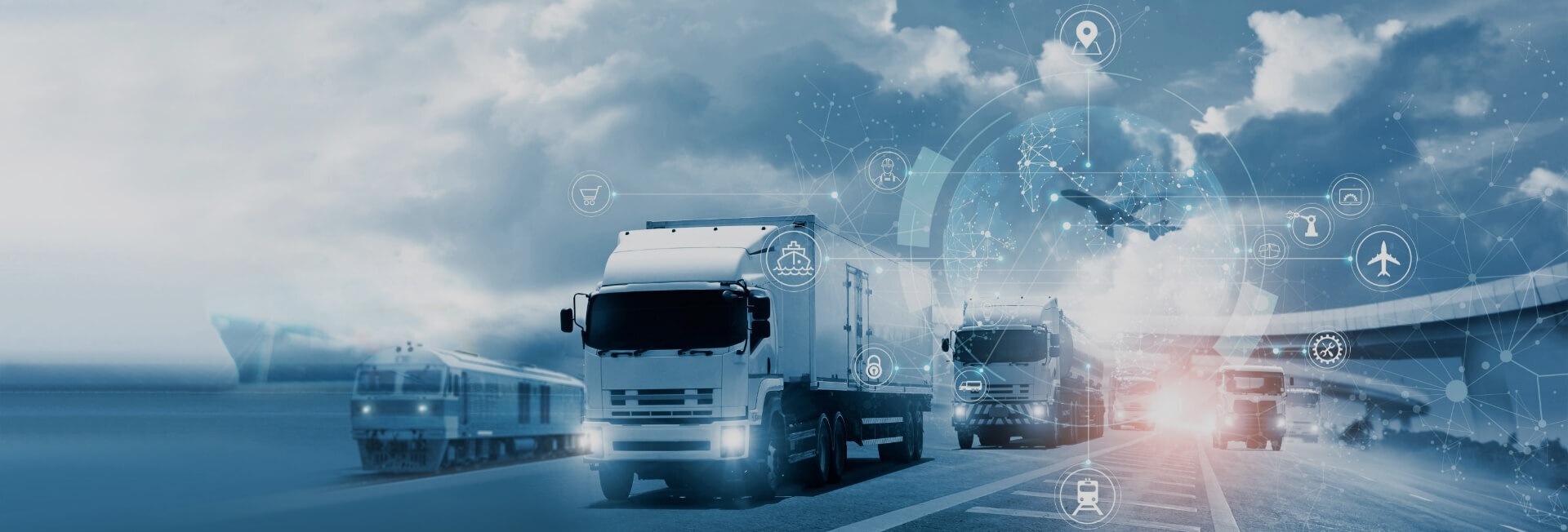
The advantages of using CANBus systems for real-time monitoring and control in manufacturing processes
- Home
- Resources
- CANBus Integration and Application
- The advantages of using CANBus systems for real-time monitoring and control in manufacturing processes
The Benefits of CANBus Systems for Real-time Monitoring and Control in Manufacturing Processes
In the world of manufacturing, efficiency and productivity are key factors that determine the success of a business. To achieve optimal performance, real-time monitoring and control of manufacturing processes is essential. One technology that has revolutionized this aspect of manufacturing is the Controller Area Network (CANBus) system. This article explores the advantages of using CANBus systems for real-time monitoring and control in manufacturing processes.
What is a CANBus System?
A Controller Area Network (CANBus) system is a communication network that allows various electronic devices within a manufacturing process to communicate with each other efficiently and effectively. It was originally developed by Bosch in the 1980s for automotive applications, but its benefits have extended to various other industries, including manufacturing.
A CANBus system consists of nodes or devices that are connected through a two-wire bus. These devices can be sensors, actuators, controllers, or any other electronic component involved in the manufacturing process. The CANBus system enables these devices to exchange information, monitor the process, and control the operation in real-time.
Advantages of Using CANBus Systems in Manufacturing Processes
1. Real-time Monitoring: One of the primary advantages of using CANBus systems in manufacturing processes is the ability to monitor the process in real-time. With CANBus, data can be transmitted and received in microseconds, allowing for instant feedback on the status of various components and parameters. This real-time monitoring enables manufacturers to identify and respond to issues promptly, minimizing downtime and improving overall productivity.
2. Fault Detection and Diagnosis: CANBus systems provide a robust platform for fault detection and diagnosis in manufacturing processes. By continuously monitoring the various devices and components connected to the CANBus network, manufacturers can quickly identify and diagnose faults or anomalies. This proactive approach to fault detection allows for timely maintenance and repairs, preventing costly breakdowns and reducing the risk of production delays.
3. Efficient Data Integration: CANBus systems facilitate seamless integration of data from multiple devices and sensors within the manufacturing process. The standardized CANBus protocols ensure that data is transmitted and received accurately, eliminating the need for complex data conversion processes. This efficient data integration enables manufacturers to gather comprehensive data from various sources, providing valuable insights for process optimization and decision-making.
4. Remote Monitoring and Control: CANBus systems can be easily integrated with remote monitoring and control systems, allowing manufacturers to oversee and manage their processes from a centralized location. This remote access provides flexibility and convenience, as manufacturers can monitor multiple production lines or facilities without the need for physical presence. Remote monitoring and control also enable timely interventions in case of any issues, ensuring uninterrupted production.
Implementing CANBus Systems in Manufacturing Processes
Implementing CANBus systems in manufacturing processes requires careful planning and consideration of various factors. Here are some key steps to follow:
1. Identify the Requirements: Start by identifying the specific requirements of your manufacturing process. Determine the types of devices and sensors that need to be connected and the data that needs to be monitored and controlled.
2. Select CANBus Devices: Choose the appropriate CANBus devices based on your requirements. Consider factors such as data transfer rate, number of nodes, and compatibility with existing equipment.
3. Design the CANBus Network: Design the CANBus network by determining the layout, topology, and wiring requirements. Ensure proper termination and grounding to minimize signal interference.
4. Integrate CANBus Protocols: Integrate the required CANBus protocols into your manufacturing process. This may involve configuring the devices and sensors to communicate using the CANBus protocol.
5. Implement Monitoring and Control Systems: Implement the necessary monitoring and control systems to leverage the data transmitted through the CANBus network. This may involve the use of software applications or dedicated hardware.
6. Train Personnel: Provide training to personnel involved in the operation and maintenance of the CANBus system. This will ensure that they have the necessary skills to effectively utilize the system and troubleshoot any issues that may arise.
Conclusion
CANBus systems offer significant advantages for real-time monitoring and control in manufacturing processes. From enabling real-time monitoring and fault detection to facilitating efficient data integration and remote access, CANBus systems have revolutionized the way manufacturers manage their processes. By implementing CANBus systems, manufacturers can improve productivity, reduce downtime, and make data-driven decisions for process optimization. With continuous advancements in technology, CANBus systems are expected to play an even more significant role in the future of manufacturing.