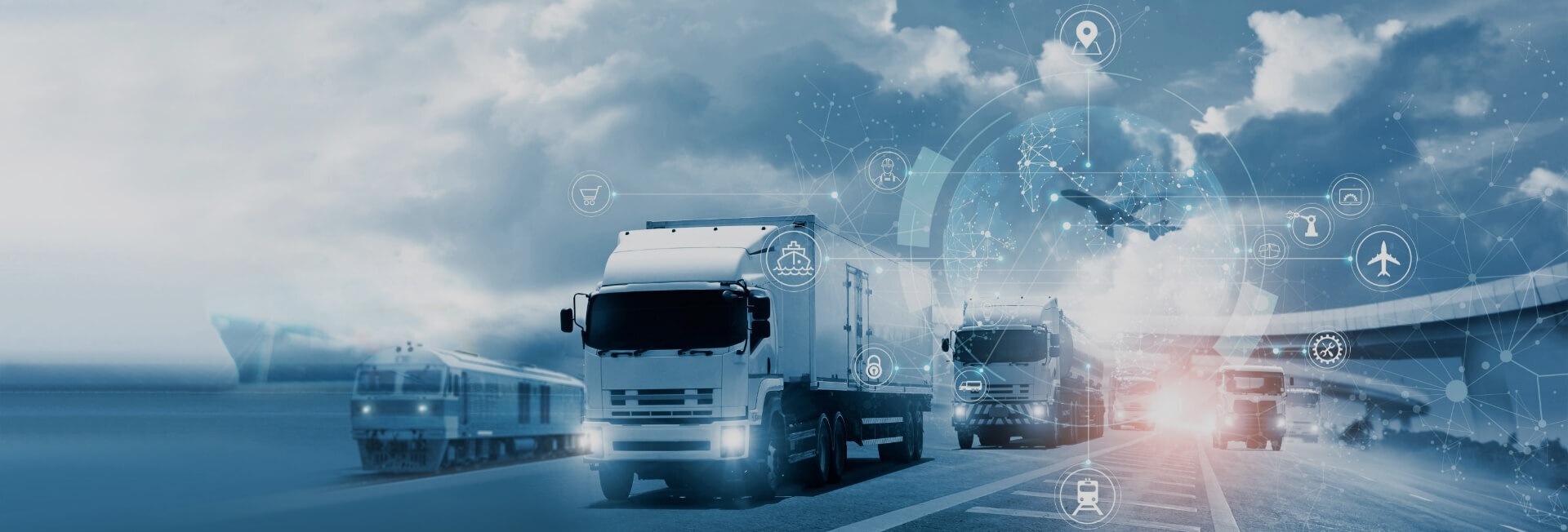
The impact of fault detection on reducing downtime in chemical plants
- Home
- Resources
- CANBus Integration and Application
- The impact of fault detection on reducing downtime in chemical plants
The Importance of Fault Detection in Reducing Downtime in Chemical Plants
Chemical plants play a crucial role in manufacturing various products that are essential to our daily lives. However, these plants are susceptible to equipment failures and malfunctions that can lead to costly downtime. Fault detection systems have emerged as a critical tool in minimizing downtime and ensuring the smooth operation of chemical plants. In this article, we will explore the impact of fault detection on reducing downtime and improving overall plant efficiency.
The Role of Fault Detection in Chemical Plants
Fault detection systems are designed to monitor the performance and condition of equipment in real-time. By continuously monitoring critical parameters such as temperature, pressure, flow rates, and vibration levels, these systems can detect anomalies and potential failures before they cause significant disruptions. Early detection of faults allows plant operators to take proactive measures to prevent equipment breakdowns and minimize downtime.
Benefits of Fault Detection in Chemical Plants
Implementing a robust fault detection system in a chemical plant offers several benefits:
1. Minimizing Downtime
Fault detection systems enable early identification of equipment failures, allowing maintenance teams to address issues before they escalate. By proactively addressing faults, chemical plants can significantly reduce unplanned downtime and avoid costly production delays. This not only improves overall plant efficiency but also enhances customer satisfaction by ensuring timely delivery of products.
2. Preventing Equipment Damage
Equipment failures in chemical plants can sometimes lead to severe damage, posing safety risks to plant personnel and the surrounding environment. Fault detection systems help prevent such incidents by detecting anomalies and triggering alarms or shutdown procedures. By promptly addressing faults, plant operators can prevent equipment damage and mitigate potential hazards.
3. Optimizing Maintenance Activities
Fault detection systems provide valuable insights into the health and performance of equipment, enabling maintenance teams to prioritize their activities. By focusing on the most critical issues identified by the fault detection system, plants can optimize their maintenance schedules and allocate resources more efficiently. This results in cost savings and reduces the overall maintenance workload.
4. Enhancing Overall Plant Efficiency
Efficient operation of chemical plants is paramount to achieving maximum productivity. Fault detection systems play a vital role in maintaining optimal performance by identifying inefficiencies, such as equipment malfunctions or process deviations. By addressing these issues promptly, plants can optimize their operations, reduce energy consumption, and improve overall plant efficiency.
Implementing a Fault Detection System
Integrating a fault detection system into a chemical plant requires careful planning and consideration. Here are some key factors to keep in mind:
1. Sensor Selection
The choice of sensors is crucial in ensuring accurate fault detection. Different equipment and processes require specific sensors that can measure and monitor the relevant parameters. It is essential to select sensors that are compatible with the chemical plant's operating conditions and can provide reliable data for fault detection.
2. Data Acquisition and Analysis
A robust fault detection system relies on accurate and timely data acquisition. Implementing a data acquisition system that can collect data from various sensors and equipment is critical. The collected data should then be analyzed using advanced algorithms and techniques to detect anomalies and patterns indicative of potential faults.
3. Alarm and Notification Systems
Once a fault is detected, it is crucial to notify the relevant personnel promptly. Implementing an alarm and notification system that can alert maintenance teams or plant operators about potential failures is essential. This allows for timely intervention and preventive measures to be taken, minimizing the impact of faults on plant operations.
4. Integration with Maintenance Management Systems
Integrating the fault detection system with the plant's maintenance management system allows for seamless communication and workflow. When a fault is detected, the system can automatically generate work orders or notifications, ensuring that the necessary maintenance activities are carried out in a timely manner. This integration streamlines the maintenance process and facilitates efficient fault resolution.
Conclusion
Fault detection systems have revolutionized the way chemical plants monitor and maintain their equipment. By detecting faults in real-time, these systems enable proactive maintenance, minimizing downtime, preventing equipment damage, optimizing maintenance activities, and enhancing overall plant efficiency. Implementing a robust fault detection system requires careful planning and integration with existing plant systems. However, the investment in fault detection technology can yield significant returns by reducing downtime, improving safety, and maximizing productivity in chemical plants.