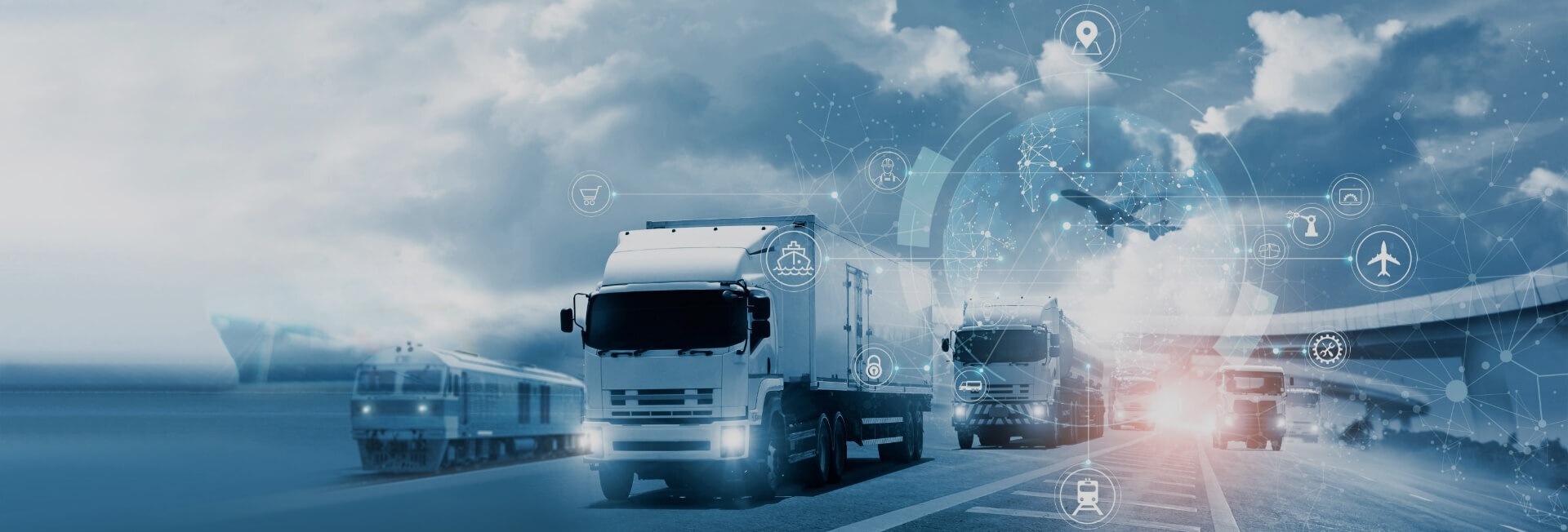
The challenges of ensuring fault tolerance and redundancy in CANbus networks
- Home
- Resources
- CANBus Integration and Application
- The challenges of ensuring fault tolerance and redundancy in CANbus networks
The Importance of Fault Tolerance and Redundancy in CANbus Networks
In the automotive industry, vehicle diagnostics and telematics have become integral parts of modern vehicles. These technologies enable remote monitoring and management of vehicles, providing valuable insights into vehicle health and performance. One crucial component that enables the seamless flow of data in these systems is the CANbus network.
What is CANbus Communication?
CANbus, which stands for Controller Area Network bus, is a communication protocol used in automotive and industrial applications. It allows various electronic devices within a vehicle to communicate with each other effectively. CANbus networks are designed to be robust, reliable, and fault-tolerant, ensuring the uninterrupted flow of data between different components.
Modern vehicles rely heavily on electronic systems for various functions, including engine management, braking, transmission, and more. These systems generate a vast amount of data that needs to be processed and exchanged in real-time. CANbus networks provide a standardized way for different devices to communicate and share information, enabling efficient vehicle operation and diagnostics.
The Challenges of Fault Detection in CANbus Networks
Fault detection is a critical aspect of maintaining the reliability and safety of CANbus networks. As these networks become more complex with the integration of additional devices and functionalities, identifying faults and diagnosing issues becomes increasingly challenging.
