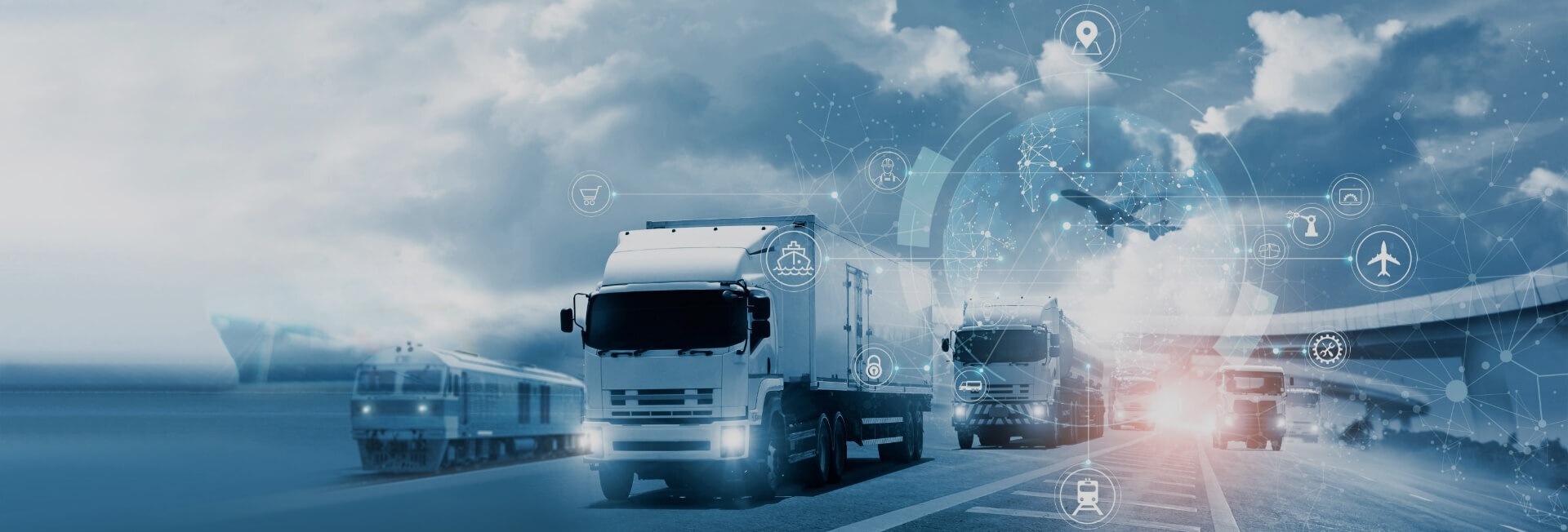
The impact of fault detection on reducing downtime in manufacturing
- Home
- Resources
- CANBus Integration and Application
- The impact of fault detection on reducing downtime in manufacturing
The Importance of Fault Detection in Reducing Downtime in Manufacturing
In the fast-paced manufacturing industry, minimizing downtime is crucial for maintaining productivity and maximizing profits. One of the key factors that can significantly impact downtime is the ability to detect faults in a timely manner. Fault detection plays a vital role in identifying and addressing issues before they escalate into major problems, leading to costly repairs and extended periods of downtime.
What is Fault Detection?
Fault detection is the process of identifying deviations or abnormalities in the performance of a system or equipment. In the context of manufacturing, it involves monitoring various parameters and signals to detect any signs of potential failures or malfunctions in machinery or processes. By identifying faults early on, manufacturers can take proactive measures to prevent downtime and maintain smooth operations.
The Impact of Fault Detection on Downtime Reduction
Implementing an effective fault detection system can have a significant impact on reducing downtime in manufacturing. Here are some key ways in which fault detection contributes to downtime reduction:
1. Early Warning System
A fault detection system serves as an early warning system, alerting operators and maintenance personnel about potential issues before they cause major disruptions. By continuously monitoring critical parameters, such as temperature, pressure, vibration, and energy consumption, the system can detect anomalies and trigger alarms or notifications. This allows immediate action to be taken to address the fault and prevent further damage or breakdowns.
2. Predictive Maintenance
Fault detection enables the implementation of predictive maintenance strategies. By analyzing data collected from sensors and other monitoring devices, manufacturers can identify patterns and trends that indicate the likelihood of future failures. This allows maintenance activities to be scheduled proactively, during planned downtime or scheduled maintenance windows, rather than during unexpected breakdowns. Predictive maintenance helps minimize unplanned downtime and reduces the risk of costly emergency repairs.
3. Improved Equipment Reliability
Fault detection systems contribute to improved equipment reliability by identifying and addressing potential issues early on. Timely detection of faults allows manufacturers to take corrective actions, such as calibration, lubrication, or component replacement, to ensure the equipment operates within optimal parameters. This proactive approach helps prevent sudden breakdowns and extends the lifespan of equipment, reducing the frequency and duration of downtime.
4. Streamlined Repair Processes
When faults are detected early, repair processes can be streamlined and expedited. By knowing the exact nature and location of the fault, maintenance personnel can quickly diagnose the problem and prepare the necessary tools, parts, and resources. This reduces the time required for troubleshooting and repair, minimizing the overall duration of downtime. In some cases, remote diagnostics and troubleshooting capabilities enabled by vehicle telematics and CANBus communication can further expedite the repair process by allowing technicians to remotely access and analyze the equipment.
The Role of CANBus Communication in Fault Detection
CANBus communication plays a critical role in fault detection and remote diagnostics in manufacturing. The Controller Area Network (CANBus) is a communication protocol used in automotive and industrial applications to enable real-time data exchange between electronic control units (ECUs). By integrating CANBus interfaces and devices into manufacturing equipment, manufacturers can collect real-time data on various parameters and monitor the performance of critical components.
CANBus communication allows for seamless integration with vehicle telematics systems, enabling remote monitoring and diagnostics of equipment. This means that manufacturers can access real-time data and receive instant alerts about any potential faults or abnormalities, even if they are not physically present at the manufacturing facility. Remote diagnostics via CANBus communication significantly reduce response times and enable proactive maintenance actions, ultimately leading to reduced downtime.
Conclusion
Fault detection plays a crucial role in reducing downtime in the manufacturing industry. By implementing effective fault detection systems and leveraging technologies like CANBus communication, manufacturers can detect faults early, implement predictive maintenance strategies, improve equipment reliability, and streamline repair processes. These proactive measures help minimize unplanned downtime, reduce repair costs, and ensure smooth operations, ultimately contributing to increased productivity and profitability.