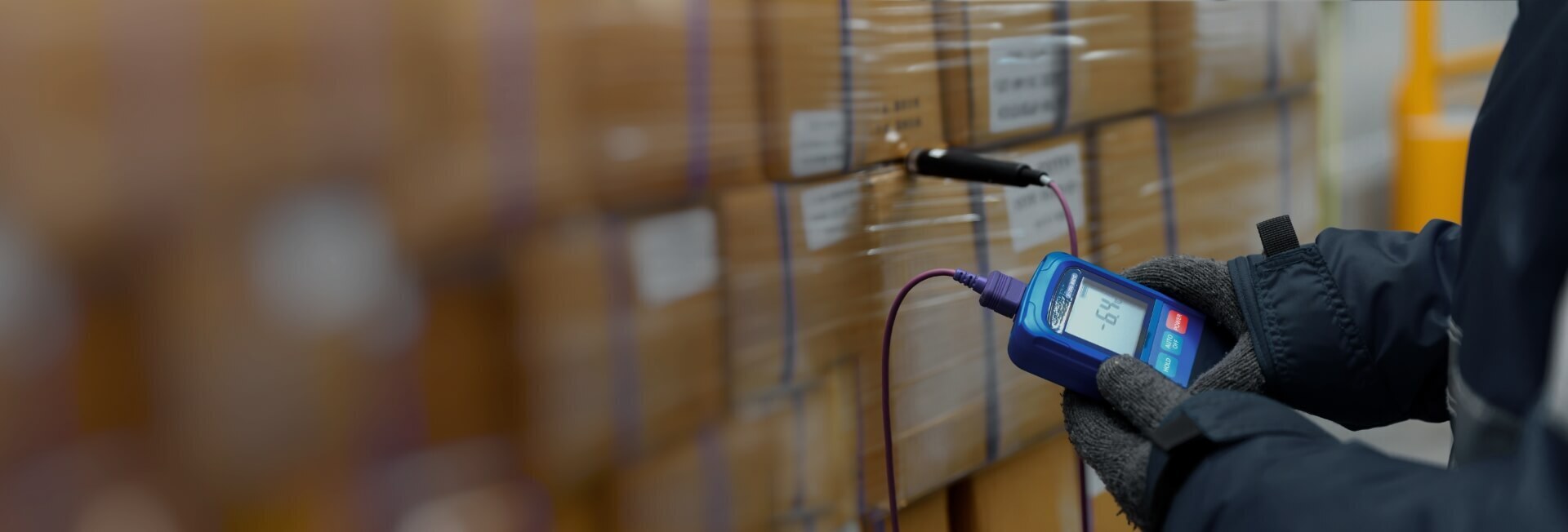
Strategies for reducing energy consumption in industrial cooling and heating systems
- Home
- Resources
- Cooling Unit Manufacturing Insights
- Strategies for reducing energy consumption in industrial cooling and heating systems
Introduction
Industrial cooling and heating systems play a crucial role in various manufacturing processes. These systems are responsible for maintaining optimal temperatures in factories, warehouses, and other industrial facilities. However, they also consume a significant amount of energy, contributing to high operational costs and environmental impact.
In recent years, there has been a growing emphasis on energy efficiency and sustainability in manufacturing. Many companies are actively seeking ways to reduce energy consumption in their cooling and heating systems, not only to lower costs but also to minimize their carbon footprint and promote environmentally friendly practices.
In this article, we will explore strategies for reducing energy consumption in industrial cooling and heating systems. By implementing these strategies, manufacturing facilities can improve their overall efficiency, reduce operational costs, and contribute to a greener and more sustainable future.
1. Upgrade to Energy-Efficient Cooling Technology
One of the most effective ways to reduce energy consumption in industrial cooling systems is by upgrading to energy-efficient cooling technology. Traditional cooling units often consume a significant amount of energy, especially when operating at full capacity for extended periods. By replacing outdated units with newer, more energy-efficient models, companies can significantly reduce their energy consumption and improve overall cooling system performance.
There are many energy-efficient cooling system manufacturers that offer custom cooling solutions tailored to specific industrial needs. These manufacturers utilize advanced technologies such as variable speed drives, high-efficiency compressors, and intelligent control systems to optimize cooling performance while minimizing energy consumption.
When considering an upgrade, it is essential to evaluate the cooling requirements of your facility and choose a system that meets those needs while providing energy savings. Working with an experienced cooling system manufacturer can help streamline the selection process and ensure that you invest in the most energy-efficient solution for your facility.
2. Implement Supply Chain Optimization
Supply chain optimization is another strategy that can help reduce energy consumption in industrial cooling and heating systems. By optimizing the supply chain, manufacturing facilities can streamline production and distribution processes, thereby minimizing energy waste and improving overall efficiency.
One aspect of supply chain optimization is inventory management. By implementing just-in-time inventory practices, companies can avoid excess inventory and reduce the need for excessive cooling and heating. This approach ensures that cooling and heating systems are only used when necessary, minimizing energy consumption.
Another aspect of supply chain optimization is transportation. By optimizing transportation routes and utilizing more fuel-efficient vehicles, companies can reduce energy consumption in the distribution process. This, in turn, reduces the need for cooling and heating during transportation, further contributing to energy savings.
3. Optimize Cooling System Settings
Optimizing cooling system settings can have a significant impact on energy consumption. Many cooling systems operate on default settings, which may not be the most energy-efficient for a specific facility. By adjusting settings such as temperature, fan speed, and ventilation, companies can optimize cooling system performance and reduce energy waste.
To determine the optimal settings for your cooling system, it is recommended to conduct an energy audit or work with a professional HVAC technician. These assessments can identify areas for improvement and provide recommendations for optimizing cooling system settings.
Additionally, implementing temperature and humidity sensors can help monitor and control the cooling system more effectively. These sensors can detect fluctuations in temperature and humidity levels, allowing the system to adjust accordingly and avoid unnecessary energy consumption.
4. Incorporate Renewable Energy Sources
Another effective strategy for reducing energy consumption in industrial cooling and heating systems is incorporating renewable energy sources. Renewable energy, such as solar power or geothermal energy, can be used to supplement or replace traditional energy sources, reducing reliance on fossil fuels and lowering carbon emissions.
Installing solar panels on the roof of a manufacturing facility can generate clean energy to power cooling and heating systems. The excess energy can be stored in batteries or fed back into the grid, further promoting sustainability. Geothermal heat pumps can also be utilized to harness the natural heat from the earth to provide heating and cooling for industrial facilities.
While the initial investment for incorporating renewable energy sources may be higher, the long-term benefits in terms of energy savings and environmental impact make it a worthwhile endeavor. Additionally, government incentives and tax credits for renewable energy installations can help offset the costs.
Conclusion
Reducing energy consumption in industrial cooling and heating systems is not only beneficial for the environment but also for manufacturing efficiency and cost savings. By upgrading to energy-efficient cooling technology, implementing supply chain optimization, optimizing cooling system settings, and incorporating renewable energy sources, companies can achieve significant reductions in energy consumption and contribute to a more sustainable future.
It is essential for manufacturing facilities to prioritize energy efficiency and explore innovative solutions for reducing energy consumption in their cooling and heating systems. By doing so, they can improve their overall operational efficiency, lower costs, and play an active role in promoting environmentally friendly practices.
Related Blogs
The importance of education and awareness in promoting the adoption of green cooling technology
Read More