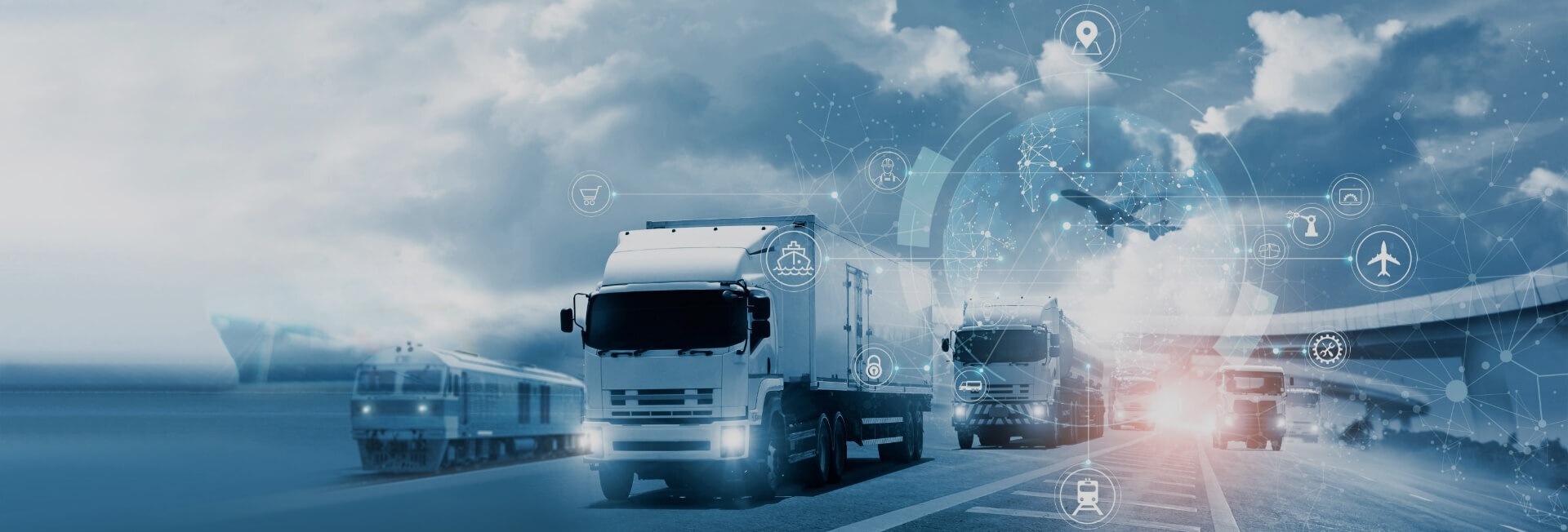
The role of fault detection in improving the efficiency of manufacturing processes
- Home
- Resources
- CANBus Integration and Application
- The role of fault detection in improving the efficiency of manufacturing processes
The Role of Fault Detection in Improving Manufacturing Efficiency
In the world of manufacturing, efficiency is key. Every minute, every second counts when it comes to optimizing production outcomes and meeting customer demands. One crucial factor that can significantly impact manufacturing efficiency is the ability to detect and address faults in the production process. Fault detection plays a vital role in ensuring that manufacturing operations run smoothly, minimizing downtime, reducing waste, and ultimately improving overall efficiency.
What is Fault Detection?
Fault detection refers to the process of identifying abnormalities or deviations from the expected performance in a manufacturing system. These abnormalities can range from minor issues to more severe problems that can disrupt the entire production process. By detecting faults early on, manufacturers can take immediate action to rectify the issue and prevent further damage or delays.
Traditionally, fault detection relied heavily on manual monitoring and inspection. However, with advancements in technology, manufacturers now have access to various automated systems and tools that can streamline the process and provide real-time insights into the health of their production systems.
