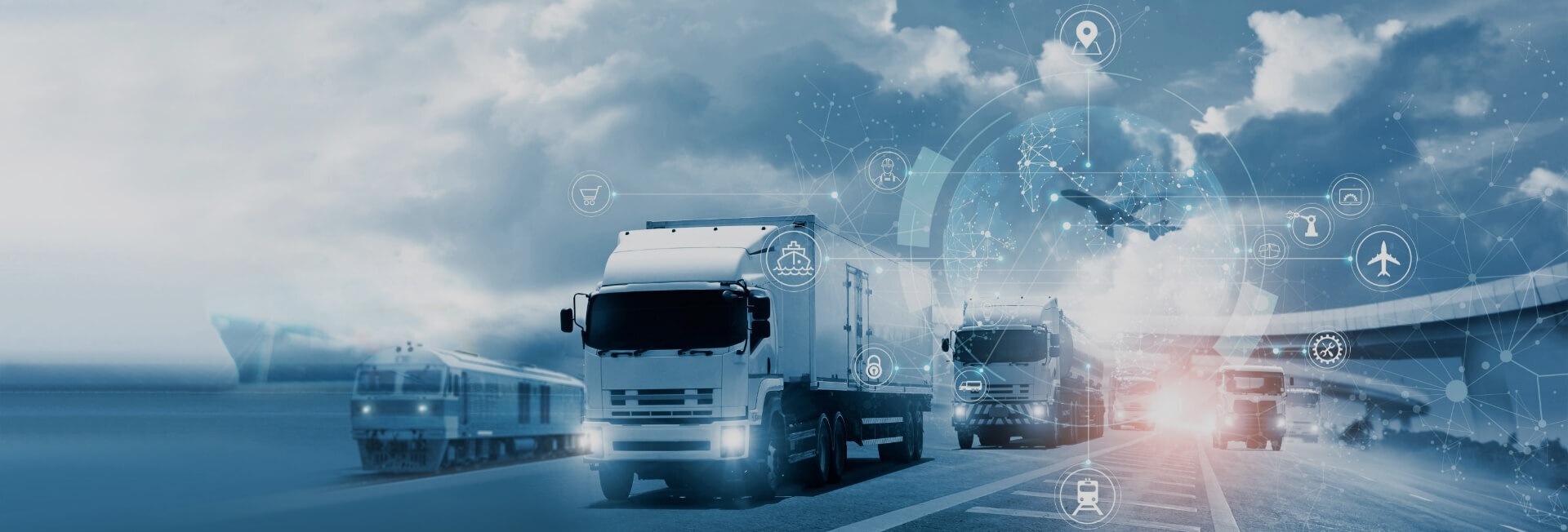
The advantages of using CANBus systems for real-time monitoring and control in industrial robotics
- Home
- Resources
- CANBus Integration and Application
- The advantages of using CANBus systems for real-time monitoring and control in industrial robotics
In the modern manufacturing industry, real-time monitoring and control are crucial for ensuring efficiency and productivity. Industrial robotics play a vital role in automating processes and increasing output. To achieve seamless integration and effective communication between various robotic components, the use of CANBus systems has become increasingly popular. CANBus, or Controller Area Network Bus, is a robust and reliable communication protocol that allows for real-time data exchange between devices. In this article, we will explore the advantages of using CANBus systems for real-time monitoring and control in industrial robotics.
Improved Efficiency and Productivity
One of the key advantages of using CANBus systems in industrial robotics is improved efficiency and productivity. CANBus communication enables real-time monitoring of robotic components, allowing for quick identification and resolution of any issues or faults. This proactive approach to maintenance minimizes downtime and ensures optimal performance of the robotic system. Additionally, CANBus systems allow for seamless integration of various robotic components, resulting in improved overall efficiency and productivity.
Furthermore, CANBus systems facilitate remote vehicle diagnostics, enabling technicians to monitor and diagnose robotic systems from a centralized location. This eliminates the need for on-site visits and reduces maintenance costs. With remote vehicle diagnostics, technicians can quickly identify and address any issues, maximizing uptime and minimizing disruptions to production.
Enhanced Fault Detection and Diagnostics
Fault detection and diagnostics are critical in maintaining the health and performance of industrial robotic systems. CANBus systems provide a comprehensive solution for fault detection and diagnostics. By continuously monitoring the various components of the robotic system, CANBus systems can quickly detect any abnormalities or malfunctions. This early detection allows for timely intervention and prevents any potential damage or breakdowns.
Additionally, CANBus systems offer a range of diagnostic tools that facilitate efficient troubleshooting and problem-solving. These diagnostic tools provide detailed information about the status and performance of each component, allowing technicians to quickly identify the root cause of any issues. This targeted approach to diagnostics saves time and resources, as technicians can focus on resolving specific problems rather than conducting extensive and time-consuming manual inspections.
Seamless Integration and Compatibility
CANBus systems are known for their seamless integration capabilities and compatibility with a wide range of devices. Industrial robotics often consist of multiple components from different manufacturers, each with its own communication protocol. CANBus acts as a universal language, allowing these components to communicate and work together seamlessly.
Moreover, CANBus systems support various canbus protocols, making them compatible with different devices and systems. This flexibility enables manufacturers to choose the most suitable components for their robotic systems without worrying about compatibility issues. Whether it's sensors, actuators, or control units, CANBus systems can integrate them all, creating a cohesive and efficient robotic system.
Real-Time Data Monitoring and Management
Real-time data monitoring and management are essential for optimizing industrial robotic systems. CANBus systems provide a wealth of data regarding the performance and status of each component, allowing for informed decision-making and proactive maintenance.
With CANBus systems, manufacturers can monitor critical parameters such as temperature, pressure, and voltage in real-time. This real-time monitoring enables technicians to identify any deviations from the normal operating conditions and take appropriate actions to prevent potential issues. Furthermore, CANBus systems can store and analyze historical data, providing valuable insights into the long-term performance and health of the robotic system.
Additionally, CANBus systems facilitate efficient vehicle data management. The vast amount of data generated by industrial robotics can be overwhelming to handle manually. CANBus systems automate the collection, storage, and analysis of this data, making it easier for manufacturers to track and manage the performance of their robotic systems. Real-time data monitoring and management enable manufacturers to make data-driven decisions and optimize the efficiency and productivity of their operations.
Conclusion
In conclusion, CANBus systems offer numerous advantages for real-time monitoring and control in industrial robotics. From improved efficiency and productivity to enhanced fault detection and diagnostics, CANBus communication and diagnostic tools revolutionize the manufacturing industry. The seamless integration and compatibility of CANBus systems enable manufacturers to create cohesive and efficient robotic systems. Real-time data monitoring and management provided by CANBus systems empower manufacturers to optimize their operations and make informed decisions.