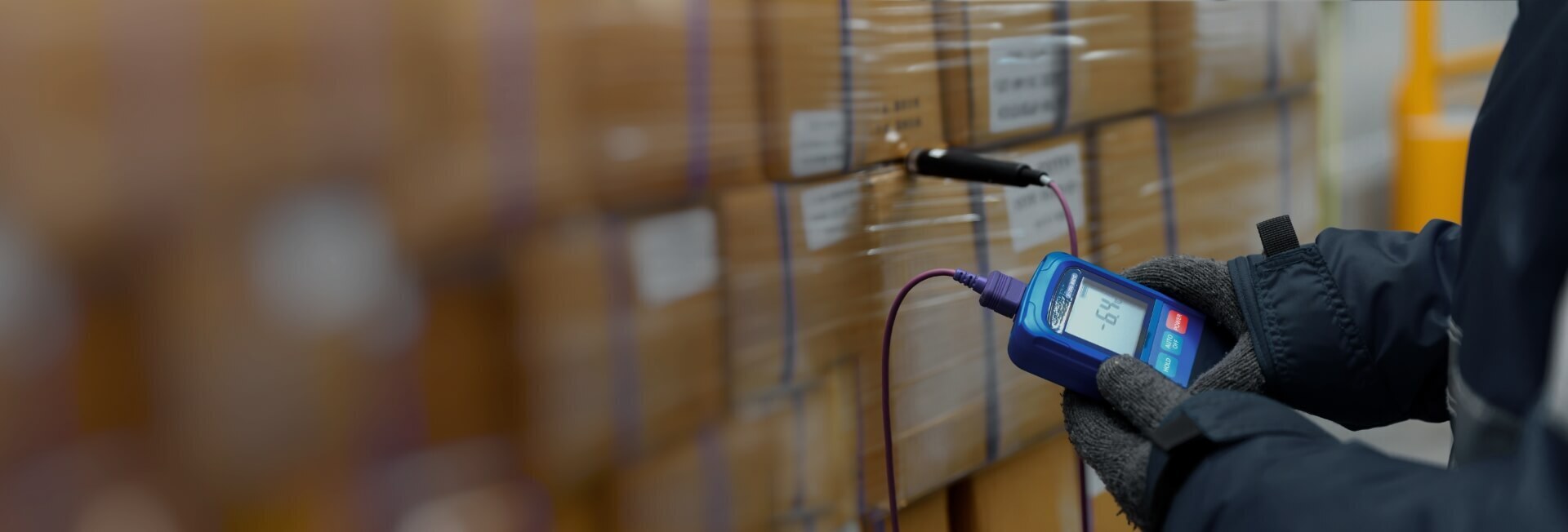
The benefits of implementing energy-efficient welding and soldering techniques in manufacturing
- Home
- Resources
- Cooling Unit Manufacturing Insights
- The benefits of implementing energy-efficient welding and soldering techniques in manufacturing
Introduction
In today's rapidly evolving manufacturing industry, companies are constantly looking for ways to improve efficiency, reduce costs, and minimize their environmental impact. One area that often goes overlooked is the welding and soldering process. By implementing energy-efficient techniques in these processes, manufacturers can not only save money and reduce their carbon footprint, but also improve supply chain optimization and streamline their operations.
The Importance of Energy-Efficiency in Manufacturing
Energy-efficiency is a key factor in modern manufacturing for several reasons. First and foremost, it helps companies reduce their energy consumption and lower their utility bills. By using less energy, manufacturers can save a significant amount of money in the long run. Additionally, energy-efficient practices can help companies comply with environmental regulations and reduce their carbon emissions, improving their overall sustainability and reputation.
Energy-Efficient Welding Techniques
Welding is a crucial process in many manufacturing industries, but it can also be energy-intensive. By implementing energy-efficient welding techniques, manufacturers can significantly reduce their energy consumption and costs. One such technique is pulse welding, which involves using short, high-energy pulses to create a weld. This technique results in less heat generation, reducing the amount of energy required for the process.
Another energy-efficient welding technique is laser welding. Laser welding uses a high-intensity laser beam to create a weld. This process is more precise and controlled compared to traditional welding methods, resulting in less energy waste. Laser welding also eliminates the need for additional materials, such as filler metals, reducing overall production and distribution costs.
Energy-Efficient Soldering Techniques
Soldering is another critical process in manufacturing, particularly in the electronics industry. Energy-efficient soldering techniques can help companies reduce energy consumption and improve overall efficiency. One such technique is selective soldering, which involves using robotic machines to apply solder only to specific areas, minimizing waste and reducing energy usage.
Another energy-efficient soldering technique is wave soldering. This technique involves using a wave of molten solder to join components together. The process is highly efficient, as it only applies solder where it is needed, reducing energy waste. Additionally, wave soldering eliminates the need for manual soldering, improving production speed and reducing labor costs.
The Benefits of Energy-Efficient Welding and Soldering Techniques
Implementing energy-efficient welding and soldering techniques in manufacturing offers several benefits. Firstly, it helps companies improve supply chain optimization. By reducing energy consumption and streamlining processes, manufacturers can operate more efficiently and ensure a smooth flow of materials and products throughout the supply chain.
Secondly, energy-efficient welding and soldering techniques contribute to overall manufacturing efficiency. By reducing energy waste and optimizing processes, companies can increase productivity and reduce production costs. This, in turn, allows manufacturers to offer competitive pricing while maintaining profitability.
Another significant benefit is the positive impact on the environment. Energy-efficient techniques reduce carbon emissions and help companies achieve their sustainability goals. By adopting these techniques, manufacturers can contribute to a greener future and improve their reputation as environmentally conscious businesses.
Furthermore, energy-efficient welding and soldering techniques can lead to improved product quality. By using precise and controlled methods, manufacturers can ensure consistent welds and solder joints, resulting in higher quality products. This can lead to increased customer satisfaction and loyalty, further enhancing a company's reputation and market position.
Conclusion
Energy-efficient welding and soldering techniques offer numerous benefits to the manufacturing industry. By implementing these techniques, companies can improve supply chain optimization, manufacturing efficiency, and overall sustainability. These techniques not only save money and reduce energy consumption but also contribute to a greener future. As the industry continues to evolve, it is essential for manufacturers to prioritize energy-efficiency and embrace sustainable practices.
Related Blogs
The importance of education and awareness in promoting the adoption of green cooling technology
Read More