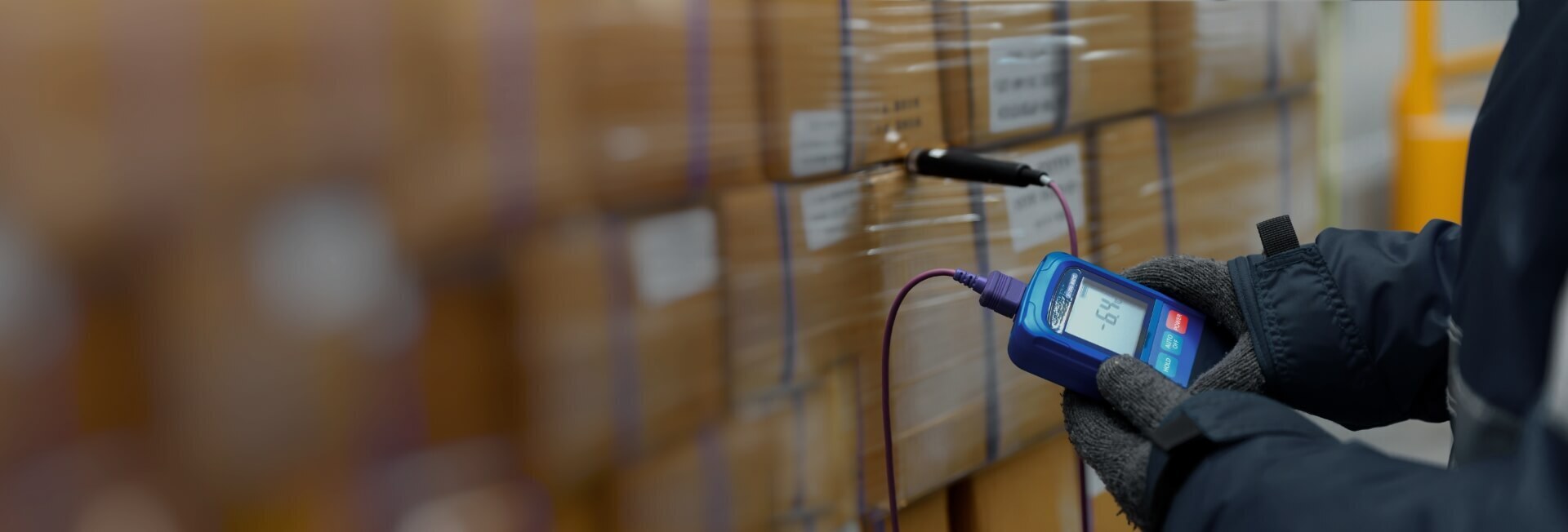
How lean manufacturing principles contribute to streamlined operations
- Home
- Resources
- Cooling Unit Manufacturing Insights
- How lean manufacturing principles contribute to streamlined operations
The Importance of Lean Manufacturing Principles in Streamlining Operations
In today's highly competitive manufacturing industry, companies are constantly seeking ways to optimize their operations, reduce costs, and improve overall efficiency. One approach that has gained significant traction in recent years is lean manufacturing. Lean manufacturing is a philosophy and set of principles that aim to eliminate waste and maximize value for the customer. By implementing lean manufacturing principles, companies can streamline their operations and achieve sustainable growth. In this article, we will explore the importance of lean manufacturing principles in streamlining operations and the benefits they bring to the table.
What is Lean Manufacturing?
Lean manufacturing, also known as lean production, is a systematic approach to eliminating waste and maximizing value in manufacturing processes. It originated in the automotive industry in Japan and was popularized by Toyota. The core idea behind lean manufacturing is to create more value for customers with fewer resources. It achieves this by identifying and eliminating activities that do not add value to the final product or service.
Lean manufacturing principles are based on the following key concepts:
- Value: Define value from the customer's perspective. Anything that does not add value is considered waste.
- Flow: Create a smooth flow of products and information through the manufacturing process.
- Pull: Produce only what is needed, when it is needed, in the quantity needed.
- Perfection: Continuously strive for perfection by relentlessly eliminating waste.
The Benefits of Lean Manufacturing Principles
Implementing lean manufacturing principles can yield numerous benefits for companies, including:
1. Increased Efficiency
Lean manufacturing principles focus on eliminating waste and optimizing processes. By streamlining operations, companies can significantly improve efficiency and reduce costs. This allows them to produce more with fewer resources, leading to increased profitability.
