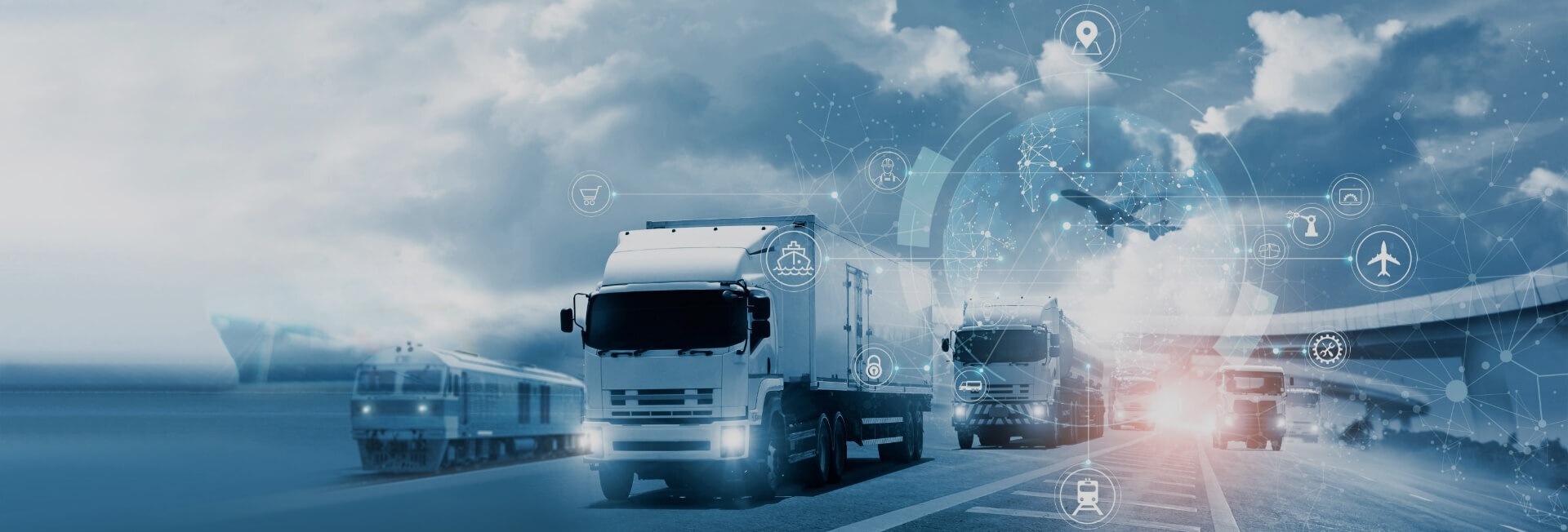
The challenges of implementing CANBus interface in marine vessels
- Home
- Resources
- CANBus Integration and Application
- The challenges of implementing CANBus interface in marine vessels
The Challenges of Implementing CANBus Interface in Marine Vessels
CANBus communication has become an essential component in the automotive industry, enabling vehicle diagnostics, telematics, and fault detection. However, implementing CANBus interface in marine vessels presents unique challenges that need to be addressed for successful integration. In this article, we will explore these challenges and discuss potential solutions.
1. Compatibility with Marine Systems
One of the major challenges in implementing CANBus interface in marine vessels is ensuring compatibility with existing marine systems. Unlike automotive applications, marine vessels have their own unique set of systems and protocols. Integrating the CANBus network with these systems requires careful consideration and customization.
Marine systems often rely on proprietary communication protocols, which may not be compatible with the standard CANBus protocols used in the automotive industry. This can make it difficult to establish communication between different systems and access the necessary data for diagnostics and monitoring.
Solution: To overcome this challenge, it is essential to work closely with marine system manufacturers and engineers to develop custom solutions that bridge the gap between the CANBus network and the marine systems. This may involve developing specialized CANBus devices and protocols that are compatible with both automotive and marine systems.
2. Harsh Environmental Conditions
Marine vessels operate in harsh environmental conditions, including exposure to saltwater, extreme temperatures, humidity, and vibrations. These conditions can affect the performance and reliability of CANBus devices and communication.
Saltwater can corrode connectors and wiring, leading to communication failures. Extreme temperatures can cause the CANBus network to malfunction or become unstable. Humidity can also impact the performance of the network, resulting in data loss or corruption. Additionally, vibrations from the vessel's engines and machinery can disrupt the communication signals.
Solution: To address these challenges, it is crucial to use marine-grade CANBus devices and components that are specifically designed to withstand the harsh conditions of marine environments. These devices should be sealed and protected against corrosion, moisture, and temperature extremes. Additionally, proper insulation and vibration dampening measures should be implemented to ensure reliable communication.
3. Integration with Existing Control Systems
Marine vessels often have complex control systems that manage various functions, including propulsion, navigation, and safety. Integrating the CANBus interface with these existing control systems can be challenging, as it requires seamless communication and data integration.
Each marine vessel may have different control systems from different manufacturers, each with its own protocols and interfaces. This makes it difficult to establish a unified communication network that can effectively transmit and receive data from the CANBus network.
Solution: To overcome this challenge, a comprehensive vehicle data management system should be implemented. This system acts as a middleware that translates and integrates data from the CANBus network into a format that can be understood by the existing control systems. It should support multiple protocols and interfaces to ensure compatibility with various control systems.
4. Real-Time Monitoring and Diagnostics
Real-time monitoring and diagnostics are crucial for ensuring the health and performance of marine vessels. However, implementing real-time monitoring and diagnostics via CANBus interface in marine vessels can be challenging due to the large amount of data generated and the need for accurate and timely analysis.
Marine vessels generate a vast amount of data from various sensors and systems, including engine performance, fuel consumption, navigation, and safety systems. Processing and analyzing this data in real-time can be resource-intensive and require sophisticated algorithms and computational power.
Solution: To address this challenge, robust vehicle health monitoring and diagnostics systems should be implemented. These systems should be capable of collecting, processing, and analyzing data in real-time, providing actionable insights and alerts for potential issues or faults. Advanced algorithms and machine learning techniques can be utilized to improve the accuracy and efficiency of the diagnostics process.
Conclusion
Implementing CANBus interface in marine vessels presents unique challenges that need to be carefully addressed. By ensuring compatibility with marine systems, mitigating the impact of harsh environmental conditions, integrating with existing control systems, and implementing real-time monitoring and diagnostics, the benefits of CANBus communication can be fully realized in the marine industry. With the right solutions and technologies, marine vessels can benefit from remote vehicle diagnostics, fault detection, and improved overall performance.