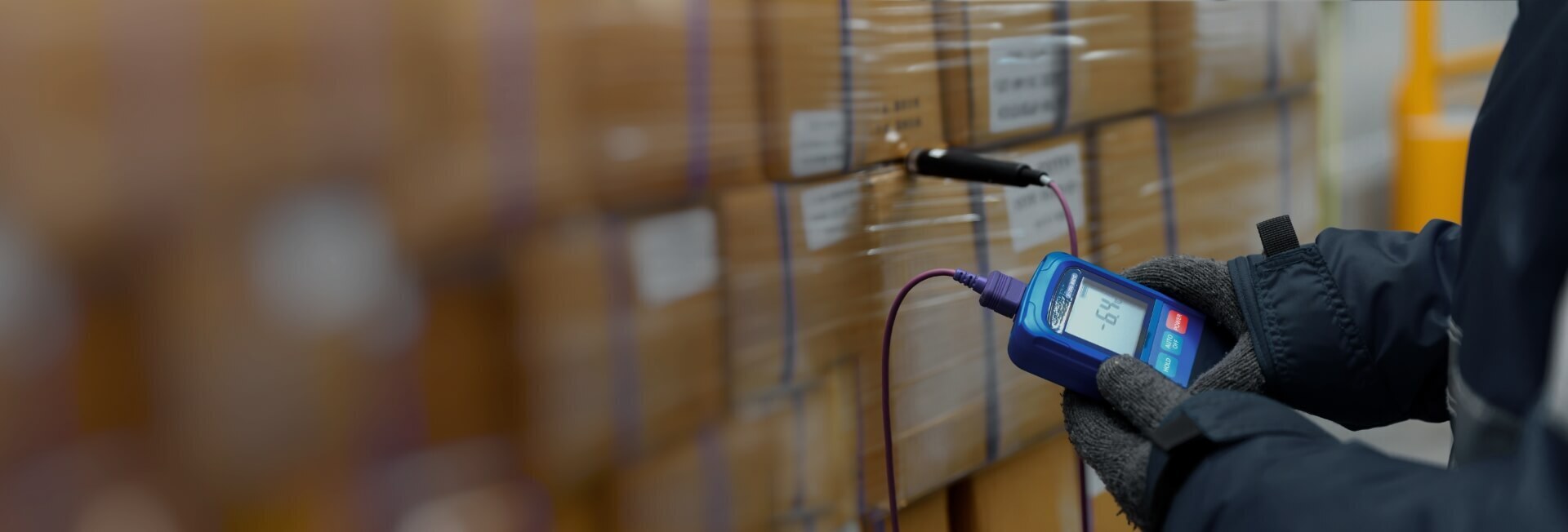
Challenges and barriers to achieving energy efficiency in manufacturing
- Home
- Resources
- Cooling Unit Manufacturing Insights
- Challenges and barriers to achieving energy efficiency in manufacturing
Introduction
Energy efficiency in manufacturing is crucial for both economic and environmental reasons. By reducing energy consumption, manufacturers can lower their operational costs and minimize their carbon footprint. However, achieving energy efficiency in the manufacturing sector is not without its challenges and barriers. This article will explore some of the primary obstacles faced by manufacturers when it comes to implementing energy-efficient practices and provide potential solutions to overcome these challenges.
Challenges in Energy Efficiency
1. Lack of Awareness and Education:
One of the significant challenges in achieving energy efficiency in manufacturing is the lack of awareness and education regarding its benefits and implementation strategies. Many manufacturing companies are unaware of the potential cost savings and environmental advantages associated with energy efficiency measures. Furthermore, there may be a lack of knowledge regarding available technologies and best practices for energy conservation.
To address this challenge, it is crucial to invest in awareness campaigns and educational programs targeting manufacturers. These initiatives can provide information on the benefits of energy efficiency, showcase successful case studies, and offer guidance on implementing energy-saving measures. By raising awareness and providing education, manufacturers can become more informed and motivated to adopt energy-efficient practices.
2. Capital Investment and Return on Investment:
Implementing energy-efficient technologies and upgrading manufacturing processes often requires a significant capital investment. Manufacturers may be hesitant to allocate funds to energy efficiency projects due to concerns about the return on investment (ROI) and the payback period.
To overcome this barrier, it is essential to demonstrate the potential financial benefits of energy efficiency improvements. Conducting a thorough energy audit can help identify areas of improvement and estimate the potential cost savings. Additionally, offering financial incentives, such as grants or tax credits, can encourage manufacturers to invest in energy-efficient technologies. By showcasing the financial advantages and providing financial support, manufacturers can be persuaded to overcome the initial capital investment barrier.
Barriers in Implementation
1. Lack of Technical Expertise:
Implementing energy-efficient practices often requires specialized technical expertise. Manufacturers may lack the necessary knowledge and skills to identify opportunities for energy savings and select the most suitable technologies.
To address this barrier, partnerships with energy consultants or experts can be established. These professionals can conduct energy audits, provide recommendations for energy-saving measures, and assist in the implementation process. Building a network of technical experts can bridge the knowledge gap and enable manufacturers to effectively implement energy-efficient practices.
2. Resistance to Change:
Resistance to change is a common barrier in various industries, including manufacturing. Employees may be resistant to adopting new energy-efficient practices due to unfamiliarity, fear of job displacement, or apprehension about potential disruptions in existing processes.
To overcome this barrier, it is crucial to involve employees in the decision-making process and provide training and support during the transition. Engaging employees in energy-saving initiatives and highlighting the benefits can help alleviate resistance and foster a culture of energy efficiency within the organization. Additionally, offering incentives, such as recognition or rewards, can further motivate employees to embrace energy-efficient practices.
Technological Solutions
1. Advanced Cooling Technology:
Cooling systems play a significant role in manufacturing processes, particularly in industries that require precise temperature control. By adopting advanced cooling technologies, manufacturers can optimize energy consumption and reduce waste.
Custom cooling solutions, such as precision cooling systems, offer enhanced efficiency and control. These systems utilize intelligent controls and sensors to maintain precise temperature levels, minimizing energy consumption and improving overall productivity. By partnering with reliable cooling system manufacturers, manufacturers can access cutting-edge technologies and implement sustainable cooling solutions.
2. Sustainable Cooling Units:
Industrial cooling units are essential for maintaining optimal operating conditions in manufacturing facilities. However, traditional cooling units can be energy-intensive and environmentally harmful.
By investing in eco-friendly cooling units, manufacturers can reduce their energy consumption and environmental impact. Green cooling technology utilizes innovative designs and refrigerants that have a lower global warming potential. These units are designed for energy efficiency and often incorporate features such as variable speed controls and intelligent cooling algorithms.
Manufacturers can also explore the option of retrofitting existing cooling units with energy-efficient components. This approach can provide a cost-effective solution to improve energy efficiency without the need for a complete system overhaul.
Conclusion
Overcoming the challenges and barriers to achieving energy efficiency in manufacturing is crucial for sustainable development and long-term profitability. By raising awareness, providing education, and offering financial incentives, manufacturers can be motivated to invest in energy-efficient practices. Additionally, partnerships with technical experts and the adoption of advanced cooling technologies can further enhance energy efficiency in manufacturing processes. By prioritizing energy efficiency, manufacturers can reduce their environmental impact, lower operational costs, and contribute to a greener and more sustainable future.
Related Blogs
The importance of education and awareness in promoting the adoption of green cooling technology
Read More