One of the primary challenges in fault detection is identifying the root cause of a fault. CANbus networks consist of multiple interconnected devices, and a fault in one device can affect the functionality of the entire network. Detecting and isolating faults can be time-consuming and require specialized diagnostic tools.
Another challenge is the sheer volume of data generated by the numerous devices connected to the CANbus network. Analyzing this data manually can be overwhelming and prone to human error. Therefore, implementing automated fault detection algorithms and systems is crucial to ensure timely and accurate identification of faults.
Importance of Redundancy in CANbus Networks
To enhance the fault tolerance of CANbus networks, redundancy is a key consideration. Redundancy involves duplicating critical components or introducing backup systems to ensure uninterrupted communication and operation in the event of a failure.
One common approach to achieving redundancy in CANbus networks is through the use of dual-bus architectures. Dual-bus systems consist of two physically separate CANbus networks running in parallel. If a fault occurs in one bus, the system can seamlessly switch to the redundant bus, ensuring uninterrupted communication and preventing data loss.
Redundancy can also be achieved by introducing backup devices or modules that can take over in case of a failure. These backup devices monitor the primary devices and automatically activate when a fault is detected. This redundancy mechanism ensures continuous operation and minimizes the impact of failures on the overall system.
Integrating Fault Tolerance and Redundancy in CANbus Solutions
Automotive manufacturers and technology providers are continuously working on developing robust CANbus solutions that integrate fault tolerance and redundancy. These solutions aim to ensure the highest level of reliability and safety in vehicle diagnostics and telematics.
One approach to integrating fault tolerance and redundancy is through the use of advanced diagnostic tools. These tools enable efficient fault detection and diagnosis by leveraging machine learning and artificial intelligence algorithms. By analyzing the vast amount of data generated by the CANbus network, these tools can quickly identify anomalies and potential faults, allowing for proactive maintenance and reducing downtime.
Additionally, advancements in CANbus system integration have led to the development of more resilient and fault-tolerant networks. By implementing advanced error detection and correction mechanisms, such as error checking and redundancy checks, CANbus networks can detect and recover from errors more effectively.
Moreover, the integration of cloud-based vehicle data management systems has further enhanced fault tolerance and redundancy in CANbus networks. These systems enable real-time monitoring and analysis of vehicle data, allowing for remote diagnostics and troubleshooting. By leveraging the power of the cloud, automotive service providers can proactively identify and address faults, minimizing the impact on vehicle performance and safety.
The Future of Fault Tolerance and Redundancy in CANbus Networks
As vehicles become increasingly connected and autonomous, the demand for fault tolerance and redundancy in CANbus networks will continue to grow. The integration of advanced technologies, such as vehicle-to-vehicle communication and sensor fusion, will require even more robust and reliable communication systems.
Future CANbus solutions are likely to incorporate advanced fault detection algorithms and predictive maintenance capabilities. These technologies will enable vehicles to detect and address potential faults before they escalate, ensuring optimal performance and minimizing the risk of failures.
Additionally, the integration of artificial intelligence and machine learning algorithms will further enhance fault tolerance and redundancy in CANbus networks. These algorithms can analyze vast amounts of data in real-time, enabling proactive fault detection and automatic reconfiguration of the network to ensure uninterrupted communication.
Conclusion
The challenges of ensuring fault tolerance and redundancy in CANbus networks are critical considerations in the automotive industry. Vehicle diagnostics and telematics heavily rely on the seamless flow of data within the CANbus network, and any disruption can have significant consequences.
By integrating advanced fault detection algorithms, redundancy mechanisms, and cloud-based data management systems, automotive manufacturers and service providers can enhance the reliability and safety of CANbus networks. These advancements will enable more efficient vehicle diagnostics, proactive maintenance, and improved overall performance.
As the automotive industry continues to evolve, fault tolerance and redundancy in CANbus networks will play an increasingly vital role in ensuring the optimal operation of vehicles and the safety of passengers and road users.