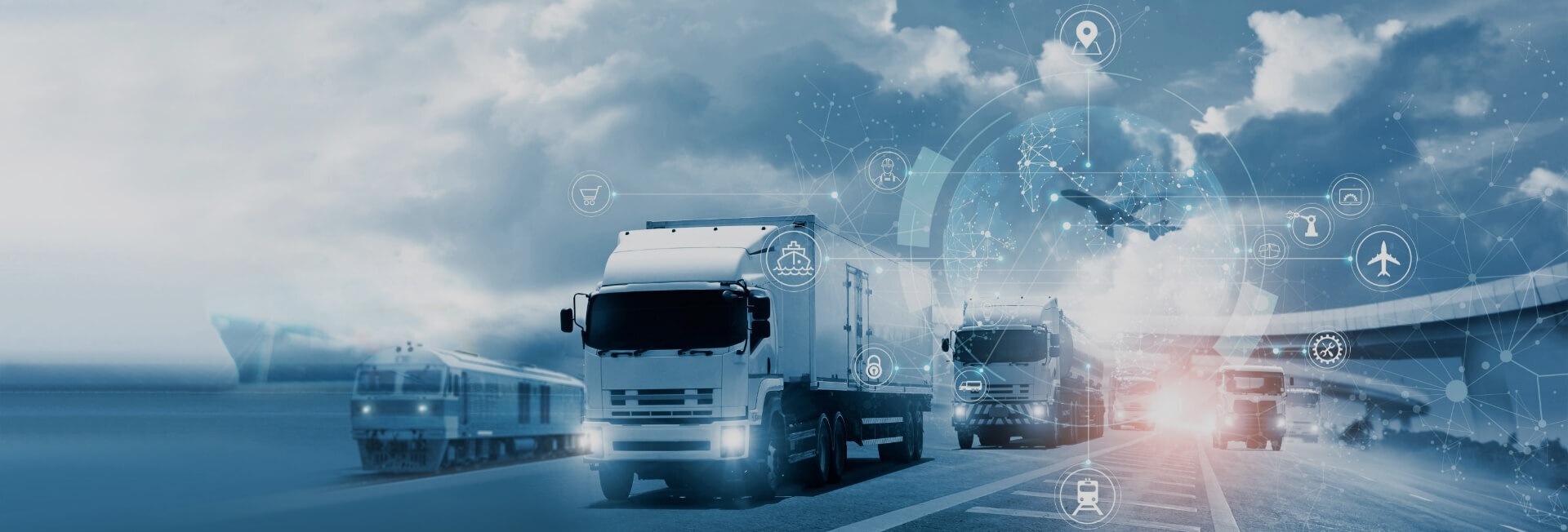
The challenges of integrating CANBus systems in legacy industrial equipment
- Home
- Resources
- CANBus Integration and Application
- The challenges of integrating CANBus systems in legacy industrial equipment
The Complexity of Integrating CANBus Systems in Legacy Industrial Equipment
Legacy industrial equipment plays a crucial role in various industries, from manufacturing to agriculture. These machines have been in operation for years, providing reliable service and contributing to the overall efficiency of the operations. However, with the advancements in technology, there is a growing need to integrate these legacy systems with modern technologies such as CANBus systems for improved monitoring and diagnostics. While this integration offers numerous benefits, it also poses significant challenges that need to be addressed.
The Importance of CANBus Systems in Industrial Equipment
CANBus systems, short for Controller Area Network, are widely used in modern vehicles and industrial equipment for efficient communication between various electronic devices. These systems enable real-time exchange of information, allowing for improved diagnostics, remote monitoring, and fault detection. By integrating CANBus systems into legacy industrial equipment, businesses can gain valuable insights into the health and performance of their machines, leading to increased productivity and reduced downtime.
The Challenges of Integrating CANBus Systems in Legacy Industrial Equipment
Integrating CANBus systems in legacy industrial equipment presents several challenges that need to be overcome for successful implementation. These challenges include:
1. Compatibility Issues
Legacy industrial equipment often uses proprietary protocols and communication standards that are not compatible with CANBus systems. This incompatibility makes it difficult to establish a seamless connection between the existing equipment and the CANBus network. Adapting the legacy equipment to support CANBus communication requires specialized hardware and software modifications, which can be time-consuming and costly.
2. Limited Data Availability
Legacy industrial equipment may not have built-in sensors or data acquisition systems, making it challenging to retrieve real-time data from these machines. CANBus systems rely on the availability of data from various sensors and devices to provide accurate diagnostics and monitoring. Without the necessary sensors and data acquisition systems, the integration of CANBus systems becomes limited, and the full potential of real-time monitoring and diagnostics cannot be realized.
