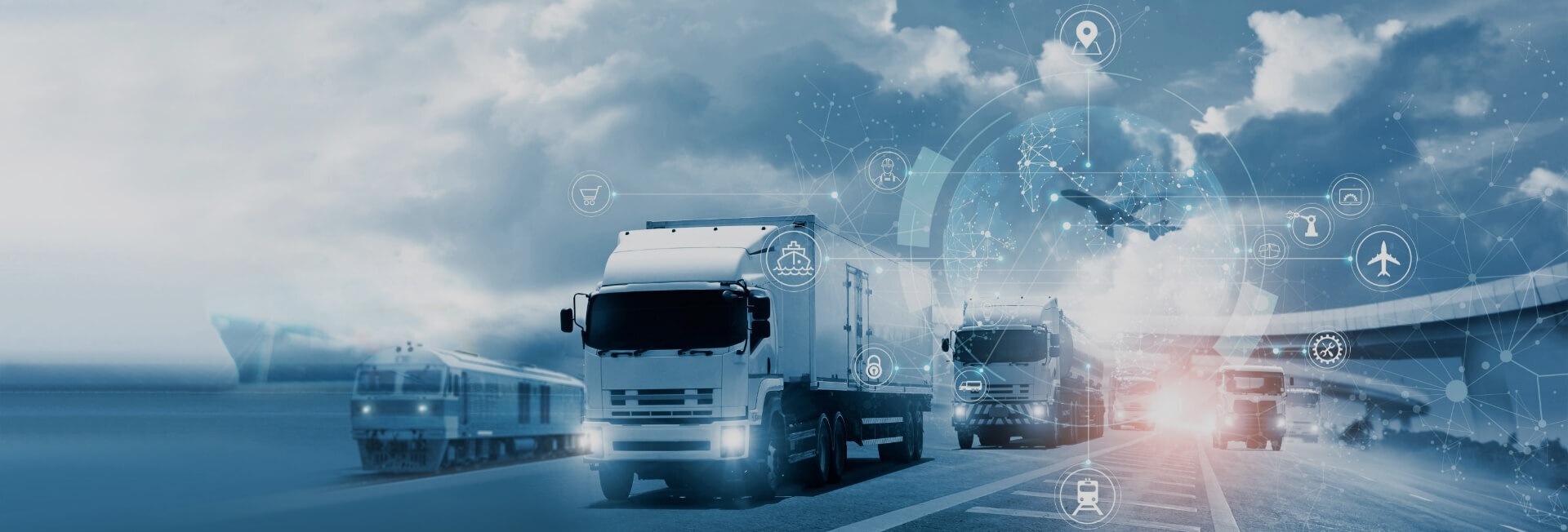
The impact of fault detection on reducing equipment failure in oil and gas industry
- Home
- Resources
- CANBus Integration and Application
- The impact of fault detection on reducing equipment failure in oil and gas industry
The oil and gas industry is one of the most critical sectors in the global economy. It plays a vital role in meeting the energy demands of various sectors, including transportation, manufacturing, and power generation. However, this industry is also prone to equipment failure, which can have severe consequences, including safety hazards, production delays, and financial losses. To mitigate these risks, fault detection has emerged as a crucial tool for identifying and addressing potential issues before they escalate into failures.
The Importance of Fault Detection
Fault detection is the process of monitoring and analyzing the performance of equipment to identify any deviations from normal operating conditions. By detecting faults early on, companies in the oil and gas industry can take proactive measures to prevent equipment failures and minimize their impact. Here are some key reasons why fault detection is essential:
1. Preventing Safety Hazards
Equipment failures in the oil and gas industry can pose significant safety hazards. For example, a faulty valve in a pipeline can lead to leaks, spills, and even explosions. By implementing fault detection systems, companies can identify and rectify such issues before they cause accidents or harm personnel. This proactive approach to safety can save lives and prevent environmental disasters.
2. Minimizing Production Downtime
When critical equipment fails, it can result in costly production downtime. For example, a malfunctioning pump or compressor can disrupt the flow of oil or gas, leading to a halt in production. Fault detection systems can help identify early signs of equipment degradation or failures, allowing companies to schedule maintenance or repairs during planned downtime. By addressing issues before they cause major breakdowns, companies can minimize production losses and maintain operational efficiency.
3. Optimizing Maintenance Strategies
Traditional maintenance strategies in the oil and gas industry are often based on fixed schedules or reactive approaches. This can result in unnecessary maintenance activities or missed opportunities to address emerging issues. Fault detection systems enable companies to adopt a predictive maintenance approach by continuously monitoring equipment health and providing real-time insights. By analyzing data from sensors and other monitoring devices, companies can optimize their maintenance activities, reducing costs and maximizing equipment uptime.
