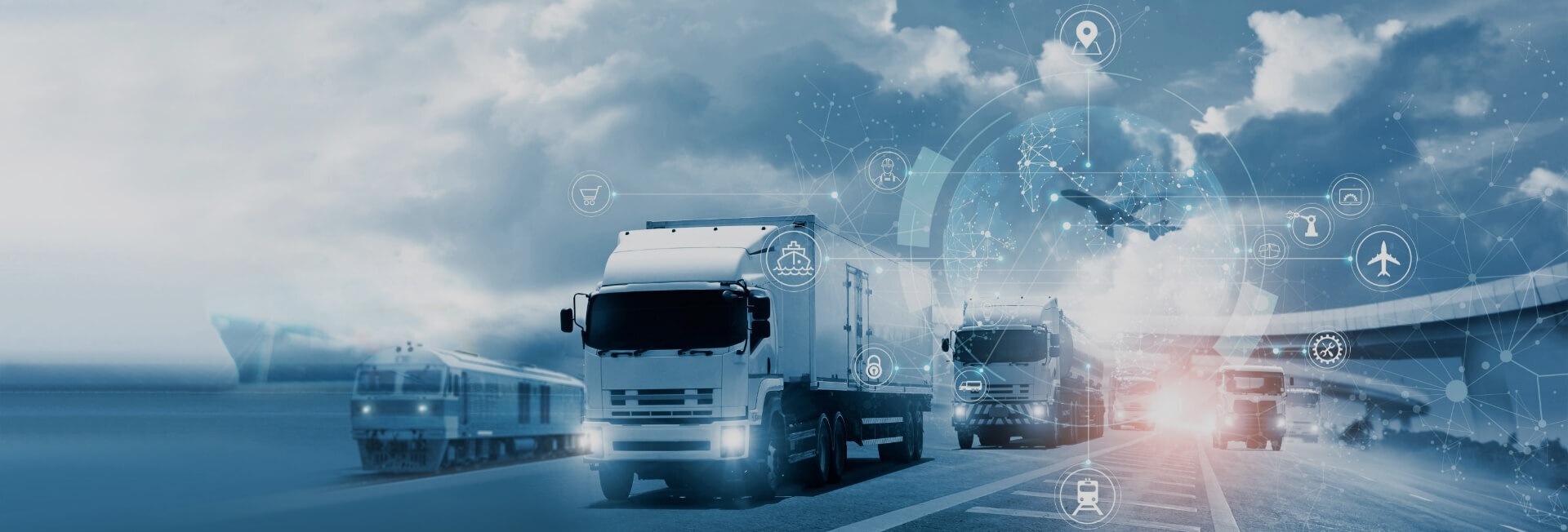
The role of fault detection in enhancing the performance of industrial robots
- Home
- Resources
- CANBus Integration and Application
- The role of fault detection in enhancing the performance of industrial robots
The Importance of Fault Detection in Industrial Robots
Industrial robots have revolutionized the manufacturing industry by increasing efficiency, precision, and productivity. These advanced machines are capable of performing repetitive tasks with high accuracy and speed. However, like any other complex system, industrial robots are prone to faults and failures. Fault detection plays a crucial role in enhancing the performance of these robots and ensuring uninterrupted operations.
What is Fault Detection?
Fault detection refers to the process of identifying abnormalities or deviations from the normal functioning of a system. In the context of industrial robots, fault detection involves monitoring various parameters and sensors to identify any potential issues or malfunctions. By detecting faults early on, it becomes possible to take corrective actions and prevent further damage or downtime.
The Role of Fault Detection in Industrial Robots
Fault detection plays a vital role in maximizing the performance and efficiency of industrial robots. Here are some key benefits of incorporating fault detection systems:
1. Minimizing Downtime
Industrial robots are often deployed in critical manufacturing processes where even a few minutes of downtime can result in significant losses. By implementing a robust fault detection system, any potential issues or malfunctions can be identified before they escalate into major problems. This allows for timely repairs or maintenance, minimizing downtime and ensuring uninterrupted production.
2. Improving Safety
Safety is a paramount concern in industrial settings. Fault detection systems can help identify safety-related issues, such as sensor failures or abnormal behavior, which could pose a risk to human operators or other equipment. By detecting these faults, appropriate actions can be taken to eliminate or mitigate the risks, ensuring a safer working environment.