3. Hardware and Software Upgrades
Integrating CANBus systems in legacy industrial equipment often requires significant hardware and software upgrades to ensure compatibility and seamless communication. This can involve replacing outdated control modules, adding new sensors and actuators, and updating the software to support CANBus protocols. These upgrades can be costly and time-consuming, especially in cases where the legacy equipment is widespread and requires extensive modifications.
4. Training and Support
Implementing CANBus systems in legacy industrial equipment requires specialized knowledge and expertise. The existing workforce may not be familiar with the intricacies of CANBus communication and the associated diagnostic tools. Training the workforce to understand and utilize CANBus systems effectively can be a significant challenge. Additionally, the availability of technical support for troubleshooting and maintenance of the integrated systems is crucial to ensure smooth operations. Lack of proper training and support can hinder the successful integration and utilization of CANBus systems in legacy industrial equipment.
Overcoming the Challenges
While integrating CANBus systems in legacy industrial equipment presents challenges, they can be overcome with proper planning and execution. Here are some strategies to address these challenges:
1. Conduct a Compatibility Analysis
Prior to integrating CANBus systems, it is essential to perform a thorough analysis of the legacy equipment to identify any compatibility issues. This analysis should include an evaluation of the existing communication protocols and hardware interfaces. Based on the analysis, appropriate hardware and software modifications can be planned to ensure compatibility with CANBus systems.
2. Retrofit Sensors and Data Acquisition Systems
If the legacy equipment lacks sensors and data acquisition systems, retrofitting them can enable the collection of real-time data for integration with the CANBus network. This may involve installing new sensors, upgrading existing sensors, and implementing data acquisition systems. By retrofitting the equipment with the necessary sensors, the full potential of CANBus systems can be realized, enabling effective monitoring and diagnostics.
3. Collaborate with CANBus System Providers
Collaborating with CANBus system providers and experts can greatly facilitate the integration process. These experts can provide valuable insights and guidance on the hardware and software upgrades required, as well as offer training and support for the workforce. Working closely with the providers can ensure a smooth and successful integration of CANBus systems in legacy industrial equipment.
4. Gradual Implementation
Instead of attempting to integrate CANBus systems in all legacy equipment simultaneously, a gradual implementation approach can be adopted. This allows for testing and troubleshooting in a controlled environment before full-scale integration. By gradually integrating CANBus systems, any issues or challenges that arise can be addressed effectively, minimizing disruptions to the overall operations.
The Benefits of Integrating CANBus Systems in Legacy Industrial Equipment
Despite the challenges, integrating CANBus systems in legacy industrial equipment offers significant benefits, making it a worthwhile endeavor for businesses. Some of the key benefits include:
1. Improved Diagnostics and Fault Detection
By integrating CANBus systems, businesses can access real-time data on the performance and health of their legacy industrial equipment. This enables proactive fault detection and timely maintenance, reducing downtime and increasing overall productivity. The ability to monitor various parameters and receive instant alerts for any anomalies allows for efficient troubleshooting and minimizes the risk of unexpected failures.
2. Remote Monitoring and Maintenance
CANBus systems enable remote monitoring and maintenance of industrial equipment. Through the integration of telematics and remote connectivity, businesses can access equipment data from anywhere. This remote access streamlines maintenance activities, eliminates the need for physical inspections, and reduces the costs associated with on-site visits. Real-time data from the CANBus network allows for remote diagnostics, enabling timely interventions to prevent critical issues.
3. Enhanced Efficiency and Productivity
Integrating CANBus systems in legacy industrial equipment provides valuable insights into equipment performance, energy consumption, and overall efficiency. By analyzing the data collected from the CANBus network, businesses can identify areas for improvement, optimize processes, and enhance productivity. The ability to monitor equipment parameters in real-time enables proactive decision-making and timely adjustments to maximize efficiency.
4. Future-Proofing
Integrating CANBus systems in legacy industrial equipment future-proofs the operations by enabling compatibility with modern technologies and systems. As the industrial landscape continues to evolve, businesses that have already integrated CANBus systems will be better prepared to adapt to new advancements and requirements. This future-proofing ensures that the legacy equipment remains relevant and can be seamlessly integrated with emerging technologies.
Conclusion
The integration of CANBus systems in legacy industrial equipment presents both challenges and opportunities. By overcoming the compatibility issues, retrofitting sensors, collaborating with experts, and adopting a gradual implementation approach, businesses can successfully integrate CANBus systems and reap the benefits of improved diagnostics, remote monitoring, and enhanced efficiency. While the process may require initial investment and effort, the long-term advantages make it a worthwhile endeavor for businesses looking to optimize their operations and future-proof their legacy equipment.