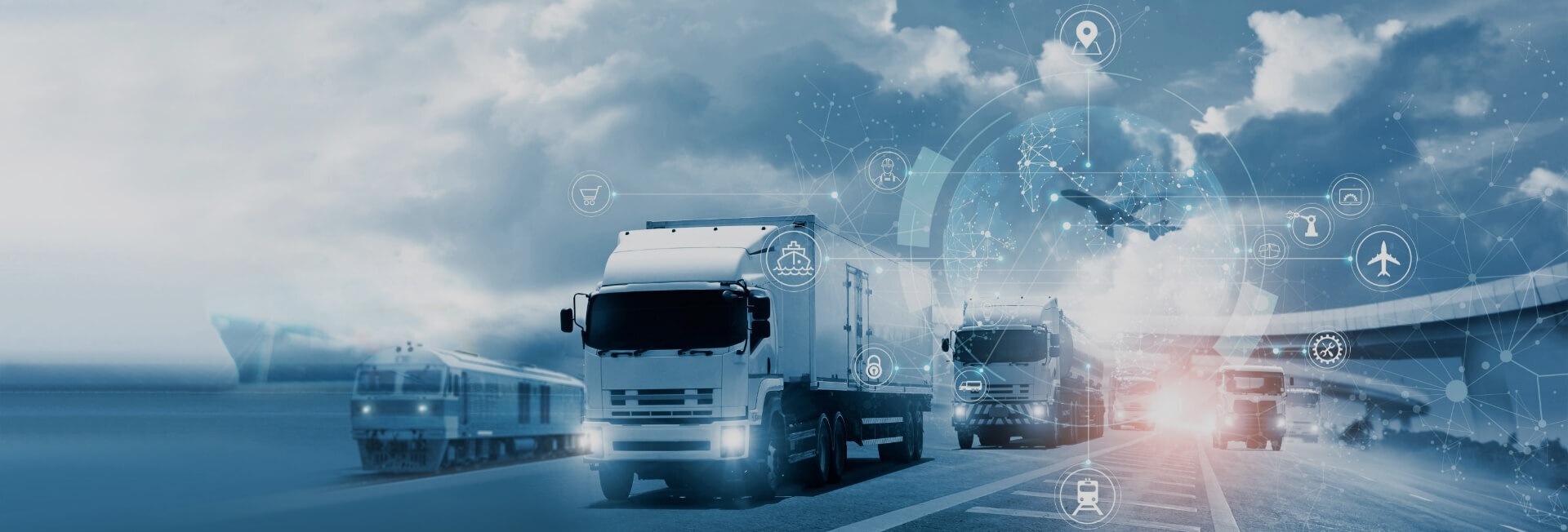
The advantages of using CANBus systems for condition monitoring and predictive maintenance in industrial plants
- Home
- Resources
- CANBus Integration and Application
- The advantages of using CANBus systems for condition monitoring and predictive maintenance in industrial plants
The Benefits of Implementing CANBus Systems for Condition Monitoring and Predictive Maintenance
In industrial plants, the ability to monitor and maintain equipment is crucial for ensuring optimal performance and minimizing downtime. Traditional maintenance practices rely on scheduled inspections and reactive repairs, which can be time-consuming and costly. However, with the advancement of technology, condition monitoring and predictive maintenance have become more accessible and efficient.
What is CANBus?
CANBus, which stands for Controller Area Network, is a communication protocol that allows various electronic devices to communicate with each other in real-time. It was originally developed by Bosch in the 1980s for use in automotive applications but has since been adopted in various industries, including manufacturing and industrial automation. CANBus systems use a two-wire bus to transmit and receive messages between interconnected devices, enabling seamless data exchange.
The Advantages of Using CANBus Systems for Condition Monitoring
Condition monitoring is the process of continuously monitoring the health and performance of equipment to detect potential faults or failures before they occur. By implementing CANBus systems for condition monitoring, industrial plants can benefit from the following advantages:
1. Real-time Monitoring and Diagnostics
CANBus systems provide real-time monitoring and diagnostics capabilities, allowing plant operators to have a comprehensive view of the equipment's condition at any given time. Through the CANBus network, data from various sensors and devices can be collected and transmitted to a central monitoring system. This data can then be analyzed to identify any abnormalities or potential issues. Real-time monitoring enables proactive maintenance, reducing the risk of unexpected failures and costly downtime.
2. Improved Fault Detection and Predictive Maintenance
With CANBus systems, fault detection and predictive maintenance become more accurate and efficient. By analyzing the data collected from sensors and devices, it is possible to identify patterns and trends that indicate the early stages of equipment degradation or failure. This information can be used to schedule maintenance activities and replace or repair components before they cause a breakdown. Predictive maintenance reduces the likelihood of unplanned downtime, improves equipment reliability, and extends its lifespan.
3. Remote Monitoring and Diagnostics
CANBus systems enable remote monitoring and diagnostics, allowing plant operators to access equipment data and perform diagnostics from a centralized location. This eliminates the need for manual inspections and reduces the time and resources required for maintenance activities. Remote monitoring also enables real-time troubleshooting, as plant operators can remotely access devices and make adjustments or perform diagnostics without physically being present at the equipment location.
4. Integration with Existing Systems
CANBus systems can be easily integrated with existing plant systems and equipment. The CANBus interface allows for seamless communication between different devices, regardless of their manufacturer or protocol. This means that plant operators can leverage their existing infrastructure and equipment without the need for costly upgrades or replacements. The integration of CANBus systems with existing systems enables comprehensive data collection and analysis, providing a holistic view of the plant's operations and equipment health.
The Advantages of Using CANBus Systems for Predictive Maintenance
Predictive maintenance is a proactive maintenance strategy that aims to predict and prevent equipment failures before they occur. By leveraging CANBus systems for predictive maintenance, industrial plants can reap the following benefits:
1. Increased Equipment Reliability
By monitoring equipment condition in real-time and performing predictive maintenance based on the data collected, the reliability of equipment can be significantly increased. Identifying and addressing potential issues before they escalate into failures ensures that equipment operates at optimal performance levels, reducing the risk of unplanned downtime and production losses.
2. Cost Savings
Predictive maintenance enabled by CANBus systems can result in significant cost savings for industrial plants. By addressing maintenance needs proactively, plant operators can avoid costly emergency repairs and unplanned downtime. Additionally, predictive maintenance allows for better planning and scheduling of maintenance activities, reducing the impact on production and minimizing the need for spare parts inventory.
3. Improved Safety
Implementing CANBus systems for predictive maintenance enhances safety in industrial plants. By continuously monitoring equipment condition, potential safety hazards can be detected and addressed before they pose a risk to personnel or the environment. Predictive maintenance also reduces the likelihood of unexpected equipment failures, which can lead to accidents and injuries.
4. Enhanced Data Analysis and Reporting
CANBus systems provide vast amounts of data that can be leveraged for advanced analysis and reporting. By integrating CANBus data with analytics tools and software, plant operators can gain valuable insights into equipment performance, identify trends, and make informed decisions regarding maintenance strategies and resource allocation. The ability to analyze and report on equipment health and performance enables continuous improvement and optimization of maintenance practices.
Conclusion
Implementing CANBus systems for condition monitoring and predictive maintenance offers numerous advantages for industrial plants. Real-time monitoring and diagnostics, improved fault detection and predictive maintenance, remote monitoring and diagnostics, and integration with existing systems are just a few of the benefits. With the ability to monitor and maintain equipment more effectively, industrial plants can optimize performance, reduce downtime, and achieve significant cost savings.