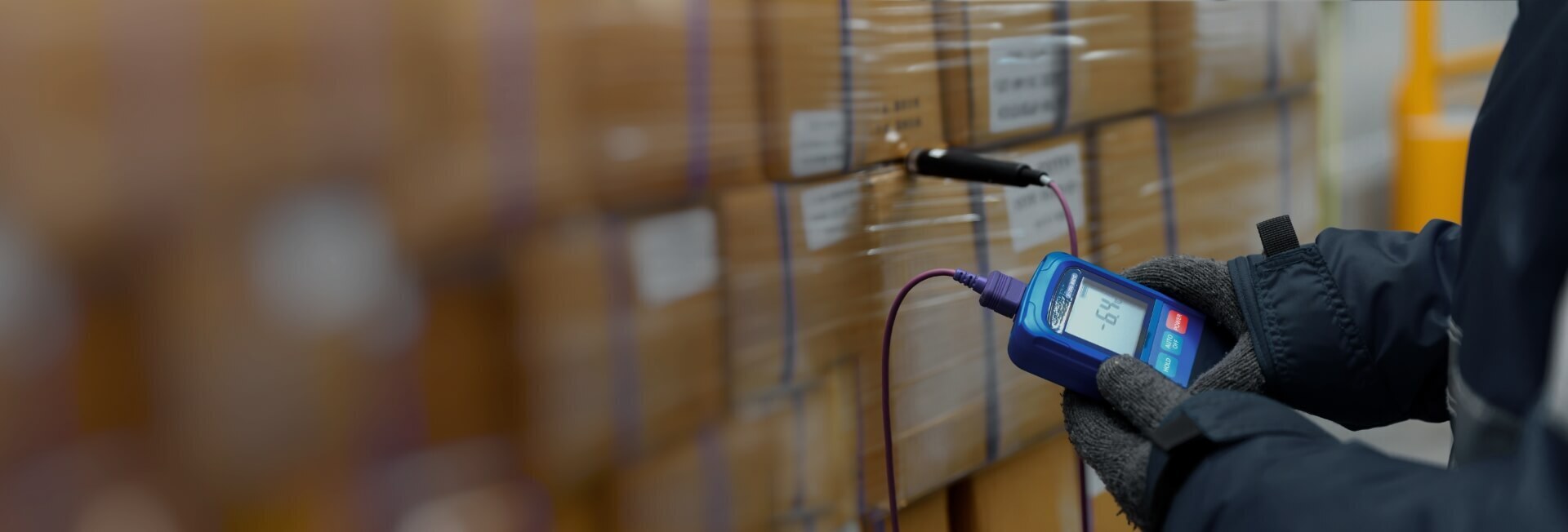
Strategies for reducing energy consumption in chemical and pharmaceutical manufacturing
- Home
- Resources
- Cooling Unit Manufacturing Insights
- Strategies for reducing energy consumption in chemical and pharmaceutical manufacturing
Introduction
In today's world, where sustainability and environmental consciousness are becoming increasingly important, industries are constantly seeking ways to reduce their carbon footprint and energy consumption. The chemical and pharmaceutical manufacturing sectors are no exception. These industries rely heavily on energy-intensive processes and equipment, making energy efficiency a top priority. By implementing strategies to reduce energy consumption, chemical and pharmaceutical manufacturers can not only decrease their environmental impact but also improve their bottom line by reducing operational costs. This article explores some key strategies for reducing energy consumption in chemical and pharmaceutical manufacturing.
1. Supply Chain Optimization
One of the first steps in reducing energy consumption in chemical and pharmaceutical manufacturing is optimizing the supply chain. Supply chain optimization involves streamlining the process of sourcing raw materials, managing inventory, and delivering finished products to customers. By implementing efficient supply chain management practices, manufacturers can reduce the energy required for transportation, warehousing, and distribution.
Supply chain optimization can be achieved through various strategies, such as:
- Consolidating suppliers to reduce transportation distances and costs
- Implementing Just-in-Time (JIT) inventory management to minimize inventory storage and transportation
- Using advanced analytics and forecasting tools to improve demand planning and reduce waste
- Collaborating with suppliers and customers to optimize delivery schedules and routes
By optimizing the supply chain, chemical and pharmaceutical manufacturers can minimize energy consumption associated with the production and distribution of their products.
2. Cooling Technology
Cooling plays a vital role in chemical and pharmaceutical manufacturing processes. Many of these processes require precise temperature control to ensure product quality and integrity. However, traditional cooling systems can be energy-intensive and inefficient. By adopting advanced cooling technologies, manufacturers can significantly reduce energy consumption while maintaining optimal process conditions.
One such technology is the use of precision cooling systems. These systems employ advanced controls and sensors to maintain precise temperature levels, minimizing energy waste. Additionally, custom cooling solutions tailored to specific process requirements can further enhance energy efficiency by eliminating unnecessary cooling capacity.
Another energy-efficient cooling technology is the use of environmentally friendly refrigerants. Traditional refrigerants, such as hydrofluorocarbons (HFCs), have a high global warming potential (GWP) and contribute to climate change. By replacing these refrigerants with low-GWP alternatives, chemical and pharmaceutical manufacturers can reduce their environmental impact and energy consumption.
3. Process Optimization
Process optimization is another effective strategy for reducing energy consumption in chemical and pharmaceutical manufacturing. By analyzing and optimizing each step of the production process, manufacturers can identify energy-intensive operations and implement measures to improve efficiency.
Process optimization can involve:
- Identifying and eliminating process bottlenecks
- Optimizing equipment utilization and sequencing
- Implementing advanced process control systems to optimize energy-intensive operations
- Using real-time monitoring and data analytics to identify energy-saving opportunities
By continuously monitoring and optimizing processes, manufacturers can identify areas for improvement and implement energy-saving measures, leading to significant reductions in energy consumption.
4. Energy-Efficient Equipment
The choice of equipment used in chemical and pharmaceutical manufacturing has a significant impact on energy consumption. By investing in energy-efficient equipment, manufacturers can achieve substantial energy savings without compromising productivity or product quality.
Some examples of energy-efficient equipment in chemical and pharmaceutical manufacturing include:
- High-efficiency motors and pumps
- Energy-efficient lighting systems
- Variable frequency drives (VFDs) for precise control of motor speed and energy consumption
- Heat recovery systems to capture and reuse waste heat
- Efficient boilers and furnaces
By replacing outdated and inefficient equipment with energy-efficient alternatives, manufacturers can significantly reduce their energy consumption and operational costs.
Conclusion
Reducing energy consumption in chemical and pharmaceutical manufacturing is not only essential for environmental sustainability but also for improving operational efficiency and reducing costs. By optimizing the supply chain, adopting energy-efficient cooling technologies, optimizing processes, and investing in energy-efficient equipment, manufacturers can achieve significant energy savings while maintaining product quality and integrity. Implementing these strategies may require upfront investment, but the long-term benefits in terms of energy savings and sustainability make it a worthwhile endeavor for chemical and pharmaceutical manufacturers.
Related Blogs
The importance of education and awareness in promoting the adoption of green cooling technology
Read More