4. Improving Cost Efficiency
Equipment failures can have significant financial implications for companies in the oil and gas industry. The costs associated with repairs, replacements, and production losses can add up quickly. Fault detection systems help companies identify and rectify issues at an early stage, minimizing the extent of damage and the associated costs. By avoiding major breakdowns and optimizing maintenance activities, companies can improve cost efficiency and enhance their profitability.
The Role of CANBus Communication in Fault Detection
CANBus communication is a key technology used in fault detection systems for the oil and gas industry. CANBus, short for Controller Area Network, is a communication protocol that allows various devices within a system to exchange data in real-time. In the context of fault detection, CANBus enables the seamless integration of different sensors, actuators, and control systems, creating a comprehensive network for monitoring and analyzing equipment performance.
CANBus communication offers several advantages for fault detection in the oil and gas industry:
1. Real-Time Data Monitoring
One of the primary benefits of CANBus communication is its ability to provide real-time data monitoring. By connecting sensors and other monitoring devices to the CANBus network, companies can continuously collect data on equipment parameters such as temperature, pressure, vibration, and fluid levels. This real-time data allows for immediate detection of any abnormalities or deviations from normal operating conditions, enabling timely intervention to prevent failures.
2. Enhanced Diagnostic Capabilities
CANBus communication facilitates enhanced diagnostic capabilities for fault detection. By integrating various sensors and actuators into the CANBus network, companies can access a wealth of data on equipment health and performance. This data can be analyzed using advanced algorithms and machine learning techniques to identify patterns and anomalies indicative of potential faults. The ability to diagnose issues accurately and quickly improves the effectiveness of fault detection systems.
3. Remote Monitoring and Maintenance
CANBus communication enables remote monitoring and maintenance of equipment in the oil and gas industry. By connecting equipment to the CANBus network, companies can remotely access and monitor its performance from a central control room. This remote monitoring capability allows for real-time visibility into equipment health, enabling proactive maintenance and troubleshooting. Companies can also remotely update equipment firmware and software, further enhancing their fault detection capabilities.
4. Seamless Integration with Existing Systems
CANBus communication can seamlessly integrate with existing systems in the oil and gas industry, making it a cost-effective solution for fault detection. Many equipment manufacturers and suppliers already incorporate CANBus interfaces into their products, allowing for easy integration with the overall fault detection system. This compatibility ensures that companies can leverage their existing infrastructure and investments, minimizing the need for expensive retrofits or replacements.
The Future of Fault Detection in the Oil and Gas Industry
The oil and gas industry is continuously evolving, driven by technological advancements and the need for greater efficiency and sustainability. Fault detection systems are also evolving to meet the industry's changing needs. Here are some trends that are shaping the future of fault detection in the oil and gas industry:
1. Integration with Advanced Analytics
As the volume and complexity of data generated by equipment increase, fault detection systems are incorporating advanced analytics capabilities. Machine learning algorithms and artificial intelligence techniques can analyze large datasets to identify patterns and correlations that may indicate potential faults. By integrating advanced analytics, fault detection systems can enhance their accuracy and provide more actionable insights for maintenance and decision-making.
2. Internet of Things (IoT) Integration
The Internet of Things (IoT) is revolutionizing the oil and gas industry by connecting various devices and systems to enable seamless data exchange and automation. Fault detection systems are leveraging IoT capabilities to enhance their monitoring and analysis capabilities. By connecting equipment to IoT platforms, companies can gather data from multiple sources, including sensors, wearables, and drones, to gain a comprehensive view of equipment health and performance.
3. Predictive Maintenance and Prescriptive Analytics
Traditional maintenance strategies are shifting towards predictive maintenance, where equipment health is continuously monitored to identify potential failures before they occur. Fault detection systems are playing a crucial role in enabling predictive maintenance by providing real-time data on equipment performance. The integration of prescriptive analytics further enhances the effectiveness of fault detection systems, enabling companies to proactively address emerging issues and optimize maintenance activities.
4. Enhanced Cybersecurity
As fault detection systems become more interconnected and reliant on digital technologies, cybersecurity becomes a critical consideration. The oil and gas industry is a prime target for cyber threats due to its critical infrastructure and economic importance. Fault detection systems need robust cybersecurity measures to protect against unauthorized access, data breaches, and malicious attacks. The integration of secure communication protocols and encryption technologies is essential to ensure the integrity and confidentiality of data.
Conclusion
Fault detection plays a crucial role in reducing equipment failure in the oil and gas industry. By implementing robust fault detection systems, companies can prevent safety hazards, minimize production downtime, optimize maintenance strategies, and improve cost efficiency. CANBus communication provides a powerful tool for fault detection, enabling real-time data monitoring, enhanced diagnostic capabilities, remote monitoring and maintenance, and seamless integration with existing systems. The future of fault detection in the oil and gas industry lies in advanced analytics, IoT integration, predictive maintenance, and enhanced cybersecurity. By embracing these trends, companies can enhance their operational efficiency, reduce risks, and ensure the reliability and sustainability of their equipment.