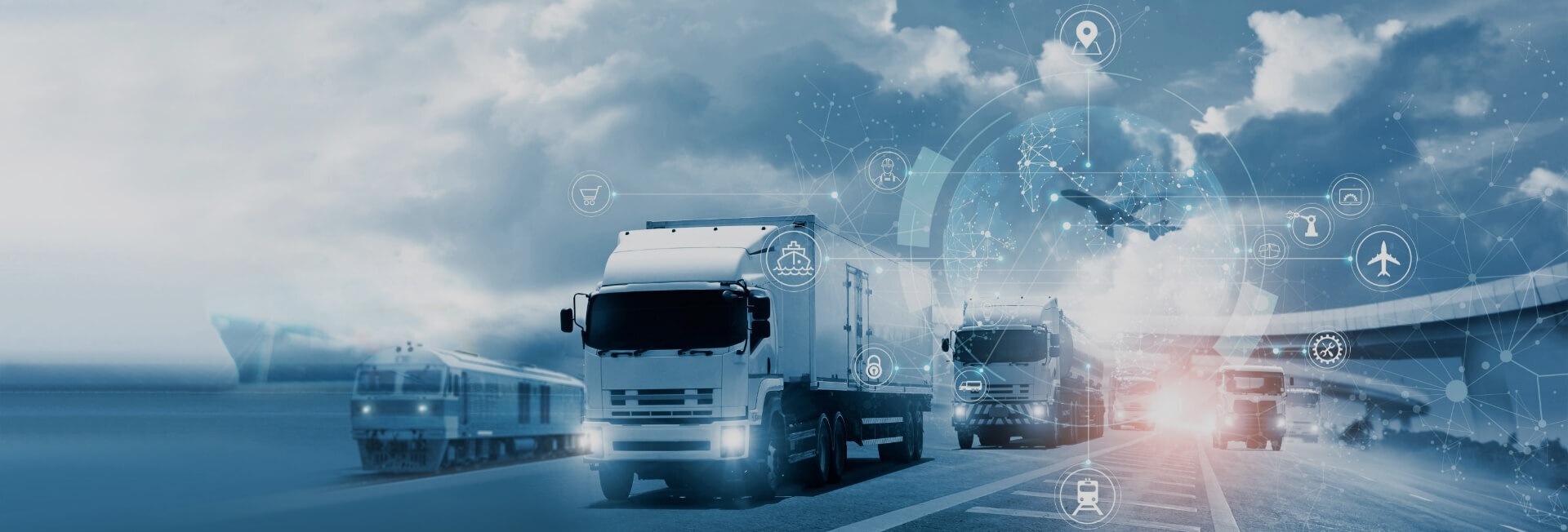
The importance of fault detection in manufacturing processes
- Home
- Resources
- CANBus Integration and Application
- The importance of fault detection in manufacturing processes
The Importance of Fault Detection in Manufacturing Processes
In the world of manufacturing, efficiency and productivity are key. Any faults or errors in the manufacturing process can lead to wasted time, resources, and ultimately, lost profits. That's why fault detection is a crucial aspect of modern manufacturing processes. By implementing effective fault detection systems, manufacturers can identify and address issues before they cause major problems.
What is Fault Detection?
Fault detection is the process of identifying and diagnosing faults or anomalies in a manufacturing process. These faults can range from equipment malfunctions to human errors, and they can have a significant impact on the quality and efficiency of the manufacturing process. Fault detection systems use various techniques and technologies to monitor and analyze data in real-time, allowing manufacturers to identify and address issues as they arise.
The Benefits of Fault Detection
Implementing a robust fault detection system in a manufacturing process can provide numerous benefits, including:
1. Improved Efficiency
Fault detection systems allow manufacturers to identify and address issues in real-time, minimizing downtime and maximizing productivity. By detecting faults early on, manufacturers can take immediate corrective action, reducing the impact on production and ensuring that the manufacturing process runs smoothly.
2. Reduced Costs
Identifying and addressing faults early can also help manufacturers save on costs. By preventing major faults or breakdowns, manufacturers can avoid costly repairs or equipment replacements. Additionally, by optimizing the manufacturing process and minimizing downtime, manufacturers can reduce waste and save on energy and resources.
3. Enhanced Product Quality
Fault detection systems can help manufacturers ensure that their products meet the highest quality standards. By detecting faults early on, manufacturers can take corrective actions to prevent defective products from reaching the market. This not only helps protect the manufacturer's reputation but also ensures customer satisfaction and loyalty.
4. Increased Safety
Faults in the manufacturing process can pose safety risks for both workers and consumers. By implementing effective fault detection systems, manufacturers can identify and address potential safety hazards before they cause harm. This helps create a safer working environment for employees and ensures that products meet safety regulations and standards.
Implementing Fault Detection Systems
There are various techniques and technologies available for implementing fault detection systems in manufacturing processes. One such technology is CANBus communication, which allows for real-time monitoring and analysis of data from various devices and sensors in the manufacturing process.
CANBus, short for Controller Area Network Bus, is a communication protocol commonly used in automotive and industrial applications. It enables devices and sensors to communicate and share data efficiently and reliably. By integrating CANBus communication into the manufacturing process, manufacturers can collect and analyze data from different components and systems, allowing for effective fault detection and diagnosis.
CANBus diagnostic tools and devices can be used to monitor parameters such as temperature, pressure, voltage, and more. By setting up thresholds and alarms, manufacturers can be alerted when values exceed acceptable ranges, indicating potential faults or anomalies. This real-time monitoring and analysis enable manufacturers to take immediate action and prevent issues from escalating.
Furthermore, CANBus systems can be integrated with vehicle telematics and remote vehicle diagnostics solutions. This integration allows manufacturers to remotely monitor and manage their vehicles and equipment, even across multiple locations. Real-time vehicle health monitoring and diagnostics via CANBus communication enable manufacturers to detect and address faults before they cause major problems, reducing downtime and maximizing efficiency.
Conclusion
Fault detection is a critical aspect of modern manufacturing processes. By implementing effective fault detection systems, manufacturers can improve efficiency, reduce costs, enhance product quality, and ensure safety. Technologies such as CANBus communication and remote vehicle diagnostics play a crucial role in enabling real-time monitoring and analysis, allowing manufacturers to detect and address faults before they become major issues. Investing in fault detection systems is a wise decision for manufacturers looking to stay competitive in today's fast-paced and demanding market.