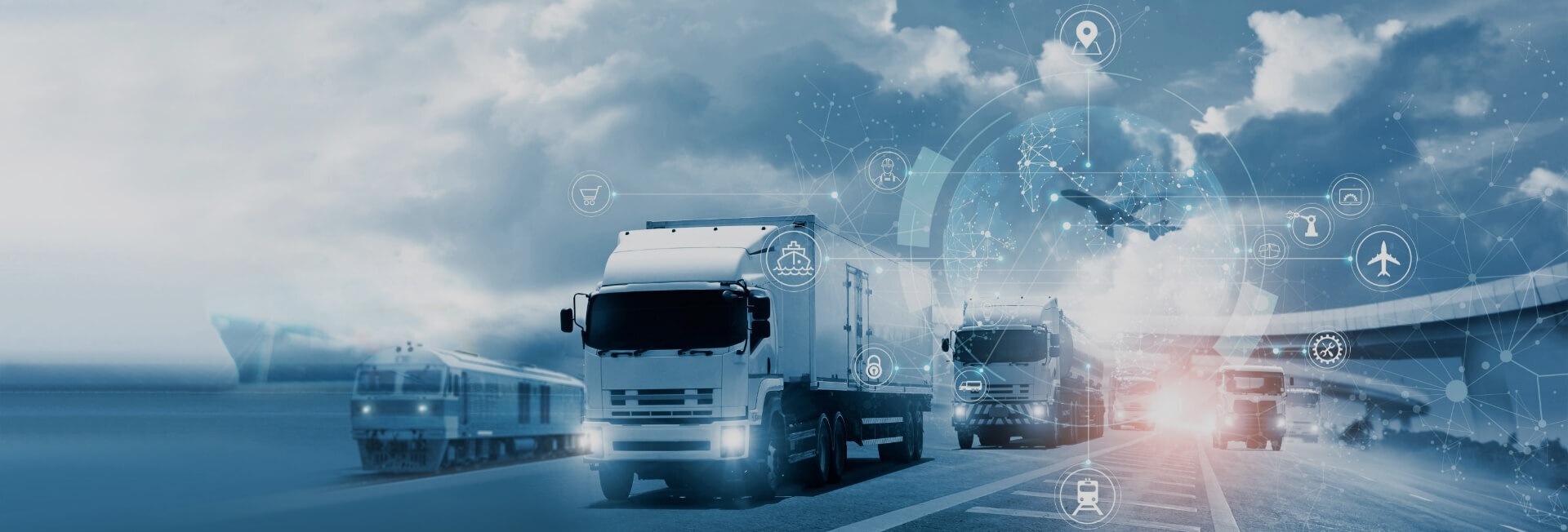
The use of fault detection in optimizing supply chain operations
- Home
- Resources
- CANBus Integration and Application
- The use of fault detection in optimizing supply chain operations
The Use of Fault Detection in Optimizing Supply Chain Operations
In today's fast-paced business environment, supply chain operations play a crucial role in the success of any organization. The efficiency and effectiveness of these operations directly impact the overall performance and profitability of a company. One key aspect of optimizing supply chain operations is the use of fault detection systems to identify and address issues in real-time. In this article, we will explore the importance of fault detection and how it can improve supply chain operations.
What is Fault Detection?
Fault detection refers to the process of identifying deviations or abnormalities in a system or process. In the context of supply chain operations, fault detection systems are used to monitor various components and processes involved in the movement of goods, such as vehicles, equipment, and infrastructure. These systems leverage advanced technologies, such as vehicle telematics and CANBus communication, to collect and analyze data in real-time.
Vehicle telematics involves the use of electronic devices installed in vehicles to capture and transmit data related to their performance and location. This data is then analyzed to identify any potential faults or issues. CANBus communication, on the other hand, enables the exchange of information between different components of a vehicle, such as the engine, transmission, and brakes, via a standardized protocol. By tapping into the CANBus network, fault detection systems can access vital vehicle data and detect any anomalies or malfunctions.
The Benefits of Fault Detection in Supply Chain Operations
Integrating fault detection systems into supply chain operations can yield numerous benefits for businesses. Let's explore some of the key advantages:
1. Early Detection and Prevention of Issues
Fault detection systems enable businesses to identify issues at an early stage, before they escalate into major problems. By continuously monitoring vehicles, equipment, and infrastructure, these systems can detect any anomalies or malfunctions as soon as they occur. This early detection allows for timely intervention and preventive measures, minimizing the risk of downtime, delays, and costly repairs.
For example, a fault detection system installed in a fleet of delivery vehicles can alert the operations team if any vehicle shows signs of engine trouble. Prompt action can then be taken to address the issue, such as scheduling maintenance or replacing the vehicle, to avoid disruptions to the delivery schedule.
2. Improved Safety and Compliance
Fault detection systems play a crucial role in ensuring the safety of supply chain operations. By continuously monitoring vehicles and equipment, these systems can detect any potential safety hazards, such as brake failures or tire blowouts, and alert the appropriate personnel. This allows for timely repairs or replacements, minimizing the risk of accidents and injuries.
In addition, fault detection systems can also help businesses maintain compliance with industry regulations and standards. By monitoring parameters such as emissions and fuel consumption, these systems can ensure that vehicles and equipment meet the required environmental and efficiency standards. This not only helps businesses avoid penalties and fines but also contributes to their reputation as responsible and sustainable organizations.
3. Enhanced Efficiency and Productivity
By identifying and addressing faults in real-time, fault detection systems contribute to improved efficiency and productivity in supply chain operations. By minimizing downtime and delays caused by unexpected breakdowns or malfunctions, these systems help businesses maintain a smooth and uninterrupted workflow.
For example, a fault detection system integrated with a warehouse management system can monitor the performance of automated material handling equipment, such as conveyor belts and robotic pickers. If any issues are detected, such as a malfunctioning conveyor belt, the system can automatically reroute the workflow or notify maintenance personnel for immediate action. This ensures that operations continue seamlessly, maximizing productivity and throughput.
4. Data-Driven Decision Making
Fault detection systems generate a wealth of data related to the performance and health of supply chain components. By leveraging this data, businesses can gain valuable insights and make informed decisions. Analyzing historical data can reveal patterns and trends, helping businesses identify root causes of faults and implement preventive measures.
Furthermore, integrating fault detection systems with other supply chain management tools, such as inventory management or route optimization software, can enable businesses to make real-time adjustments based on the detected faults. For example, if a delivery vehicle is experiencing engine issues, the system can automatically reroute the remaining deliveries to another vehicle to ensure timely delivery and customer satisfaction.
Conclusion
Fault detection systems are invaluable tools for optimizing supply chain operations. By continuously monitoring vehicles, equipment, and infrastructure, these systems enable businesses to detect and address faults in real-time, minimizing downtime, improving safety, enhancing efficiency, and enabling data-driven decision making. As the complexity and scale of supply chain operations continue to grow, the use of fault detection systems will become even more essential for businesses looking to stay competitive and deliver exceptional customer experiences.