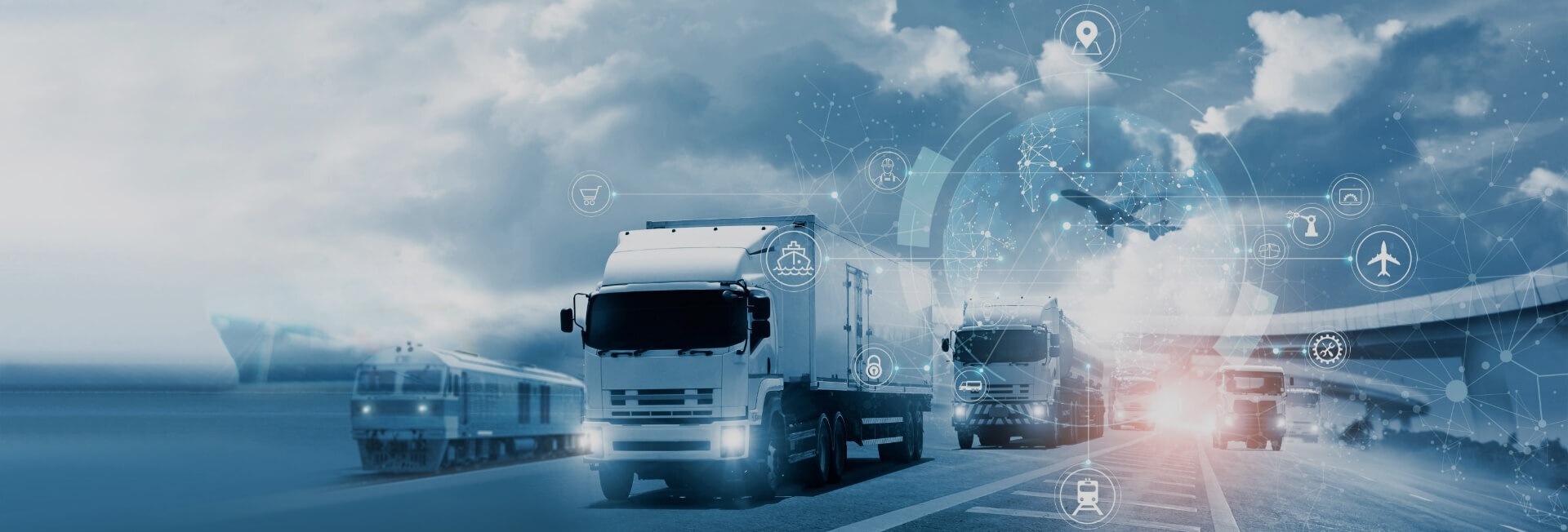
The role of fault detection in improving the performance of industrial pumps
- Home
- Resources
- CANBus Integration and Application
- The role of fault detection in improving the performance of industrial pumps
The Role of Fault Detection in Improving the Performance of Industrial Pumps
Industrial pumps are used in a wide range of applications, from water supply and wastewater treatment to oil and gas refining. These pumps play a crucial role in ensuring the smooth operation of various industrial processes. However, like any mechanical equipment, pumps are prone to faults and failures that can lead to costly downtime and production losses. This is where fault detection systems come into play.
What is Fault Detection?
Fault detection is the process of identifying and diagnosing faults or abnormalities in a system. In the case of industrial pumps, fault detection involves monitoring various parameters and performance indicators to detect any deviations from normal operating conditions. By detecting faults early on, maintenance teams can take proactive measures to address the issues before they escalate into more serious problems.
Fault detection systems leverage advanced technologies such as sensors, data analytics, and machine learning algorithms to continuously monitor the performance of industrial pumps. These systems collect data from various sensors installed on the pumps and analyze it in real-time to identify any anomalies. By comparing the current performance data with historical data or predefined thresholds, these systems can detect deviations and trigger alerts or notifications.
Now, let's explore some of the key benefits of using advanced fault detection systems in industrial pump applications.
Improved Efficiency
One of the main advantages of using fault detection systems is improved efficiency. By monitoring and analyzing pump performance data, these systems can identify inefficiencies or deviations from optimal operating conditions. For example, a fault detection system can detect a drop in pump efficiency due to worn-out impellers or clogged filters. By addressing these issues promptly, maintenance teams can restore the pump's efficiency and prevent energy wastage.
Furthermore, fault detection systems can also identify performance degradation over time, allowing maintenance teams to schedule preventive maintenance activities. By replacing worn-out components or conducting maintenance tasks at the right time, operators can ensure that pumps operate at their peak efficiency, reducing energy consumption and operational costs.
Reduced Downtime
Fault detection systems can significantly reduce downtime by providing early warnings about potential failures. By continuously monitoring pump performance, these systems can detect signs of impending faults or failures, such as abnormal vibrations or temperature spikes. Maintenance teams can then take proactive measures to address the issues before they lead to unexpected breakdowns or production interruptions.
In addition, fault detection systems can also provide insights into the root causes of failures, allowing maintenance teams to implement preventive measures. For example, if a fault detection system detects frequent bearing failures in a pump, it can indicate an underlying lubrication issue. By addressing the root cause, operators can prevent future failures and extend the lifespan of the pump.
Optimized Maintenance Strategies
Traditional maintenance strategies often rely on scheduled maintenance activities or reactive repairs. However, these approaches can be inefficient and costly. Scheduled maintenance may result in unnecessary downtime and maintenance costs, while reactive repairs can lead to production losses and expensive emergency repairs.
Fault detection systems enable a more proactive and data-driven approach to maintenance. By continuously monitoring pump performance and detecting faults in real-time, these systems provide valuable insights into the condition of the pumps. Maintenance teams can use this information to prioritize maintenance activities based on the actual condition of the equipment.
For example, if a fault detection system detects a worn-out bearing in a pump, maintenance teams can schedule a bearing replacement during a planned maintenance window, rather than waiting for a failure to occur. This approach minimizes downtime and reduces the risk of unplanned breakdowns.
Enhanced Safety
Fault detection systems also play a crucial role in enhancing the safety of industrial pump applications. By monitoring pump performance and detecting faults, these systems can prevent potentially dangerous situations. For example, a fault detection system can detect a leak in a pump's sealing system and trigger an alarm to alert operators. This early warning allows operators to take immediate action to prevent further damage or safety hazards.
Furthermore, fault detection systems can also monitor critical parameters such as pump temperature and vibration levels. If these parameters exceed safe limits, the system can automatically shut down the pump to prevent catastrophic failures or accidents. By proactively addressing potential safety risks, fault detection systems help create a safer working environment for operators and reduce the risk of accidents.
Conclusion
Fault detection systems play a crucial role in improving the performance and reliability of industrial pumps. By continuously monitoring pump performance, these systems can detect faults and deviations from normal operating conditions, allowing maintenance teams to take proactive measures. The benefits of using advanced fault detection systems include improved efficiency, reduced downtime, optimized maintenance strategies, and enhanced safety. With the help of these systems, operators can ensure the smooth operation of industrial pumps and minimize costly downtime and production losses.