The Role of Vehicle Diagnostics in Manufacturing
One area where fault detection plays a critical role is in the automotive manufacturing industry. Vehicle diagnostics have become an essential part of the production process, allowing manufacturers to monitor and analyze the performance of their vehicles at different stages of production. By integrating vehicle telematics and remote diagnostics systems, manufacturers can gain valuable insights into the health and performance of their vehicles, enabling them to proactively detect and address any faults or issues that may arise.
The use of CANBus communication systems has revolutionized vehicle diagnostics by providing a standardized interface for collecting and transmitting data from various sensors and modules within a vehicle. CANBus, short for Controller Area Network, is a communication protocol that allows different electronic devices within a vehicle to communicate with each other. By leveraging CANBus communication, manufacturers can integrate fault detection systems directly into their production processes, enabling real-time monitoring and analysis of vehicle health.
Benefits of Fault Detection in Manufacturing
The integration of fault detection systems in manufacturing processes offers several benefits, all of which contribute to improving efficiency and optimizing production outcomes. Here are some key advantages:
1. Minimizing Downtime
One of the most significant impacts of faults in manufacturing is the potential downtime they can cause. When a fault occurs, production may come to a halt while the issue is identified and resolved. The longer it takes to detect and address the fault, the more downtime is incurred, leading to delays in delivery and increased costs. By implementing an effective fault detection system, manufacturers can quickly identify faults and take immediate action, minimizing downtime and ensuring smooth operations.
2. Reducing Waste
Faults in the manufacturing process can result in the production of defective or substandard products. These products often need to be discarded or reworked, leading to increased waste and additional costs. By detecting faults early on, manufacturers can prevent the production of faulty products, reducing waste and optimizing resource utilization.
3. Improving Product Quality
Fault detection systems not only help identify faults but also provide insights into the root causes of these issues. By analyzing the data collected from the manufacturing process, manufacturers can identify trends and patterns that contribute to faults and take proactive measures to address them. This continuous improvement approach helps improve overall product quality and customer satisfaction.
4. Enhancing Predictive Maintenance
By monitoring the health and performance of manufacturing equipment and systems, fault detection systems can provide valuable data for predictive maintenance. Predictive maintenance involves analyzing real-time data to identify potential faults or failures before they occur. By addressing maintenance needs proactively, manufacturers can prevent unexpected breakdowns and optimize equipment performance, further improving efficiency.
Implementing Fault Detection Systems
Implementing an effective fault detection system requires careful planning and consideration. Here are some key steps to take:
1. Identify Critical Control Points
Start by identifying the critical control points in your manufacturing process where faults are most likely to occur. These could be specific stages of production, machinery, or components that are prone to issues. By focusing on these critical points, you can prioritize your fault detection efforts and allocate resources accordingly.
2. Select Suitable Fault Detection Tools
There are various fault detection tools and technologies available in the market, ranging from simple sensor-based systems to advanced machine learning algorithms. Consider the specific needs of your manufacturing process and choose tools that align with your requirements. For example, if you're dealing with complex data sets, you may need advanced analytics tools to process and analyze the data effectively.
3. Integrate Fault Detection into the Production Process
To maximize the benefits of fault detection, it's crucial to integrate the system directly into your production process. This integration allows for real-time monitoring and analysis, enabling immediate action when faults are detected. Consider leveraging CANBus communication systems to interface with your production equipment and collect data seamlessly.
4. Train and Educate Staff
Implementing a fault detection system requires buy-in from your entire workforce. Train and educate your staff on the importance of fault detection and how to effectively utilize the tools and systems in place. Encourage a culture of continuous improvement and empower your employees to report and address faults as soon as they are identified.
Conclusion
Fault detection plays a crucial role in improving the efficiency of manufacturing processes. By detecting faults early on, manufacturers can minimize downtime, reduce waste, improve product quality, and enhance predictive maintenance. Integrating fault detection systems, particularly through CANBus communication, allows for real-time monitoring and analysis, enabling immediate action when faults are detected. As technology continues to advance, fault detection systems will play an even more significant role in optimizing manufacturing efficiency and driving continuous improvement.