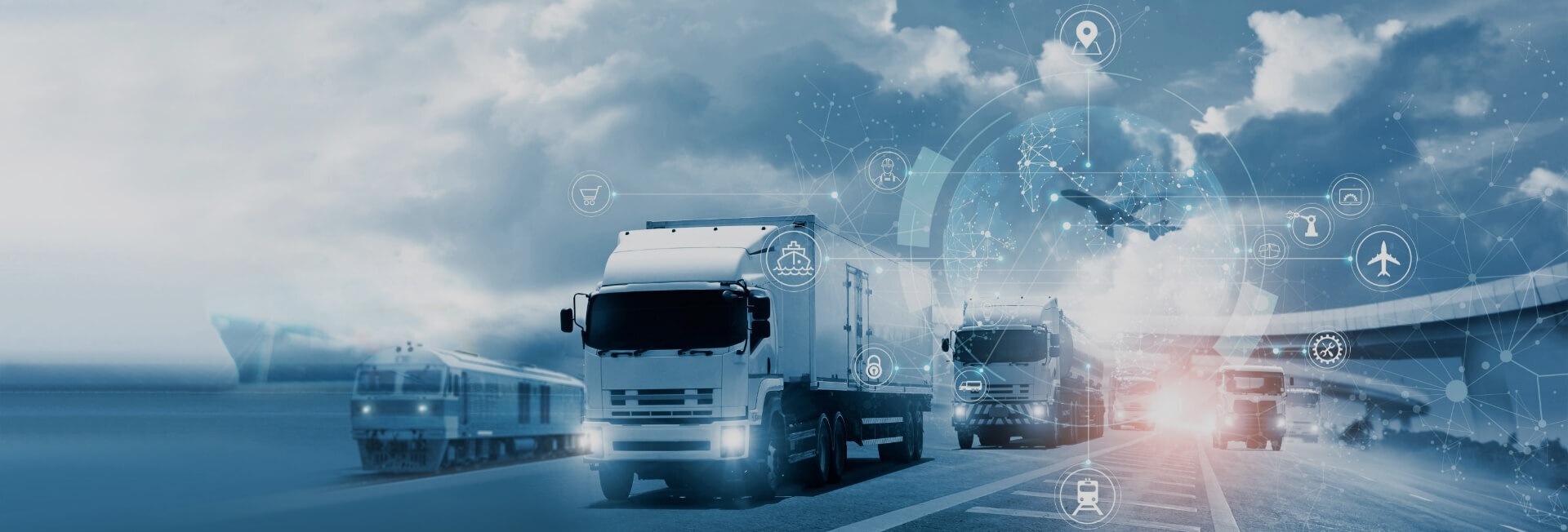
The role of fault detection in enhancing the performance of industrial compressors
- Home
- Resources
- CANBus Integration and Application
- The role of fault detection in enhancing the performance of industrial compressors
The Importance of Fault Detection in Industrial Compressors
Industrial compressors play a crucial role in various industries, including manufacturing, oil and gas, and automotive. These machines are responsible for converting power into potential energy stored in compressed air, which is then used for various applications such as powering pneumatic tools, operating machinery, and even supplying breathable air in certain environments.
Understanding Industrial Compressor Faults
Like any other mechanical system, industrial compressors are prone to faults and failures. These faults can lead to downtime, inefficiency, increased maintenance costs, and even safety hazards. Therefore, it is essential to have a robust fault detection system in place to identify and address any issues promptly.
Faults in industrial compressors can manifest in various ways, including abnormal vibrations, excessive noise, irregular pressure levels, and increased energy consumption. These faults can be caused by factors such as worn-out components, lubrication issues, leaks, and electrical problems.
The Role of Fault Detection in Enhancing Performance
Fault detection systems are designed to monitor the performance of industrial compressors in real-time and identify any deviations from normal operating conditions. By detecting faults early on, these systems help prevent further damage, minimize downtime, and improve overall compressor performance.
Here are some key ways in which fault detection enhances the performance of industrial compressors:
1. Early Fault Detection
Fault detection systems use various sensors and monitoring techniques to continuously measure parameters such as temperature, pressure, vibration, and power consumption. By analyzing these data points, the system can detect anomalies and potential faults before they escalate into major issues.
Early fault detection allows maintenance teams to take proactive measures, such as scheduling maintenance or replacing worn-out components, before a failure occurs. This not only prevents costly breakdowns but also ensures that the compressor operates at its optimal performance level.
2. Improved Energy Efficiency
Faults in industrial compressors can significantly impact energy efficiency. For example, leaks in the compressed air system can lead to wasted energy and increased power consumption. By detecting and addressing these faults, a fault detection system can help optimize energy usage and reduce operational costs.
Additionally, a fault detection system can monitor the compressor's power consumption and identify any abnormal patterns or deviations. This information can be used to optimize the compressor's performance and ensure that it operates within its designated energy efficiency parameters.
3. Preventive Maintenance
Regular maintenance is essential for the smooth operation of industrial compressors. However, traditional maintenance approaches, such as time-based or usage-based schedules, can be inefficient and costly.
A fault detection system enables condition-based maintenance, where maintenance activities are planned based on the actual condition of the compressor rather than pre-determined schedules. By continuously monitoring the compressor's performance and health, the system can provide real-time insights into the optimal timing for maintenance activities.
4. Enhanced Safety
Faults in industrial compressors can pose significant safety risks, especially in hazardous environments. For example, a leak in the compressed air system can lead to the accumulation of flammable gases, increasing the risk of fire or explosion.
A fault detection system can quickly identify potential safety hazards and trigger appropriate alarms or shutdown procedures. This helps prevent accidents and ensures the safety of personnel working with or around the compressor.
Conclusion
Fault detection plays a vital role in enhancing the performance of industrial compressors. By detecting faults early on, these systems enable proactive maintenance, improve energy efficiency, optimize maintenance schedules, and enhance overall safety.
Implementing a robust fault detection system is essential for industries relying on industrial compressors to ensure uninterrupted operations, reduce maintenance costs, and maximize productivity.