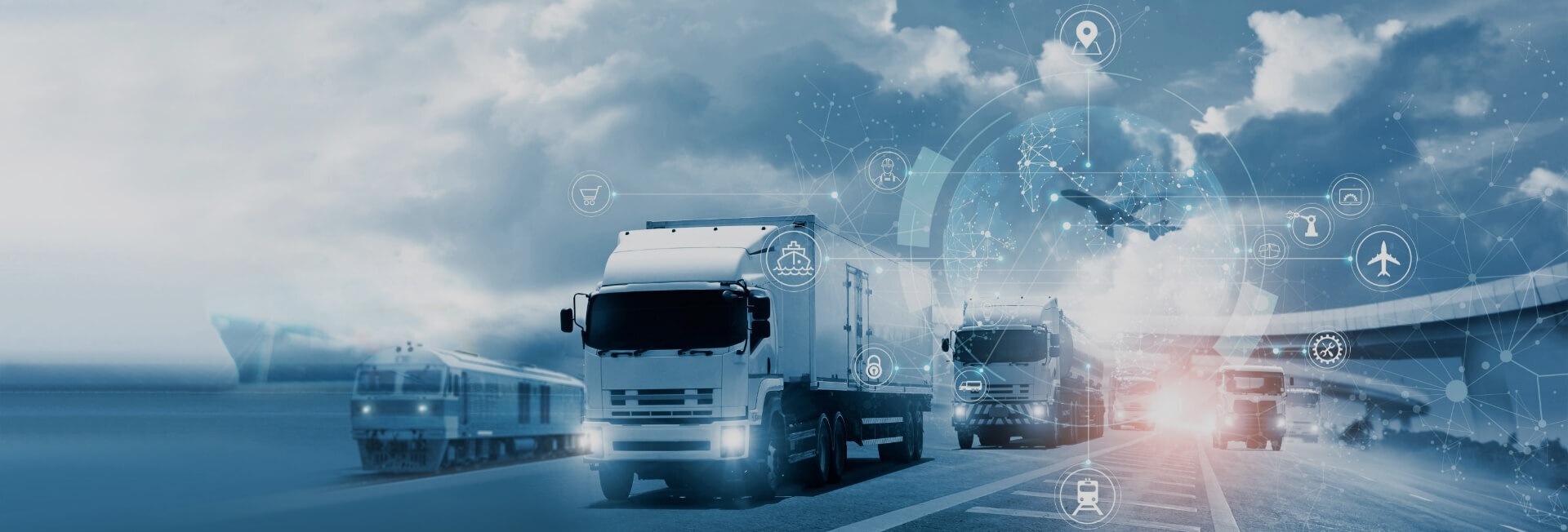
The advantages of using CANBus systems for predictive maintenance in manufacturing plants
- Home
- Resources
- CANBus Integration and Application
- The advantages of using CANBus systems for predictive maintenance in manufacturing plants
The Advantages of Using CANBus Systems for Predictive Maintenance in Manufacturing Plants
In today's fast-paced manufacturing industry, downtime can be a costly and disruptive issue. From equipment failures to unexpected maintenance needs, any disruption in the production process can result in lost time and revenue. That is why many manufacturing plants are turning to predictive maintenance solutions to minimize the risk of downtime and keep their operations running smoothly. One such solution that has gained popularity is the use of CANBus systems for predictive maintenance.
What is CANBus Communication?
CANBus communication, short for Controller Area Network Bus, is a communication protocol used in the automotive and manufacturing industries. It allows various electronic devices within a vehicle or manufacturing plant to communicate with each other, sharing information and coordinating their actions. This communication network is essential for the proper functioning of the various systems within a vehicle or manufacturing plant.
By integrating predictive maintenance systems with CANBus communication, manufacturers can gain valuable insights into the health and performance of their equipment. This allows them to detect potential issues before they escalate into major problems, minimizing downtime and reducing maintenance costs.
The Role of Vehicle Diagnostics in Predictive Maintenance
Vehicle diagnostics play a crucial role in predictive maintenance. They involve monitoring and analyzing various parameters and performance indicators of vehicles or equipment to identify any potential faults or issues. By using CANBus communication, manufacturers can access real-time data from their equipment, enabling them to monitor its performance and detect any anomalies.
With the help of vehicle telematics and CANBus communication, manufacturers can remotely monitor the health and performance of their equipment. This allows them to identify any potential issues and take proactive measures to address them before they cause any significant disruption. By leveraging vehicle diagnostics and CANBus communication, manufacturers can achieve greater efficiency and reduce the risk of unexpected downtime.
The Benefits of Fault Detection via CANBus
Fault detection is another key advantage of using CANBus systems for predictive maintenance. By continuously monitoring the data transmitted through the CANBus network, manufacturers can quickly detect any faults or abnormalities in their equipment. This allows them to take immediate action and prevent any potential failures or breakdowns.
With the help of CANBus diagnostic tools, manufacturers can analyze the data collected from their equipment and identify patterns or trends that indicate potential issues. This allows them to schedule maintenance activities proactively and replace or repair any faulty components before they cause any major problems. By detecting faults early on, manufacturers can significantly reduce downtime and avoid costly repairs.
Integration of CANBus Systems with Predictive Maintenance Solutions
One of the significant advantages of using CANBus systems for predictive maintenance is their compatibility with various predictive maintenance solutions. CANBus communication allows manufacturers to integrate their equipment with advanced analytics platforms and machine learning algorithms. This enables them to analyze the data collected from their equipment and make accurate predictions about its health and performance.
By integrating CANBus systems with predictive maintenance solutions, manufacturers can automate the monitoring and analysis process. This eliminates the need for manual inspections and reduces the risk of human error. Through real-time monitoring and analysis, manufacturers can identify any potential issues and take immediate action, ensuring the continuous operation of their equipment and minimizing downtime.
Conclusion
Using CANBus systems for predictive maintenance offers numerous benefits for manufacturing plants. The integration of CANBus communication allows manufacturers to monitor the health and performance of their equipment in real-time, enabling them to detect potential issues before they escalate. By leveraging vehicle diagnostics and fault detection via CANBus, manufacturers can minimize downtime and reduce maintenance costs.
The integration of CANBus systems with predictive maintenance solutions further enhances the effectiveness of the overall maintenance process. By automating the monitoring and analysis process, manufacturers can make accurate predictions about the health and performance of their equipment, allowing them to take proactive measures and prevent any major disruptions.
In conclusion, the use of CANBus systems for predictive maintenance in manufacturing plants is a game-changer. It improves efficiency, reduces downtime, and ultimately leads to cost savings. By embracing this technology, manufacturers can stay ahead of the competition and ensure the smooth operation of their production processes.