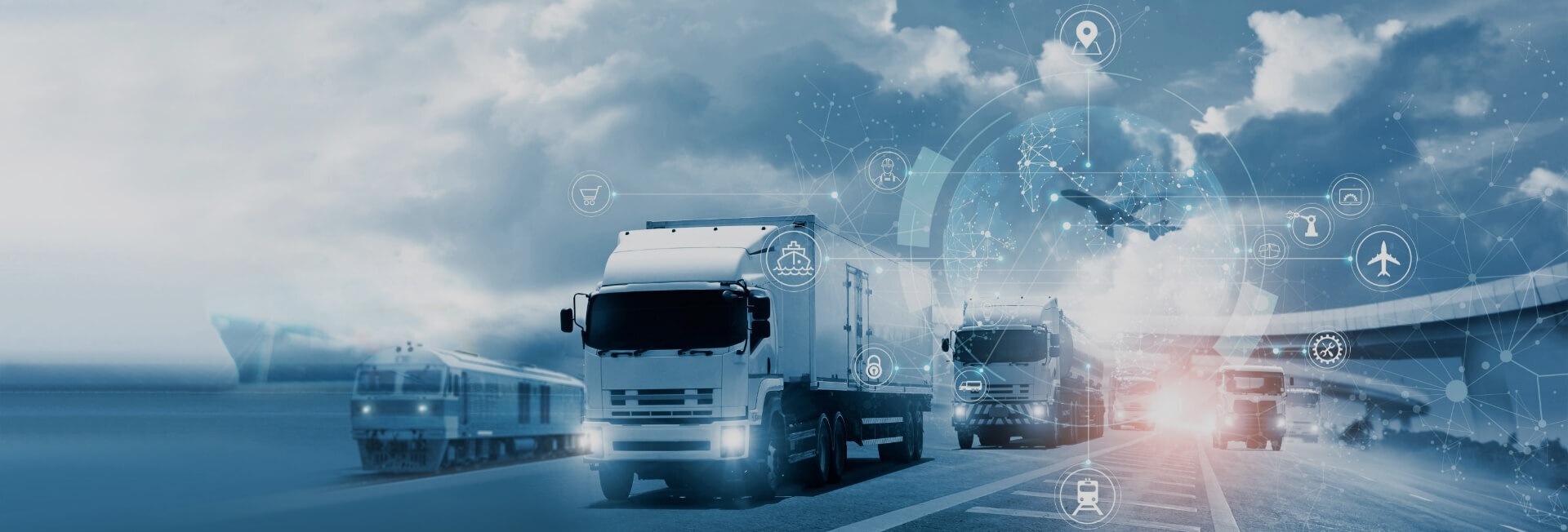
The use of fault detection in improving the reliability of aerospace systems
- Home
- Resources
- CANBus Integration and Application
- The use of fault detection in improving the reliability of aerospace systems
The Importance of Fault Detection in Aerospace Systems
The aerospace industry relies heavily on complex systems and machinery to ensure the safety and efficiency of air travel. With the increasing complexity of these systems, the need for effective fault detection and diagnosis has become crucial. Fault detection refers to the process of identifying and diagnosing faults or anomalies in aerospace systems, while fault diagnosis involves determining the root cause of the fault and providing solutions for its resolution.
Why is Fault Detection Important?
Fault detection plays a vital role in improving the reliability and safety of aerospace systems. By detecting faults at an early stage, potential failures can be prevented or mitigated, reducing the risk of accidents or malfunctions. This is particularly important in the aerospace industry, where even minor faults can have catastrophic consequences. Fault detection also allows for proactive maintenance, as systems can be repaired or replaced before they fail completely, minimizing downtime and increasing overall operational efficiency.
Integration of Fault Detection Systems
Modern aerospace systems are equipped with advanced fault detection systems that utilize various technologies and techniques to monitor and analyze system performance. One such technology is vehicle telematics, which involves the collection and analysis of data from onboard sensors and systems. Vehicle telematics can provide real-time information about the health and performance of aerospace systems, enabling early detection of faults and proactive maintenance.
Another important aspect of fault detection is the integration of vehicle diagnostics and CANBus communication. The CANBus (Controller Area Network) is a communication network used in aerospace systems to facilitate communication between various components and subsystems. By integrating vehicle diagnostics with CANBus communication, faults can be detected and diagnosed more efficiently, as diagnostic information can be accessed and analyzed directly from the CANBus network.
Fault detection systems in aerospace systems often rely on advanced algorithms and machine learning techniques to analyze the vast amount of data collected from various sensors and systems. These algorithms can identify patterns and anomalies in the data, allowing for the early detection of faults. Additionally, fault detection systems can also incorporate predictive analytics to anticipate potential failures based on historical data, further enhancing the reliability and safety of aerospace systems.
The Benefits of Remote Vehicle Diagnostics
Remote vehicle diagnostics is another key technology that is revolutionizing fault detection in aerospace systems. With remote vehicle diagnostics, real-time data from aircraft or spacecraft can be transmitted to a central monitoring station, where it can be analyzed and interpreted by experts. This allows for immediate detection and diagnosis of faults, regardless of the location of the aircraft or spacecraft.
Remote vehicle diagnostics offers several benefits in terms of fault detection. First, it enables faster response times, as faults can be detected and diagnosed in real-time. This allows for prompt action to be taken, such as rerouting an aircraft or implementing necessary repairs. Second, remote vehicle diagnostics can provide valuable insights into the overall health and performance of aerospace systems, allowing for proactive maintenance and optimization. By monitoring and analyzing data from multiple aircraft or spacecraft, trends and patterns can be identified, leading to more effective fault detection and prevention strategies.
The Future of Fault Detection in Aerospace Systems
The field of fault detection in aerospace systems is constantly evolving, driven by advancements in technology and the increasing complexity of aerospace systems. One area of development is the integration of fault detection systems with artificial intelligence (AI) and machine learning (ML) algorithms. AI and ML can analyze large datasets and identify complex patterns and anomalies, allowing for more accurate and efficient fault detection.
Another area of focus is the integration of fault detection systems with fleet data integration. Fleet data integration involves aggregating data from multiple aircraft or spacecraft to gain a comprehensive view of the entire fleet's performance. By integrating fault detection systems with fleet data integration, trends and patterns can be identified across multiple systems, leading to more effective fault detection and prevention strategies.
Furthermore, advancements in CANBus system integration and diagnostic tools are also driving improvements in fault detection. CANBus diagnostic tools allow for the direct access and analysis of diagnostic information from the CANBus network, enabling more efficient and accurate fault detection. CANBus system integration ensures seamless communication between various components and subsystems, facilitating the exchange of diagnostic information and enhancing overall fault detection capabilities.
Conclusion
Fault detection is a critical aspect of ensuring the reliability and safety of aerospace systems. By detecting faults at an early stage and diagnosing their root causes, potential failures can be prevented or mitigated, reducing the risk of accidents or malfunctions. Integration of fault detection systems with vehicle telematics, CANBus communication, and remote vehicle diagnostics has revolutionized the way faults are detected and diagnosed in aerospace systems. As technology continues to advance, the future of fault detection in aerospace systems holds great promise, with advancements in AI, ML, fleet data integration, and CANBus system integration driving further improvements in fault detection capabilities.