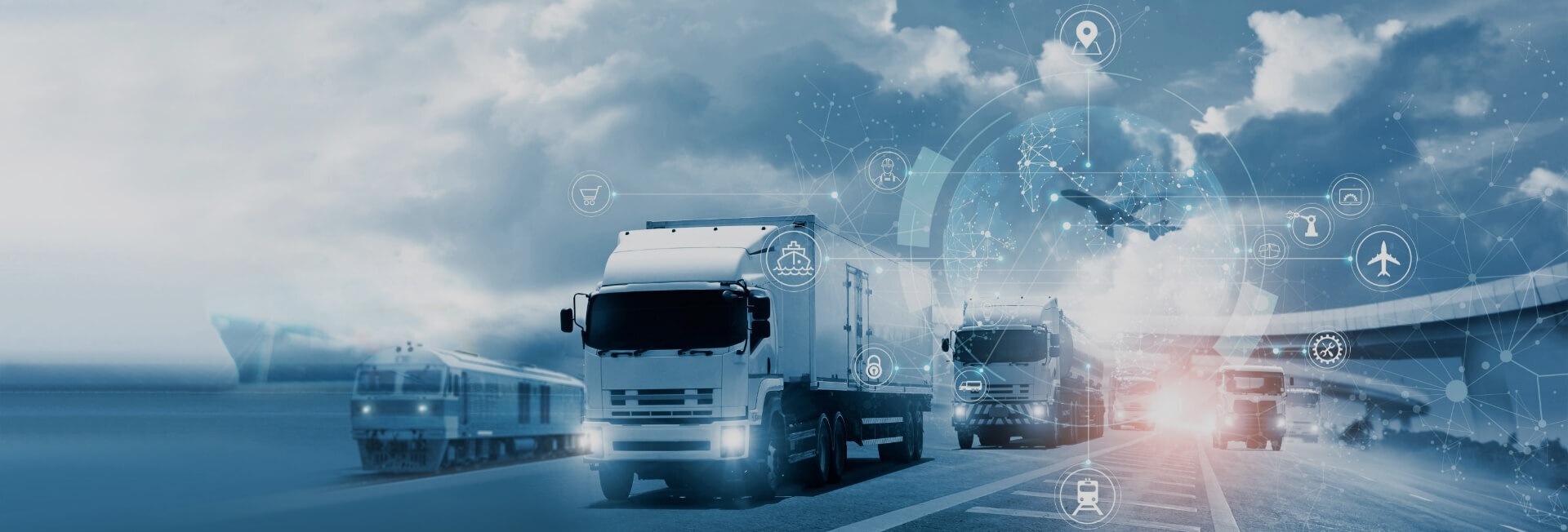
The role of fault detection in improving the performance of industrial boilers
- Home
- Resources
- CANBus Integration and Application
- The role of fault detection in improving the performance of industrial boilers
The Importance of Fault Detection in Improving Industrial Boiler Performance
Industrial boilers play a crucial role in various industries, providing the necessary heat and steam for a wide range of processes. However, like any complex machinery, boilers are prone to faults and issues that can impact their performance and efficiency. This is where fault detection systems come into play, offering a proactive approach to identify and resolve problems before they escalate.
What is Fault Detection?
Fault detection refers to the process of monitoring and analyzing the behavior and performance of a system to identify any deviations or abnormalities. In the context of industrial boilers, fault detection systems continuously monitor various parameters such as temperature, pressure, flow rate, and fuel consumption to detect any anomalies that may indicate a fault or potential issue.
The Benefits of Fault Detection in Industrial Boilers
Fault detection systems offer several benefits when it comes to improving the performance of industrial boilers:
1. Early Detection and Prevention of Issues
By continuously monitoring the boiler's parameters, fault detection systems can quickly identify any deviations from normal operating conditions. This early detection allows for proactive maintenance and troubleshooting, preventing minor issues from escalating into major problems. Timely intervention can help avoid costly repairs, reduce downtime, and optimize the overall performance of the boiler.
2. Optimization of Efficiency
Fault detection systems provide real-time data on the boiler's performance, allowing operators to identify inefficiencies and make adjustments accordingly. By optimizing the boiler's operation parameters, such as combustion air-fuel ratio and excess oxygen levels, the system can achieve higher energy efficiency and reduce fuel consumption. This not only reduces operating costs but also contributes to environmental sustainability.
3. Enhanced Safety
Fault detection systems play a crucial role in ensuring the safety of industrial boiler operations. By continuously monitoring critical parameters, such as pressure and temperature, these systems can detect any abnormal conditions that may pose a safety risk. In case of an emergency or potential hazard, the system can trigger alarms or shutdown procedures to prevent accidents and protect both personnel and equipment.
4. Data-Driven Decision Making
Fault detection systems generate a wealth of data related to the boiler's performance and behavior. This data can be analyzed and used to gain valuable insights into the system's operation, identify patterns, and make data-driven decisions. By understanding the root causes of faults and issues, operators can implement targeted maintenance and optimization strategies, leading to improved performance and reliability.
Implementing Fault Detection Systems
Implementing a fault detection system for industrial boilers involves several key steps:
1. Sensor Installation
The first step is to install appropriate sensors to measure and monitor the boiler's key parameters. These sensors can include temperature sensors, pressure sensors, flow meters, and gas analyzers. The sensors should be strategically placed to capture accurate and representative data.
2. Data Acquisition
Once the sensors are installed, the next step is to establish a data acquisition system to collect and store the sensor data. This can be achieved through a dedicated data acquisition unit or by integrating the boiler's control system with the fault detection system.
3. Data Analysis and Interpretation
The collected data is then analyzed using advanced algorithms and techniques to identify any deviations or abnormalities. This analysis can involve statistical analysis, machine learning algorithms, or rule-based systems. The goal is to distinguish between normal operating conditions and potential faults or issues.
4. Alarm Generation and Reporting
Based on the analysis results, the fault detection system can generate alarms or notifications to alert operators about any detected faults or abnormal conditions. These alarms can be displayed on a control panel or sent via email or SMS to the relevant personnel. Additionally, comprehensive reports can be generated to provide detailed insights into the system's performance and any detected faults.
Conclusion
Fault detection systems play a critical role in improving the performance and reliability of industrial boilers. By continuously monitoring key parameters and analyzing data, these systems can detect and prevent faults, optimize efficiency, enhance safety, and enable data-driven decision making. Implementing a fault detection system for industrial boilers can result in significant cost savings, improved productivity, and a more sustainable operation.