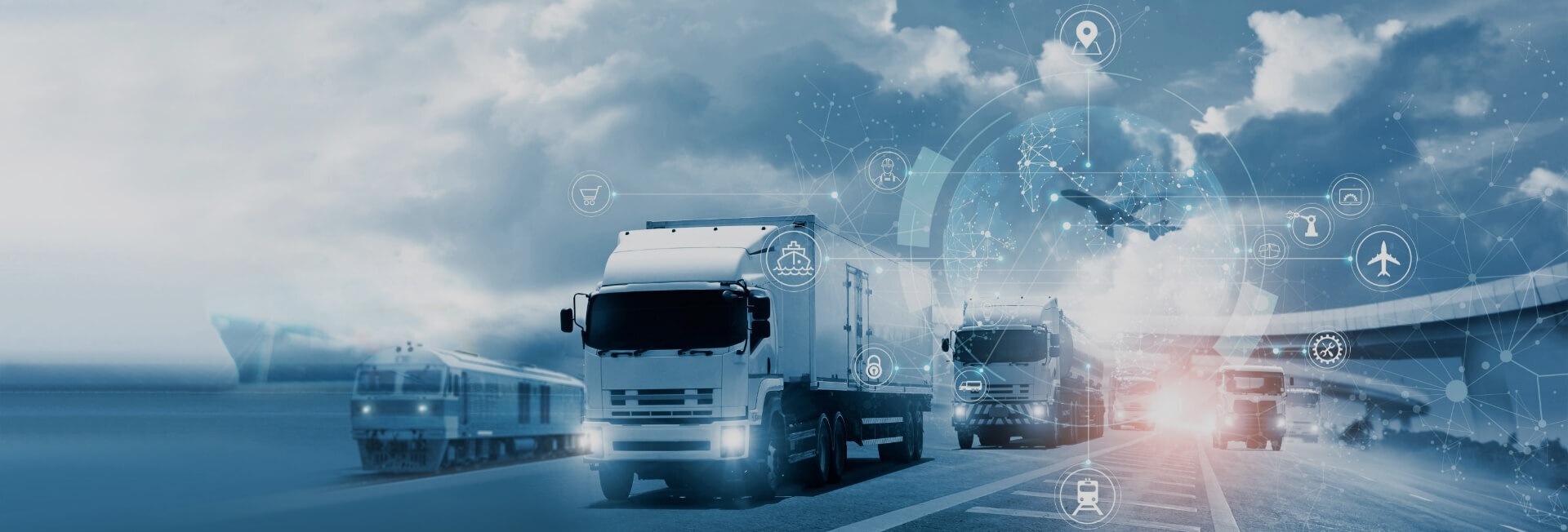
The challenges of implementing a CANbus network in large-scale industrial systems
- Home
- Resources
- CANBus Integration and Application
- The challenges of implementing a CANbus network in large-scale industrial systems
The Challenges of Implementing a CANbus Network in Large-Scale Industrial Systems
As industrial systems become more complex and interconnected, the need for efficient and reliable communication between devices and components is paramount. This is where the Controller Area Network (CANbus) comes into play. CANbus is a robust and widely-used communication protocol that allows for real-time data exchange between devices within a network. However, implementing a CANbus network in large-scale industrial systems comes with its own set of challenges. In this article, we will explore the complexities and solutions associated with integrating a CANbus network in such systems.
Understanding CANbus Communication
CANbus communication is based on a two-wire bus system, consisting of a CAN High (CANH) and a CAN Low (CANL) wire. This differential signaling scheme allows for noise immunity and reliable data transmission over long distances. In large-scale industrial systems, CANbus networks can span across multiple devices and subsystems, such as sensors, actuators, and control units.
One of the main challenges in implementing a CANbus network in large-scale industrial systems is the sheer volume of data that needs to be transmitted and processed. With the increasing complexity of modern industrial systems, the amount of data generated by various devices and components can be overwhelming. Efficient data integration and management are crucial to ensure smooth operation and effective decision-making.
Integration and Management of CANbus Data
The integration and management of CANbus data in large-scale industrial systems require robust solutions that can handle the high data volumes and ensure data integrity. Vehicle telematics and diagnostics play a crucial role in this process, providing real-time monitoring and analysis of vehicle health and performance. By utilizing CANbus interfaces and diagnostic tools, fleet managers can remotely access and analyze vehicle data, enabling proactive maintenance and fault detection.
Automotive data integration platforms are also available to streamline the integration and management of CANbus data in large-scale industrial systems. These platforms provide a centralized hub for collecting, analyzing, and visualizing vehicle data from various sources, including CANbus networks. This enables fleet managers and system operators to gain insights into vehicle health and performance, identify potential issues, and make informed decisions.
Ensuring Fault Detection and Remote Vehicle Diagnostics
Fault detection and remote vehicle diagnostics are crucial in large-scale industrial systems to minimize downtime and optimize maintenance activities. CANbus networks provide a wealth of diagnostic information, such as fault codes, sensor data, and system status. However, effectively utilizing this data for fault detection and remote diagnostics can be challenging.
One of the main challenges is the interoperability of CANbus devices and protocols. In large-scale industrial systems, different devices and components from various manufacturers may utilize different CANbus protocols, making it difficult to standardize and integrate the data. This requires the use of advanced diagnostic tools and software that can handle multiple protocols and provide a unified view of the vehicle's health.
CANBus System Integration and Standardization
To overcome the challenges associated with implementing a CANbus network in large-scale industrial systems, system integration and standardization are crucial. Standardization of CANbus protocols and devices enables seamless communication and data exchange between different subsystems, reducing complexity and improving reliability.
Additionally, system integration plays a crucial role in ensuring the smooth operation of a CANbus network. By integrating CANbus networks with other industrial communication protocols, such as Modbus or Ethernet/IP, data can be shared between different systems and devices. This enables a holistic view of the entire industrial system, allowing for better decision-making and optimization.
Conclusion
Implementing a CANbus network in large-scale industrial systems brings its own set of challenges, including data integration, fault detection, and system integration. However, with the right tools, protocols, and system integration strategies, these challenges can be overcome. By leveraging the power of CANbus communication and integrating it with other industrial protocols, large-scale industrial systems can achieve efficient and reliable data exchange, leading to improved performance, reduced downtime, and optimized maintenance activities.