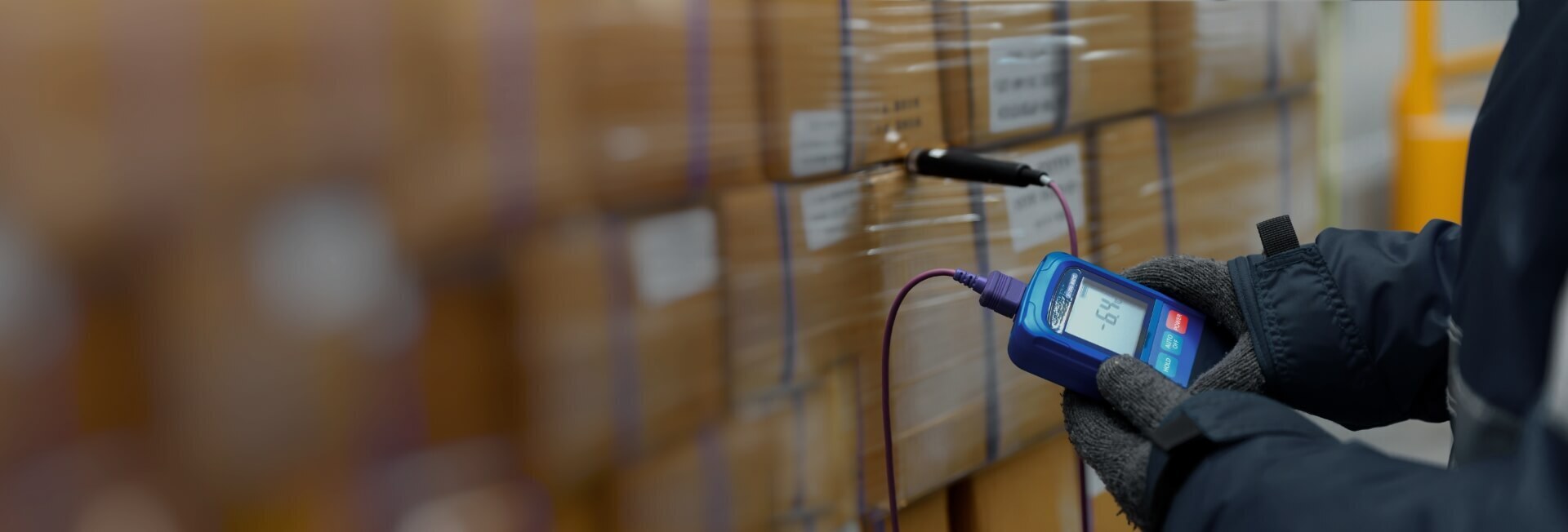
Strategies for reducing energy consumption in textile and apparel manufacturing
- Home
- Resources
- Cooling Unit Manufacturing Insights
- Strategies for reducing energy consumption in textile and apparel manufacturing
Introduction
The textile and apparel industry is one of the largest contributors to global energy consumption and greenhouse gas emissions. The production and distribution processes involved in textile manufacturing require significant amounts of energy, resulting in a negative impact on the environment. In recent years, there has been a growing focus on sustainability and energy efficiency in manufacturing industries, including textiles. Implementing strategies to reduce energy consumption not only helps in minimizing the environmental impact but also improves overall manufacturing efficiency and cost-effectiveness. This article explores some effective strategies for reducing energy consumption in textile and apparel manufacturing, from supply chain optimization to the use of sustainable cooling solutions.
Supply Chain Optimization
One of the key strategies for reducing energy consumption in textile and apparel manufacturing is supply chain optimization. By streamlining the supply chain processes, manufacturers can minimize energy waste and improve overall efficiency. Here are some key steps involved in supply chain optimization:
- Consolidate suppliers and choose those with a commitment to sustainability and energy efficiency.
- Implement just-in-time manufacturing to avoid excess inventory and reduce energy required for storage and transportation.
- Optimize transportation routes to minimize fuel consumption and greenhouse gas emissions.
- Invest in advanced tracking and monitoring systems to identify areas of energy waste and implement corrective measures.
Cooling Technology and Energy Efficiency
The textile and apparel manufacturing process often involves the use of cooling systems to regulate temperature and humidity. However, traditional cooling systems can be energy-intensive and contribute to environmental degradation. By adopting energy-efficient cooling technology, manufacturers can significantly reduce their energy consumption and carbon footprint. Here are some key considerations for implementing energy-efficient cooling technology in textile manufacturing:
- Invest in commercial cooling units that are specifically designed for industrial applications. These units are generally more energy-efficient compared to conventional cooling systems.
- Choose cooling system manufacturers that offer custom cooling solutions tailored to the specific needs of the textile industry. Customized systems can optimize energy consumption by providing precise cooling where it is needed the most.
- Consider the use of sustainable cooling solutions, such as evaporative cooling or solar-powered cooling systems. These solutions utilize renewable energy sources and minimize the environmental impact.
- Implement precision cooling systems that allow for localized temperature control. This helps in avoiding overcooling and reduces energy waste.
- Regularly maintain and optimize cooling systems to ensure their optimal performance. This includes cleaning filters, checking insulation, and repairing any leaks or malfunctions.
Energy-Efficient Production and Distribution
In addition to optimizing the cooling systems, manufacturers can also focus on improving energy efficiency in other aspects of production and distribution. Here are some strategies to consider:
- Upgrade to energy-efficient machinery and equipment. Newer models often come with advanced features that help in reducing energy consumption.
- Implement energy management systems that monitor and control energy usage throughout the manufacturing facility.
- Invest in energy-efficient lighting solutions, such as LED bulbs, which consume significantly less energy compared to traditional lighting systems.
- Optimize production processes to minimize energy waste. This can include optimizing machine settings, reducing idle time, and implementing lean manufacturing principles.
- Explore alternative energy sources, such as solar or wind power, to generate electricity for the manufacturing facility.
Sustainable Practices and Environmental Impact
In addition to implementing energy-efficient strategies, textile and apparel manufacturers can also adopt sustainable practices to minimize their environmental impact. Here are some sustainable practices to consider:
- Implement recycling and waste management programs to reduce the amount of waste generated during the manufacturing process.
- Use eco-friendly materials and dyes that are less harmful to the environment.
- Collaborate with suppliers and partners who share the same commitment to sustainability and environmental responsibility.
- Encourage employees to adopt environmentally friendly practices, such as carpooling or using public transportation.
- Regularly monitor and report on environmental performance to ensure continuous improvement and accountability.
Conclusion
Reducing energy consumption in textile and apparel manufacturing is not only essential for minimizing the environmental impact but also for improving overall efficiency and cost-effectiveness. By implementing strategies such as supply chain optimization, adopting energy-efficient cooling technology, optimizing production and distribution processes, and adopting sustainable practices, manufacturers can significantly reduce their energy consumption and contribute to a greener future. It is important for the textile industry to prioritize sustainability and energy efficiency to ensure a more sustainable and environmentally friendly future.
Related Blogs
The importance of education and awareness in promoting the adoption of green cooling technology
Read More