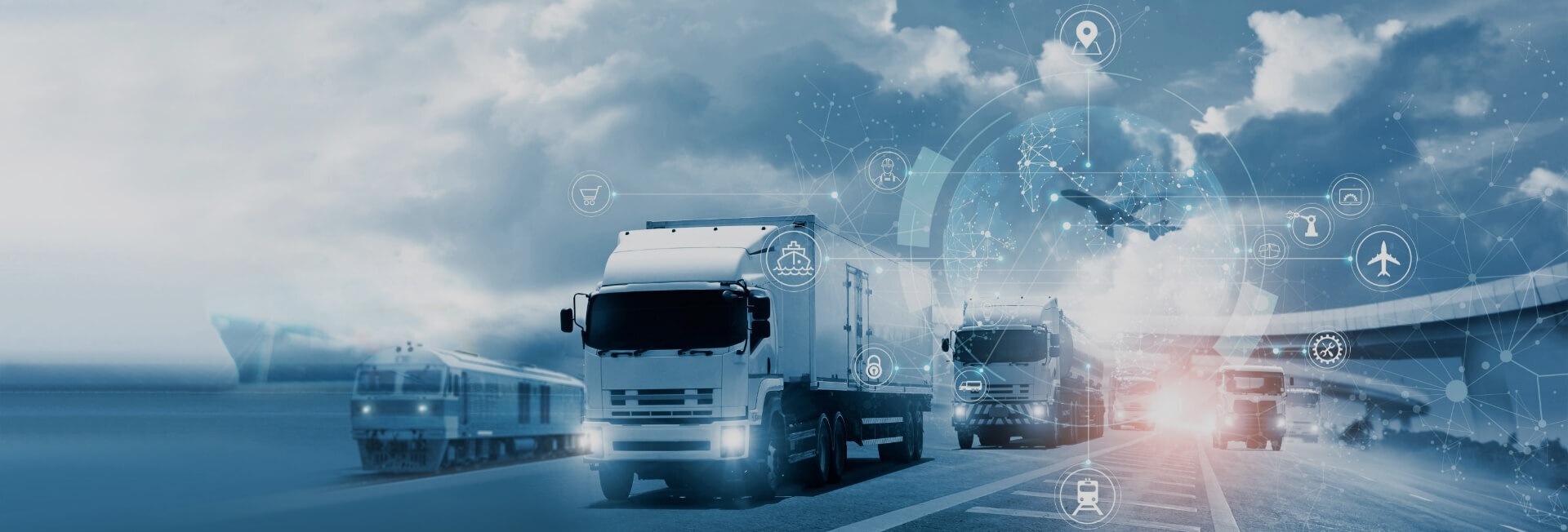
The impact of CANBus system integration on reducing maintenance costs in industrial machinery
- Home
- Resources
- CANBus Integration and Application
- The impact of CANBus system integration on reducing maintenance costs in industrial machinery
The Impact of CANBus System Integration on Reducing Maintenance Costs in Industrial Machinery
In today's industrial landscape, machinery plays a critical role in ensuring efficient operations and productivity. However, maintaining and servicing industrial machinery can be a significant cost factor for businesses. Traditional maintenance practices often involve routine inspections and manual diagnostics, leading to downtime and increased expenses.
The Need for Advanced Diagnostics in Industrial Machinery
Effective maintenance strategies require timely identification and resolution of issues to prevent breakdowns and minimize downtime. This is where CANBus system integration comes into play. CANBus communication technology allows for real-time monitoring and diagnostics of industrial machinery, enabling remote fault detection and vehicle health monitoring.
The Basics of CANBus Systems
CANBus, or Controller Area Network Bus, is a communication protocol widely used in automotive and industrial applications. It provides a reliable and efficient means of transmitting data between various components within a machine or vehicle. CANBus systems consist of interconnected devices, such as sensors and actuators, that communicate using CANBus protocols.
By integrating CANBus systems into industrial machinery, manufacturers can gather valuable data on the machine's performance, including operating parameters, fault codes, and diagnostic information. This data can be transmitted to a central control system or accessed remotely for analysis and troubleshooting.
The Benefits of CANBus System Integration
1. Remote Vehicle Diagnostics: One of the primary advantages of CANBus system integration is the ability to perform remote vehicle diagnostics. Instead of manually inspecting machinery on-site, technicians can access real-time data from the CANBus network, allowing them to identify potential issues and diagnose faults remotely. This not only saves time but also reduces the need for physical presence and minimizes downtime.
2. Fault Detection: CANBus systems enable proactive fault detection by continuously monitoring the performance of industrial machinery. Any deviations from normal operating parameters can trigger fault codes and alerts, notifying operators or technicians of potential issues. Early detection of faults allows for timely repairs or maintenance, preventing costly breakdowns and reducing overall maintenance costs.
3. Predictive Maintenance: By leveraging the data collected through CANBus system integration, businesses can implement predictive maintenance strategies. Analyzing historical data and trends enables the identification of potential failures before they occur, allowing for scheduled maintenance and part replacements. This approach minimizes unplanned downtime and optimizes maintenance schedules, resulting in cost savings and increased operational efficiency.
4. Improved Data Management: CANBus systems facilitate seamless integration of automotive data into existing fleet management and maintenance systems. By consolidating data from multiple machines or vehicles, businesses can gain insights into overall fleet performance, identify common issues, and optimize maintenance schedules. This centralized data management approach streamlines operations and reduces administrative overhead.
Implementing CANBus System Integration
Integrating CANBus systems into industrial machinery requires careful planning and collaboration between equipment manufacturers and technology providers. Here are some key considerations for successful implementation:
1. Hardware Compatibility: Ensure that the machinery is equipped with CANBus-compatible devices and sensors. This includes selecting the appropriate CANBus interface modules and protocols that are compatible with the target machinery.
2. Data Analysis and Visualization: Implement a data analysis and visualization platform that can handle the influx of data from the CANBus network. This may involve utilizing cloud-based solutions or on-premises systems, depending on the organization's requirements and infrastructure.
3. Training and Support: Provide adequate training and support to operators and technicians to effectively utilize the CANBus system integration. This includes educating them on interpreting fault codes, analyzing data, and troubleshooting machinery based on the information provided by the CANBus network.
4. Scalability: Consider the scalability of the CANBus system integration to accommodate future expansion or modifications to the machinery. This includes ensuring that the network can handle increasing data volumes and additional devices without compromising performance or reliability.
Conclusion
CANBus system integration offers numerous benefits for reducing maintenance costs in industrial machinery. By enabling remote vehicle diagnostics, fault detection, and predictive maintenance, businesses can minimize downtime, optimize maintenance schedules, and improve overall operational efficiency. Implementing CANBus system integration requires careful planning and collaboration, but the long-term cost savings and increased productivity make it a worthwhile investment for industrial businesses.