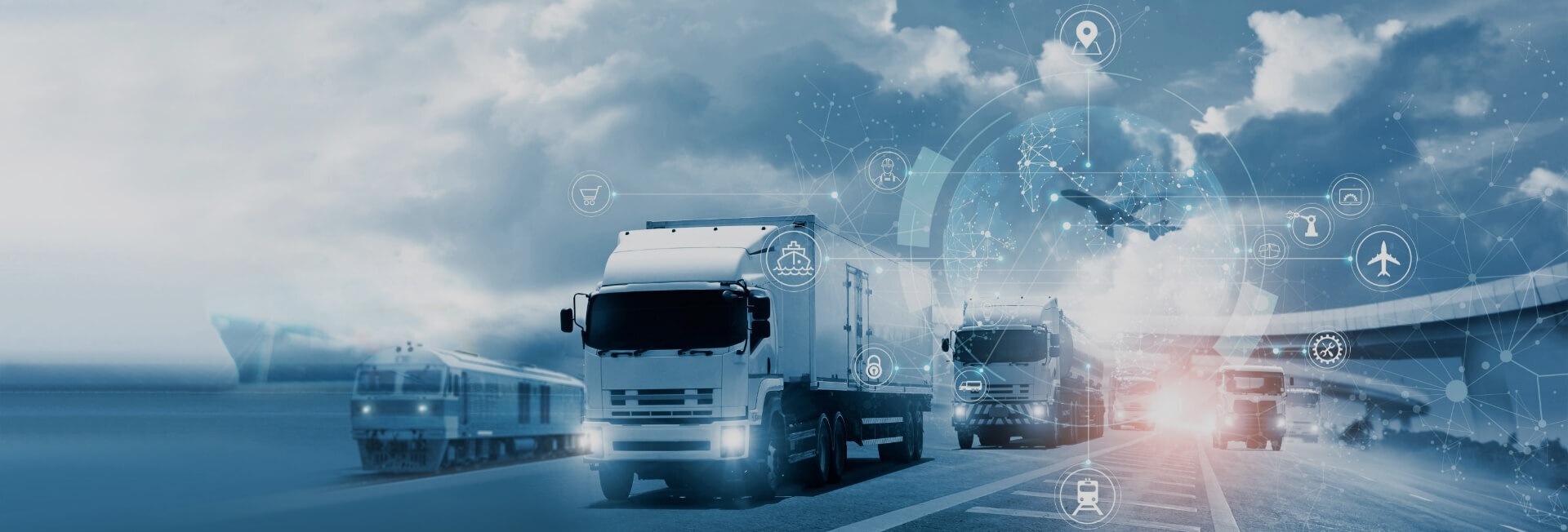
The challenges of implementing CANbus networks in harsh and rugged environments
- Home
- Resources
- CANBus Integration and Application
- The challenges of implementing CANbus networks in harsh and rugged environments
Overcoming Challenges in Implementing CANbus Networks in Harsh Environments
Implementing CANbus networks in harsh and rugged environments can present a unique set of challenges. These networks, which are commonly used in vehicles for communication between various electronic control units (ECUs), face issues such as extreme temperatures, vibrations, electromagnetic interference (EMI), and physical damage. In this article, we will explore the challenges faced in implementing CANbus networks in harsh environments and discuss potential solutions to overcome them.
1. Temperature Extremes
One of the primary challenges in harsh environments is dealing with extreme temperatures. CANbus networks can be exposed to both extremely high and low temperatures, depending on the application. For example, in automotive and industrial settings, vehicles and machinery can operate in environments where temperatures can reach well below freezing or exceed 100 degrees Celsius.
Extreme temperatures can affect the performance and reliability of CANbus networks. In cold temperatures, the conductivity of wires and connectors can decrease, leading to increased resistance and signal loss. This can result in communication errors and data corruption. On the other hand, high temperatures can cause the insulation of wires to degrade, leading to short circuits or even complete failure of the network.
To overcome temperature-related challenges, it is important to use components and materials that can withstand the extremes. This includes using high-quality wires and connectors with appropriate insulation and shielding. Additionally, implementing temperature-resistant ECUs and incorporating proper thermal management techniques can help maintain the performance and reliability of CANbus networks in harsh environments.
2. Vibrations
Another challenge in harsh environments is dealing with vibrations. Vehicles and machinery operating in rugged environments are often subjected to continuous vibrations, which can affect the integrity of CANbus networks. Vibrations can cause connectors to become loose, leading to intermittent or complete loss of communication. Moreover, constant vibrations can also lead to fatigue failure of wires and connectors, further compromising the network's reliability.
To mitigate the impact of vibrations, it is essential to use robust and vibration-resistant components. This includes using connectors with locking mechanisms to ensure a secure and stable connection. Additionally, cables should be properly secured and routed to minimize movement and stress. Implementing shock-absorbing mounts for ECUs and using vibration-resistant materials can also help improve the overall durability and reliability of CANbus networks in harsh environments.
3. Electromagnetic Interference (EMI)
Harsh environments are often characterized by the presence of electromagnetic interference (EMI) sources such as motors, power lines, and other electronic devices. EMI can interfere with the signals transmitted over CANbus networks, leading to communication errors and data corruption. This can result in inaccurate readings, faulty diagnostics, and compromised vehicle performance.
To address EMI challenges, it is important to implement proper shielding and grounding techniques. Shielded cables can help minimize the impact of external electromagnetic fields on the CANbus signals. Grounding the network and ensuring proper electrical grounding of the vehicle or machinery can also help reduce the effects of EMI. Additionally, isolating sensitive components and using filters and ferrite cores can further improve the EMI immunity of CANbus networks in harsh environments.
4. Physical Damage
In harsh environments, CANbus networks are often exposed to physical damage caused by factors such as debris, water, and mechanical impact. Physical damage can lead to broken wires, damaged connectors, and even complete network failure. This can result in costly repairs, downtime, and compromised vehicle or machinery performance.
To protect CANbus networks from physical damage, it is important to use ruggedized components that are designed to withstand harsh conditions. This includes using connectors with IP-rated sealing to prevent water and dust ingress. Additionally, routing cables away from potential hazards and using protective conduits can help minimize the risk of physical damage. Regular inspections and maintenance can also help identify and address any potential issues before they escalate into major problems.
Conclusion
Implementing CANbus networks in harsh and rugged environments presents a unique set of challenges. Temperature extremes, vibrations, electromagnetic interference, and physical damage can all impact the performance and reliability of these networks. However, by using high-quality components, implementing proper thermal management and shielding techniques, and taking necessary precautions to prevent physical damage, it is possible to overcome these challenges and ensure the successful implementation of CANbus networks in harsh environments.