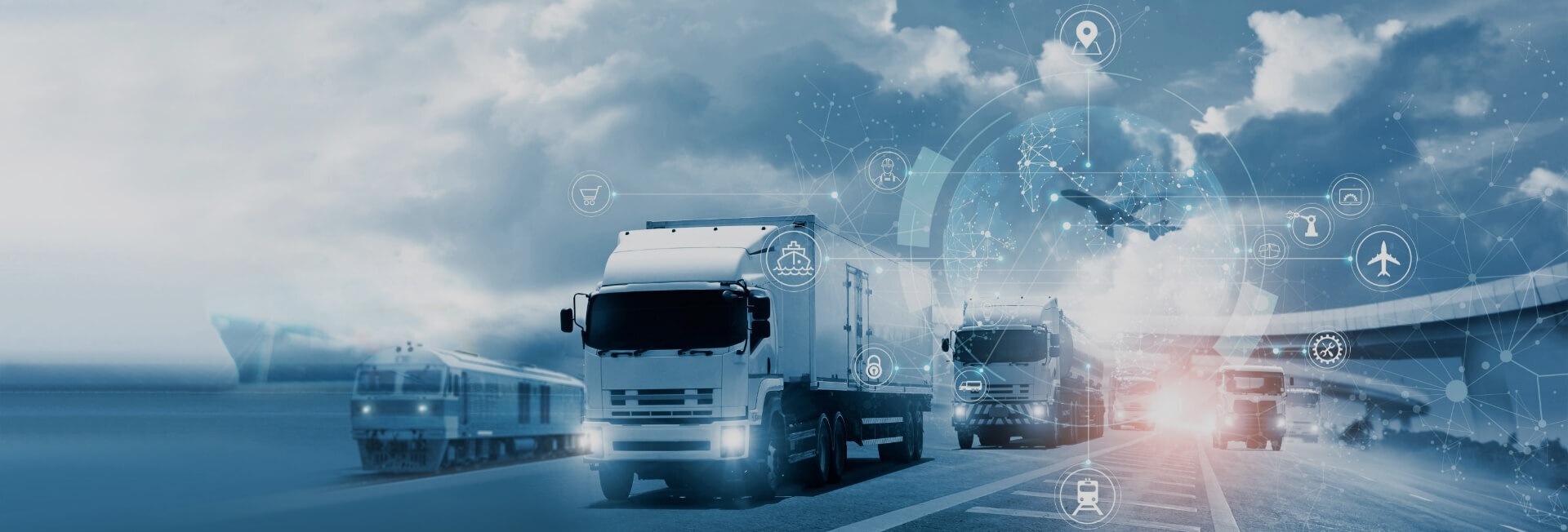
The challenges faced in developing CANBus diagnostic tools for heavy-duty vehicles
- Home
- Resources
- CANBus Integration and Application
- The challenges faced in developing CANBus diagnostic tools for heavy-duty vehicles
Developing CANBus diagnostic tools for heavy-duty vehicles is no easy task. These tools play a crucial role in vehicle diagnostics, fault detection, and remote vehicle diagnostics. However, they come with their own set of challenges that must be overcome to ensure accurate and reliable results. In this article, we will explore the challenges faced in developing CANBus diagnostic tools for heavy-duty vehicles and how they are being addressed.
The Importance of Vehicle Diagnostics and CANBus Communication
Vehicle diagnostics is the process of analyzing and monitoring the performance of a vehicle to detect any faults or issues. It involves collecting and analyzing data from various sensors and systems within the vehicle to identify potential problems before they become major issues. This can help prevent breakdowns, reduce maintenance costs, and improve overall vehicle performance.
CANBus communication is a key component of vehicle diagnostics. CANBus (Controller Area Network) is a standardized communication protocol used in modern vehicles to facilitate communication between various electronic control units (ECUs). It allows different ECUs to exchange information and control signals, enabling real-time monitoring and control of various vehicle systems.
The Challenges in Developing CANBus Diagnostic Tools
Developing CANBus diagnostic tools for heavy-duty vehicles is challenging due to a variety of factors. These challenges include:
1. Complex canbus Networks and Protocols
Heavy-duty vehicles have complex canbus networks consisting of multiple ECUs connected through the canbus interface. Each ECU communicates using specific canbus protocols, which vary depending on the manufacturer and vehicle model. Developing diagnostic tools that can accurately communicate with and interpret data from these diverse canbus networks and protocols is a major challenge.
2. Access to Vehicle Data
Accessing vehicle data is another significant challenge in developing CANBus diagnostic tools. Heavy-duty vehicles generate vast amounts of data related to engine performance, transmission, braking systems, and more. However, accessing this data securely and reliably can be difficult, especially in remote or fleet management scenarios. Ensuring proper data integration and management is crucial for effective vehicle diagnostics.
3. Compatibility with Multiple Vehicle Makes and Models
Heavy-duty vehicles come in various makes and models, each with its own unique canbus system and protocols. Developing diagnostic tools that are compatible with multiple vehicle makes and models is a complex task. It requires extensive testing and validation to ensure accurate data interpretation and compatibility across different vehicle types.
4. Real-Time Data Processing
Real-time data processing is essential for effective vehicle diagnostics. However, heavy-duty vehicles generate a significant amount of data that needs to be processed and analyzed in real-time. Ensuring efficient and reliable real-time data processing capabilities in diagnostic tools is a challenge that requires advanced algorithms and computing power.
Addressing the Challenges
Despite the challenges, significant progress has been made in developing CANBus diagnostic tools for heavy-duty vehicles. Various solutions and strategies are being implemented to address these challenges, including:
1. Advanced Data Integration and Management
Efforts are being made to improve data integration and management in CANBus diagnostic tools. This includes developing standardized data formats and protocols for seamless data exchange between different diagnostic tools and vehicle systems. Additionally, cloud-based solutions are being utilized for secure and efficient data storage and access.
2. Collaboration and Standardization
Collaboration between industry stakeholders, including vehicle manufacturers, diagnostic tool developers, and fleet operators, is crucial for addressing the challenges in developing CANBus diagnostic tools. By working together, they can establish common standards and protocols for canbus communication and data exchange, making it easier to develop compatible diagnostic tools.
3. Advanced Algorithms and Machine Learning
Advanced algorithms and machine learning techniques are being used to improve real-time data processing capabilities in diagnostic tools. These technologies enable faster and more accurate fault detection and diagnostics by analyzing large volumes of data in real-time. This helps in identifying potential issues before they escalate, reducing downtime and maintenance costs.
4. Continuous Testing and Validation
Continuous testing and validation are essential for ensuring the accuracy and reliability of CANBus diagnostic tools. Rigorous testing is conducted to verify the compatibility of diagnostic tools with different vehicle makes and models, as well as their ability to interpret canbus data correctly. This helps in identifying and addressing any issues or inconsistencies in the diagnostic tools.
Conclusion
Developing CANBus diagnostic tools for heavy-duty vehicles is a challenging task due to complex canbus networks, diverse canbus protocols, and the need for real-time data processing. However, through advanced data integration, collaboration, advanced algorithms, and continuous testing, these challenges are being addressed. The development of reliable and accurate CANBus diagnostic tools is crucial for efficient vehicle diagnostics, fault detection, and remote vehicle diagnostics in heavy-duty vehicles.