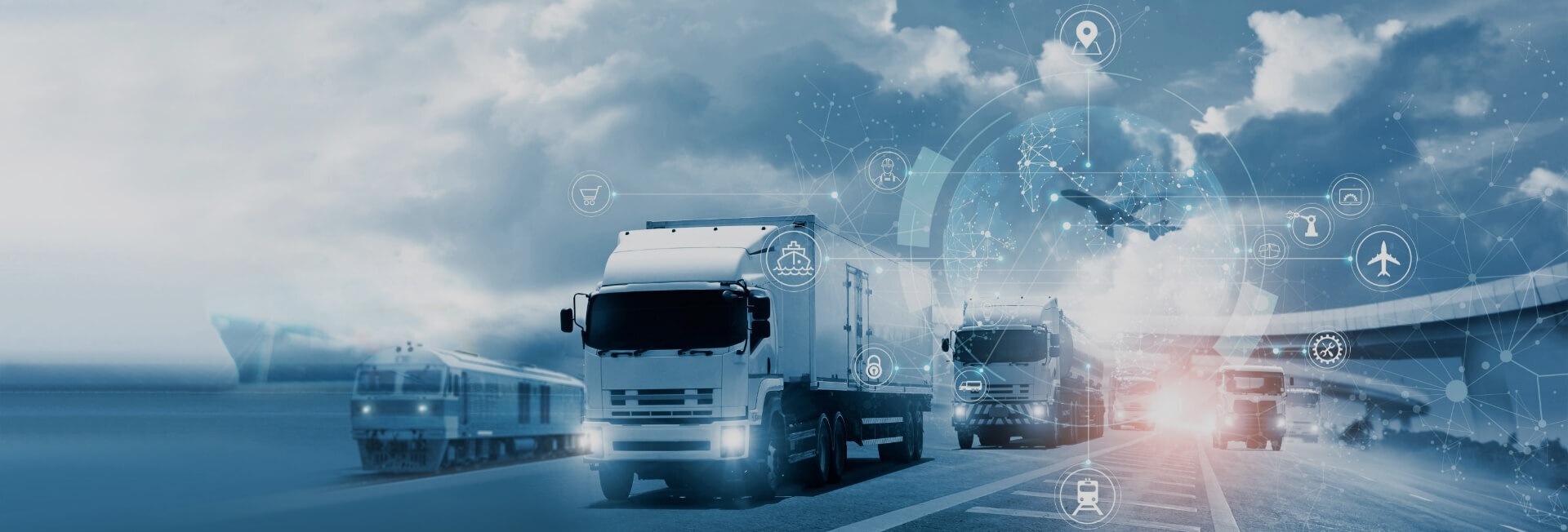
The benefits of using CANBus interface in railway and locomotive systems
- Home
- Resources
- CANBus Integration and Application
- The benefits of using CANBus interface in railway and locomotive systems
The Advantages of CANBus Interface in Railway and Locomotive Systems
Railway and locomotive systems are complex and require efficient communication and data management to function effectively. One of the key technologies that enable this is the CANBus interface. CANBus, short for Controller Area Network Bus, is a standard communication protocol used in various industries, including automotive, aerospace, and railway systems. In this article, we will explore the benefits of using CANBus interface in railway and locomotive systems and how it enhances vehicle diagnostics, fault detection, and remote vehicle diagnostics.
Enhanced Vehicle Diagnostics
Vehicle diagnostics is a critical aspect of railway and locomotive systems. It involves monitoring and analyzing various parameters and sensors within the vehicle to ensure optimal performance and identify any potential issues or faults. CANBus interface plays a crucial role in enhancing vehicle diagnostics by providing a standardized and efficient way of collecting and transmitting data from different devices and sensors in the vehicle.
With CANBus communication, different components of the railway system, such as the engine, brakes, traction control, and suspension, can exchange information seamlessly. This allows for real-time monitoring of critical parameters and early detection of any abnormalities or faults. By integrating CANBus interface into the vehicle's diagnostic system, engineers and maintenance personnel can access accurate and comprehensive data, enabling them to quickly diagnose and address any issues, thus reducing downtime and improving overall efficiency.
Remote Vehicle Diagnostics
Remote vehicle diagnostics is another significant advantage of using CANBus interface in railway and locomotive systems. Traditionally, diagnosing and troubleshooting issues in railway vehicles required physical access to the vehicle, which could be time-consuming and costly. However, with the integration of CANBus communication, remote vehicle diagnostics becomes a possibility.
CANBus allows for the transmission of vehicle data to a remote location, where it can be analyzed and interpreted by experts. This enables engineers and maintenance personnel to monitor the performance of multiple vehicles simultaneously, regardless of their physical location. By remotely accessing the vehicle's CANBus network, they can identify potential faults, diagnose issues, and even perform software updates or reprogramming, all without the need for physical presence. This significantly reduces maintenance costs, improves operational efficiency, and minimizes downtime.
Improved Fault Detection
Fault detection is crucial for ensuring the safety and reliability of railway and locomotive systems. By using CANBus interface, fault detection becomes more efficient and accurate. CANBus allows for the continuous monitoring of critical parameters, such as engine temperature, brake pressure, and wheel speed, among others. Any deviation from the expected values can trigger fault codes, which are then transmitted through the CANBus network.
These fault codes can be instantly detected and analyzed by onboard diagnostic systems or transmitted to a remote location for further analysis. This enables engineers to quickly identify the root cause of the fault and take appropriate actions to rectify it. By detecting faults early on, potential issues can be addressed before they escalate, reducing the risk of failures and accidents. Additionally, the integration of CANBus interface with advanced analytics and machine learning algorithms further enhances fault detection capabilities, allowing for predictive maintenance and proactive troubleshooting.
Seamless Automotive Data Integration
Integration of automotive data is essential for effective fleet management and decision-making. CANBus interface simplifies the process of data integration by providing a standardized protocol for communication between different devices and systems. With CANBus, data from various sensors and components can be collected, processed, and transmitted seamlessly, regardless of the manufacturer or technology used. This enables railway and locomotive systems to leverage a wide range of data sources, including engine performance, fuel consumption, maintenance records, and GPS location, among others.
By integrating CANBus interface with fleet management systems, operators can access real-time and historical data to monitor the performance of their vehicles, optimize fuel consumption, track maintenance schedules, and improve overall operational efficiency. Furthermore, CANBus data can be combined with other sources, such as weather conditions or traffic data, to gain deeper insights and make informed decisions regarding route planning, scheduling, and resource allocation.
Conclusion
The benefits of using CANBus interface in railway and locomotive systems are vast. From enhanced vehicle diagnostics and fault detection to remote vehicle diagnostics and seamless data integration, CANBus plays a critical role in improving the efficiency, safety, and reliability of railway operations. By leveraging the power of CANBus communication, railway operators can optimize maintenance processes, reduce downtime, and enhance overall operational performance. As technology continues to advance, the integration of CANBus interface with advanced analytics and machine learning capabilities will further revolutionize the railway industry, enabling predictive maintenance and proactive fault detection.