product quality due to human error are minimized. This leads to greater consistency and reliability in the final products.
The Future of Error-Proofing Techniques
As manufacturing processes become more complex and automated, the importance of error-proofing techniques continues to grow. In addition to improving efficiency and product quality, error-proofing techniques also contribute to sustainable and environmentally friendly manufacturing practices.
For example, the implementation of precision cooling systems in manufacturing facilities can help optimize energy consumption and reduce greenhouse gas emissions. Cooling system manufacturers are constantly developing custom cooling solutions that are not only energy-efficient but also environmentally friendly.
By using commercial cooling units that are designed with eco-friendly refrigerants and advanced cooling technologies, manufacturers can reduce their carbon footprint and contribute to a more sustainable future. These precision cooling systems ensure that the manufacturing equipment operates at optimal temperatures, minimizing energy waste and extending the lifespan of the machinery.
Furthermore, error-proofing techniques can also reduce material waste and improve the overall sustainability of the manufacturing process. By eliminating errors and defects, the need for rework and scrap material is significantly reduced. This leads to cost savings and a more efficient use of resources.
Conclusion
In conclusion, implementing error-proofing techniques in manufacturing processes offers numerous benefits, including improved efficiency, enhanced product quality, and a more sustainable approach to manufacturing. By preventing errors and defects from occurring at the source, manufacturers can reduce waste, lower production costs, and deliver products that meet or exceed customer expectations.
As the manufacturing industry continues to evolve, error-proofing techniques will play an increasingly important role in ensuring the success and competitiveness of businesses. By embracing these techniques and investing in innovative solutions, manufacturers can streamline their operations, reduce errors, and create a more efficient and sustainable manufacturing environment.
Related Blogs
The importance of education and awareness in promoting the adoption of green cooling technology
Read More