3. Enhancing Product Quality
Faulty robots can lead to subpar product quality, resulting in customer dissatisfaction and potential financial losses. Fault detection systems allow for real-time monitoring of critical parameters, such as positioning accuracy or force exertion. By identifying deviations from the expected values, corrective actions can be initiated to maintain consistent product quality.
4. Optimizing Maintenance
Traditional maintenance approaches often rely on scheduled maintenance or reactive repairs. This can result in unnecessary downtime or the occurrence of unexpected faults. Fault detection systems enable predictive maintenance by continuously monitoring the health of the robot and its components. By analyzing data from various sensors and systems, maintenance activities can be optimized, reducing costs and increasing overall efficiency.
Implementing Fault Detection in Industrial Robots
Implementing an effective fault detection system in industrial robots requires a combination of hardware and software solutions. The following are some key components and techniques used in fault detection:
1. CANBus Communication
CANBus (Controller Area Network Bus) communication is a widely used standard in industrial automation. It enables seamless communication between various devices and sensors in a networked environment. By integrating fault detection systems with CANBus communication, real-time data can be exchanged, allowing for quick identification of faults and abnormalities.
2. Fault Detection Algorithms
Fault detection algorithms analyze data from sensors and systems to identify deviations from expected behavior. These algorithms can be based on statistical models, machine learning techniques, or rule-based approaches. By continuously monitoring sensor data and comparing it with predefined thresholds or patterns, potential faults can be detected and flagged for further analysis.
3. Remote Monitoring and Diagnostics
Remote monitoring and diagnostics enable real-time monitoring of industrial robots from a centralized location. This allows for proactive fault detection and troubleshooting, without the need for physical presence near the robot. Remote monitoring also enables the collection of valuable data for analysis and continuous improvement of fault detection algorithms.
4. Redundancy and Fault Tolerance
Redundancy and fault tolerance techniques can be implemented to enhance the reliability and fault detection capabilities of industrial robots. By incorporating redundant sensors, controllers, or actuators, the system can continue to operate even in the event of a failure. Fault tolerance mechanisms ensure that the robot can detect and compensate for faults, minimizing the impact on overall performance.
The Future of Fault Detection in Industrial Robots
The field of fault detection in industrial robots is continuously evolving, driven by advancements in technology and the need for improved efficiency and productivity. Here are some trends and developments that will shape the future of fault detection:
1. Artificial Intelligence and Machine Learning
Artificial intelligence (AI) and machine learning (ML) techniques are increasingly being used in fault detection systems. These technologies enable robots to learn from data, identify complex patterns, and make informed decisions. AI-powered fault detection algorithms can adapt to changing conditions, improving the accuracy and effectiveness of fault detection.
2. Sensor Fusion
Sensor fusion involves combining data from multiple sensors to obtain a more accurate and comprehensive understanding of the robot's behavior. By fusing data from various sensors, such as vision systems, force sensors, or temperature sensors, a more holistic view of the robot's performance can be obtained. This enables more precise fault detection and diagnosis.
3. Cloud-Based Fault Detection
Cloud computing and connectivity have opened up new possibilities for fault detection in industrial robots. By leveraging the power of the cloud, robots can transmit real-time data to remote servers for analysis. Cloud-based fault detection systems enable centralized monitoring, analysis, and diagnostics, providing a scalable and cost-effective solution for fault detection.
4. Predictive Analytics
Predictive analytics involves using historical data and statistical models to predict future events or behaviors. In the context of fault detection, predictive analytics can help anticipate potential faults or failures based on historical data patterns. By analyzing large volumes of data, predictive analytics algorithms can provide valuable insights for proactive maintenance and fault prevention.
Conclusion
Fault detection is a critical aspect of ensuring the reliable and efficient operation of industrial robots. By implementing robust fault detection systems, manufacturers can minimize downtime, enhance safety, improve product quality, and optimize maintenance activities. As technology continues to advance, the future of fault detection in industrial robots holds great promise, with the integration of AI, sensor fusion, cloud computing, and predictive analytics.
By leveraging these advancements, manufacturers can unlock new levels of performance and productivity in their industrial robotics operations.