2. Improved Quality
Lean manufacturing principles place a strong emphasis on quality. By eliminating waste and standardizing processes, companies can identify and address quality issues early on. This leads to improved product quality and customer satisfaction.
3. Reduced Lead Times
Lean manufacturing principles help companies reduce lead times by eliminating non-value-added activities and optimizing workflows. This allows them to respond quickly to customer demands and increase their competitive advantage.
4. Enhanced Flexibility
Lean manufacturing principles enable companies to be more flexible and responsive to changing market conditions. By eliminating waste and improving processes, companies can adapt quickly to new customer demands and market trends.
Implementing Lean Manufacturing Principles
Implementing lean manufacturing principles requires a systematic approach and commitment from all levels of the organization. Here are some key steps to consider:
1. Identify Value
The first step in implementing lean manufacturing principles is to identify the value from the customer's perspective. This involves understanding the customer's needs and expectations and aligning the manufacturing processes to deliver that value.
2. Map the Value Stream
Once the value is identified, the next step is to map the value stream. This involves identifying all the steps and processes involved in delivering the final product or service. By mapping the value stream, companies can identify areas of waste and opportunities for improvement.
3. Eliminate Waste
Eliminating waste is a fundamental principle of lean manufacturing. There are seven types of waste in lean manufacturing:
- Transportation waste
- Inventory waste
- Motion waste
- Waiting waste
- Overproduction waste
- Overprocessing waste
- Defect waste
By identifying and eliminating these types of waste, companies can streamline their operations and improve overall efficiency.
4. Implement Continuous Improvement
Continuous improvement is a key principle of lean manufacturing. It involves constantly seeking ways to improve processes, reduce waste, and enhance efficiency. This can be achieved through the use of tools and techniques such as Kaizen events, 5S, and Six Sigma.
Case Study: Lean Manufacturing in Action
One company that successfully implemented lean manufacturing principles is XYZ Manufacturing. XYZ Manufacturing is a leading manufacturer of cooling systems for commercial and industrial applications. They specialize in custom cooling solutions that are energy-efficient and environmentally friendly.
XYZ Manufacturing recognized the need to streamline their operations to meet growing customer demands and stay ahead of the competition. They decided to implement lean manufacturing principles to achieve this goal.
The first step XYZ Manufacturing took was to identify the value from the customer's perspective. They conducted market research and customer surveys to gain insights into their customers' needs and expectations. Based on this information, they defined value as providing cooling solutions that are energy-efficient, reliable, and cost-effective.
Next, XYZ Manufacturing mapped their value stream to identify areas of waste and opportunities for improvement. They found that their manufacturing processes had significant transportation waste and waiting waste. Components were often transported back and forth between different workstations, leading to delays and inefficiencies.
To eliminate waste and optimize their workflows, XYZ Manufacturing implemented a pull-based production system. They established clear communication channels between different departments and suppliers to ensure that production only happened when there was a demand for their products.
Furthermore, XYZ Manufacturing implemented a continuous improvement culture within their organization. They encouraged employees to identify and address areas of waste and inefficiency on an ongoing basis. They also provided training and resources to support employees in their continuous improvement efforts.
As a result of implementing lean manufacturing principles, XYZ Manufacturing experienced significant improvements in their operations. They were able to reduce lead times by 50% and increase production capacity by 30%. Their customers also noticed the difference, as the quality of their cooling systems improved, and the delivery times became more reliable.
Conclusion
Lean manufacturing principles play a crucial role in streamlining operations and improving overall efficiency in the manufacturing industry. By eliminating waste, optimizing processes, and fostering a culture of continuous improvement, companies can achieve sustainable growth and stay ahead of the competition.
Implementing lean manufacturing principles requires a systematic approach and commitment from all levels of the organization. However, the benefits are well worth the effort. Companies that embrace lean manufacturing principles can expect increased efficiency, improved quality, reduced lead times, and enhanced flexibility.
As demonstrated by the case study of XYZ Manufacturing, lean manufacturing principles can deliver tangible results and drive business success. By focusing on value, eliminating waste, and continuously improving processes, companies can create a competitive advantage and meet the ever-changing needs of their customers.