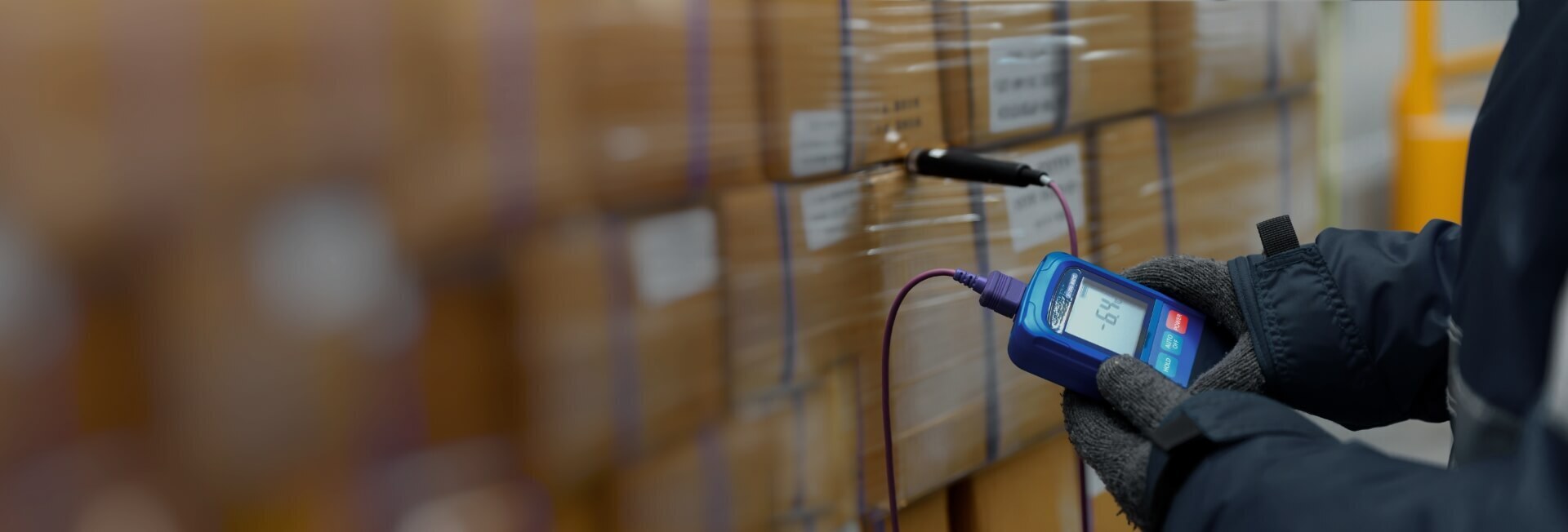
The benefits of implementing 5S methodology in achieving streamlined manufacturing
- Home
- Resources
- Cooling Unit Manufacturing Insights
- The benefits of implementing 5S methodology in achieving streamlined manufacturing
The Benefits of Implementing 5S Methodology in Achieving Streamlined Manufacturing
In today's competitive business landscape, manufacturing companies are constantly seeking ways to optimize their supply chain, improve manufacturing efficiency, and promote sustainable and eco-friendly practices. One approach that has gained significant traction in recent years is the implementation of 5S methodology. This systematic approach to workplace organization and standardization has proven to be highly effective in achieving streamlined manufacturing processes. In this article, we will explore the numerous benefits of implementing the 5S methodology and how it can revolutionize the way manufacturing companies operate.
What is 5S Methodology?
The 5S methodology is a set of principles aimed at improving workplace efficiency, organization, and cleanliness. Originally developed in Japan as part of the Toyota Production System, the 5S methodology has since been adopted by companies worldwide as a best practice in Lean Manufacturing. The five S's stand for Sort, Set in Order, Shine, Standardize, and Sustain, and each step plays a crucial role in achieving a streamlined and efficient manufacturing environment.
Benefits of Implementing 5S Methodology
Implementing the 5S methodology in manufacturing processes can yield a wide range of benefits, including:
1. Improved Productivity and Efficiency
One of the primary benefits of implementing the 5S methodology is improved productivity and efficiency. By organizing the workplace and eliminating unnecessary items, employees can easily locate tools, equipment, and materials, reducing time wasted searching for items. This leads to streamlined processes, increased production output, and ultimately, improved customer satisfaction.
2. Enhanced Safety
Safety is of paramount importance in any manufacturing environment. By implementing the 5S methodology, companies can create a safer workplace for their employees. The Sort step involves removing unnecessary items, reducing clutter, and eliminating potential hazards. The Set in Order step ensures that tools and equipment are properly stored and easily accessible, minimizing the risk of accidents. The Shine step focuses on cleanliness, which not only improves aesthetics but also reduces the risk of slips, trips, and falls. Overall, the 5S methodology promotes a culture of safety and reduces the likelihood of workplace injuries.
3. Optimal Use of Space
Space is often a limited resource in manufacturing facilities. The 5S methodology helps companies optimize the use of available space by eliminating clutter, organizing tools and equipment, and maximizing storage efficiency. By implementing the Set in Order step, companies can ensure that every item has a designated place, reducing the need for excess storage and freeing up valuable floor space. This not only improves workflow but also allows for future expansion or reconfiguration of the manufacturing layout.
4. Improved Quality Control
Quality control is crucial in manufacturing to ensure that products meet the highest standards of quality and reliability. The 5S methodology plays a vital role in improving quality control by standardizing processes and reducing the risk of errors or defects. The Standardize step involves creating clear guidelines and procedures for each task, ensuring consistency and reducing the likelihood of mistakes. By implementing the 5S methodology, companies can achieve higher levels of quality control, resulting in improved customer satisfaction and reduced costs associated with rework or product recalls.
5. Employee Engagement and Empowerment
The 5S methodology fosters a culture of employee engagement and empowerment. By involving employees in the implementation process, they become active participants in improving the workplace. This not only increases employee satisfaction but also promotes a sense of ownership and responsibility. By giving employees the autonomy to organize and maintain their workspaces, companies can tap into the creativity and problem-solving skills of their workforce, leading to continuous process improvement and innovation.
6. Cost Savings
Implementing the 5S methodology can result in significant cost savings for manufacturing companies. By eliminating waste and optimizing processes, companies can reduce material waste, minimize production downtime, and avoid unnecessary expenses associated with inefficiencies. The 5S methodology also helps companies identify and address areas of improvement, leading to long-term cost savings and improved profitability.
Conclusion
The implementation of 5S methodology in manufacturing processes offers numerous benefits, ranging from improved productivity and efficiency to enhanced safety and cost savings. By adopting this systematic approach to workplace organization and standardization, companies can achieve streamlined manufacturing processes, optimize their supply chain, and promote sustainable and eco-friendly practices. The 5S methodology is not a one-time effort but rather a continuous improvement process that requires ongoing commitment and involvement from all levels of the organization. By embracing the principles of Sort, Set in Order, Shine, Standardize, and Sustain, manufacturing companies can revolutionize their operations and stay ahead in today's competitive market.
Related Blogs
The importance of education and awareness in promoting the adoption of green cooling technology
Read More