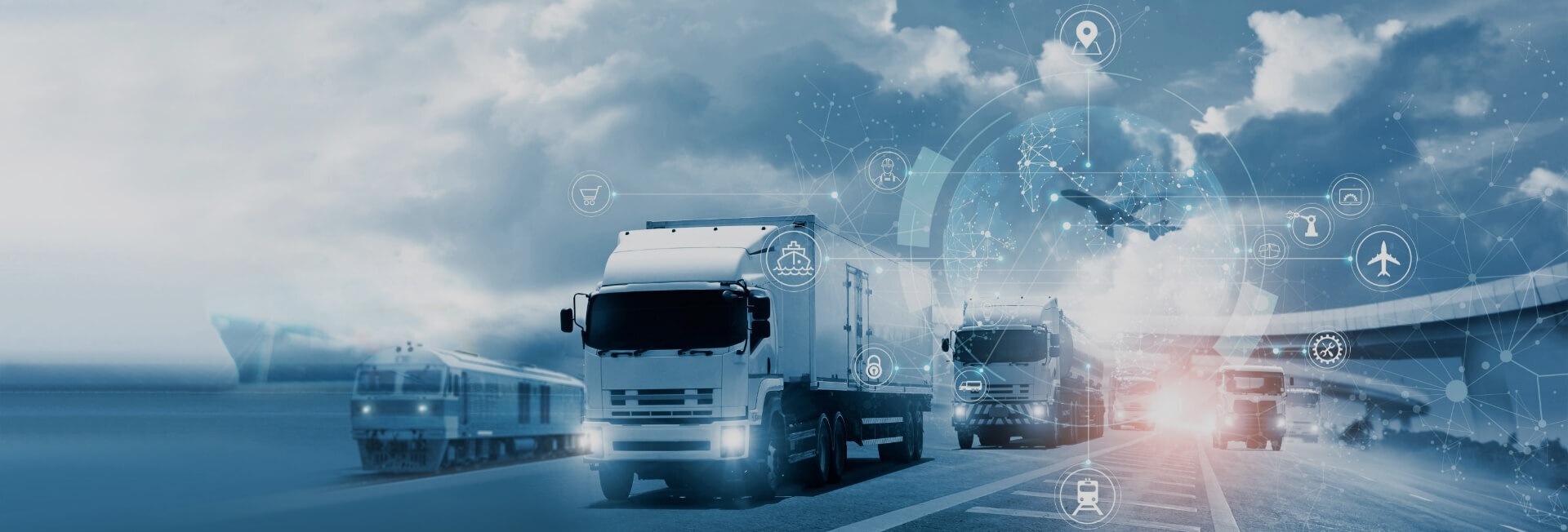
The advantages of using CANBus systems for real-time monitoring and control in chemical plants
- Home
- Resources
- CANBus Integration and Application
- The advantages of using CANBus systems for real-time monitoring and control in chemical plants
The Power of CANBus Systems for Real-Time Monitoring and Control in Chemical Plants
In today's rapidly advancing technology landscape, industries across the board are embracing innovative solutions to enhance productivity, efficiency, and safety. Chemical plants, in particular, are leveraging the power of CANBus systems for real-time monitoring and control, revolutionizing their operations and streamlining processes like never before.
What is CANBus Communication?
CANBus, short for Controller Area Network, is a robust communication protocol widely used in the automotive industry for vehicle diagnostics, telematics, and fault detection. It allows multiple electronic control units (ECUs) within a vehicle to communicate with each other efficiently and securely, enabling seamless integration of automotive data.
But the benefits of CANBus communication extend beyond the automotive sector. Chemical plants can leverage the same technology to monitor and control various processes, ensuring optimal performance and safety throughout the facility. By integrating CANBus systems into their operations, chemical plants can unlock a host of advantages that can significantly impact their bottom line.
Advantages of Using CANBus Systems in Chemical Plants
1. Real-Time Monitoring and Control:
CANBus systems provide chemical plants with real-time visibility into their operations. By connecting various sensors and control devices to the CANBus network, plant operators can monitor critical parameters such as temperature, pressure, flow rates, and chemical levels in real-time. This level of monitoring enables proactive decision-making, allowing operators to respond quickly to any deviations or anomalies, preventing potential accidents or equipment failures.
2. Enhanced Fault Detection and Diagnostics:
One of the key advantages of CANBus systems is their ability to detect faults and diagnose issues in real-time. By continuously monitoring the CANBus network, chemical plants can identify any abnormalities or malfunctions in their equipment or processes. This proactive approach to fault detection enables early intervention and preventive maintenance, minimizing downtime and reducing the risk of costly repairs.
3. Remote Monitoring and Diagnostics:
CANBus systems facilitate remote monitoring and diagnostics, allowing plant operators to access critical data and perform diagnostics from a centralized location. This remote access eliminates the need for manual inspections, reducing the time and effort required for maintenance tasks. Additionally, remote diagnostics enable quick troubleshooting and issue resolution, enhancing overall operational efficiency.
4. Improved Efficiency and Productivity:
By leveraging the power of CANBus systems, chemical plants can optimize their processes and improve overall efficiency. Real-time monitoring and control enable plant operators to make data-driven decisions, adjust parameters on the fly, and optimize resource allocation. This level of control and automation leads to increased productivity, reduced waste, and improved operational performance.
Integration of CANBus Systems in Chemical Plants
Integrating CANBus systems into existing chemical plant infrastructure requires careful planning and implementation. Here are some key considerations:
1. CANBus Network Design:
Designing a robust and scalable CANBus network is crucial for effective implementation. Plant operators must carefully analyze their requirements, identify critical parameters to monitor, and determine the number and placement of sensors and control devices. This network design phase ensures optimal connectivity and seamless data transmission within the facility.
2. Selection of CANBus Devices and Protocols:
Choosing the right CANBus devices and protocols is essential to ensure compatibility and interoperability within the plant's ecosystem. There are various CANBus protocols available, such as CAN 2.0, CAN FD, and J1939, each with its own advantages and use cases. Plant operators must evaluate their specific needs and select the appropriate devices and protocols accordingly.
3. CANBus System Integration:
Integrating the CANBus system with existing plant control systems is a critical step in the implementation process. This integration allows seamless data exchange between the CANBus network and the plant's supervisory control and data acquisition (SCADA) system or distributed control system (DCS), enabling centralized monitoring and control of all critical processes.
4. Training and Maintenance:
Proper training of plant operators and maintenance personnel is essential to maximize the benefits of CANBus systems. Operators must be familiar with the CANBus interface, diagnostic tools, and troubleshooting techniques to effectively monitor and control the plant's processes. Additionally, regular maintenance and updates of the CANBus network are crucial to ensure its reliability and performance.
Conclusion
The adoption of CANBus systems for real-time monitoring and control in chemical plants offers significant advantages, including enhanced safety, improved efficiency, and proactive fault detection. By leveraging CANBus communication, chemical plants can optimize their operations, reduce downtime, and ensure compliance with industry regulations. As technology continues to evolve, CANBus systems will play a vital role in shaping the future of chemical plant operations.