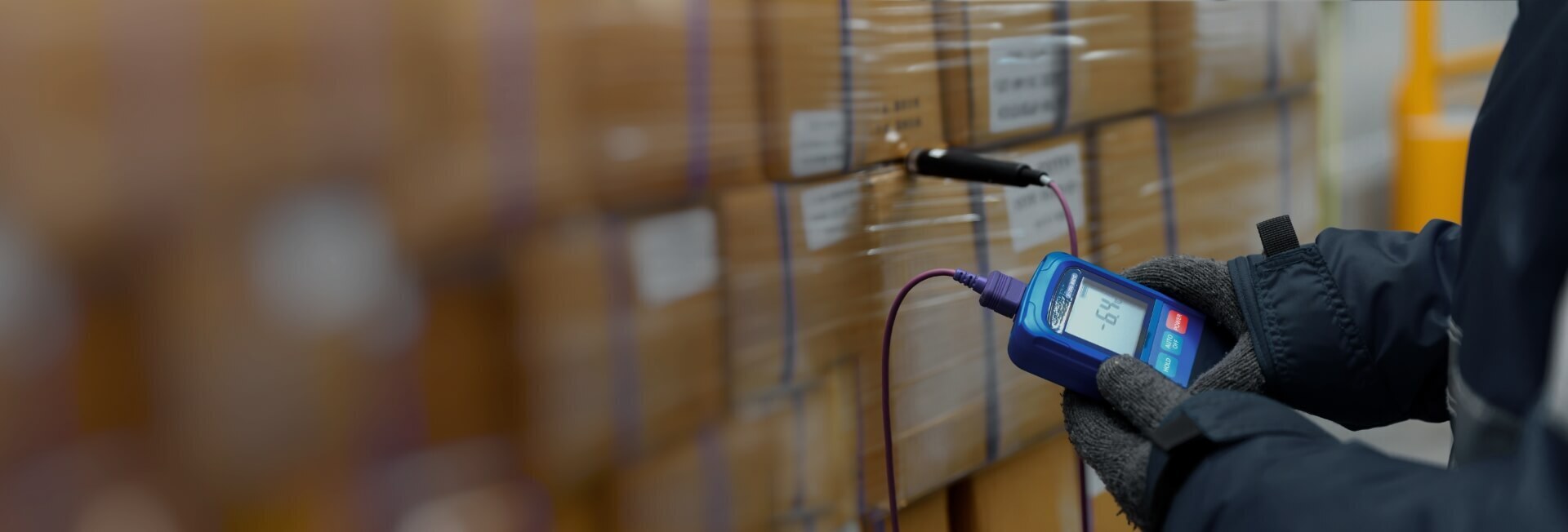
Techniques for optimizing supply chain inventory management
- Home
- Resources
- Cooling Unit Manufacturing Insights
- Techniques for optimizing supply chain inventory management
Techniques for Optimizing Supply Chain Inventory Management
The management of supply chain inventory is a critical aspect of any manufacturing operation. It involves the efficient handling and control of raw materials, work-in-progress items, and finished goods. Proper inventory management is essential to ensure that production and distribution processes run smoothly, costs are minimized, and customer satisfaction is achieved. In this article, we will explore various techniques for optimizing supply chain inventory management, with a focus on improving manufacturing efficiency and streamlining production and distribution.
1. Implementing Lean Manufacturing Principles
One of the most effective techniques for optimizing supply chain inventory management is by implementing lean manufacturing principles. Lean manufacturing aims to eliminate waste and increase efficiency throughout the production process. By reducing excess inventory, companies can lower carrying costs, improve cash flow, and minimize the risk of obsolescence. Lean principles such as just-in-time (JIT) inventory management and continuous improvement can help streamline production and distribution, resulting in shorter lead times and improved customer responsiveness.
2. Utilizing Advanced Forecasting and Demand Planning Tools
Accurate forecasting and demand planning are crucial for efficient supply chain inventory management. By using advanced forecasting tools and demand planning software, companies can better predict demand patterns, optimize inventory levels, and reduce stockouts. These tools leverage historical data, market trends, and demand signals to generate accurate forecasts, enabling companies to make informed decisions regarding production volumes and inventory replenishment.
3. Implementing RFID and Barcode Technology
RFID (Radio Frequency Identification) and barcode technology play a vital role in improving inventory visibility and accuracy. By tagging products and materials with RFID tags or barcodes, companies can track their movement throughout the supply chain in real-time. This enables better inventory control, reduces the risk of theft and loss, and facilitates efficient order fulfillment. RFID and barcode technology also allows for faster and more accurate inventory counting, eliminating the need for time-consuming manual processes.
4. Collaborating with Suppliers and Partners
Collaboration with suppliers and partners is essential for effective supply chain inventory management. By establishing strong relationships and sharing information, companies can gain better visibility into their suppliers' inventory levels, lead times, and production capacities. This enables more accurate demand planning, reduces the risk of stockouts or excess inventory, and improves overall supply chain efficiency. Collaboration can be facilitated through the use of technology platforms and shared data systems, allowing for seamless communication and information exchange.
5. Embracing Green and Sustainable Practices
In recent years, there has been a growing focus on green and sustainable practices in manufacturing. Companies are increasingly adopting eco-friendly and energy-efficient solutions to minimize their environmental impact and reduce costs. When it comes to supply chain inventory management, embracing green and sustainable practices can have several benefits. For example, using energy-efficient cooling technology in warehouses and distribution centers can reduce electricity consumption and lower operating costs. Implementing sustainable packaging solutions can also help minimize waste and improve overall sustainability.
6. Implementing Automated Inventory Management Systems
Automated inventory management systems can greatly improve supply chain efficiency and accuracy. These systems utilize advanced software and hardware solutions to automate various inventory-related tasks, such as order processing, stock replenishment, and inventory tracking. By reducing manual intervention and human error, companies can streamline their inventory management processes, improve data accuracy, and achieve higher levels of customer satisfaction. Additionally, automated systems provide real-time visibility into inventory levels, enabling better decision-making and reducing the risk of stockouts or excess inventory.
7. Continuous Monitoring and Performance Measurement
Continuous monitoring and performance measurement are essential for effective supply chain inventory management. By regularly tracking key performance indicators (KPIs) such as inventory turnover, stock accuracy, and order fulfillment rates, companies can identify areas for improvement and take corrective actions. Implementing regular audits and cycle counting can help maintain inventory accuracy and identify discrepancies or issues. By continuously monitoring and measuring performance, companies can ensure that their inventory management processes are optimized and aligned with business objectives.
Conclusion
Optimizing supply chain inventory management is crucial for improving manufacturing efficiency and streamlining production and distribution processes. By implementing lean manufacturing principles, utilizing advanced forecasting tools, leveraging RFID and barcode technology, collaborating with suppliers and partners, embracing green and sustainable practices, implementing automated inventory management systems, and continuously monitoring performance, companies can achieve significant improvements in inventory control, cost reduction, and customer satisfaction. By adopting these techniques, companies can stay competitive in today's dynamic business environment and achieve sustainable success.
Related Blogs
The importance of education and awareness in promoting the adoption of green cooling technology
Read More