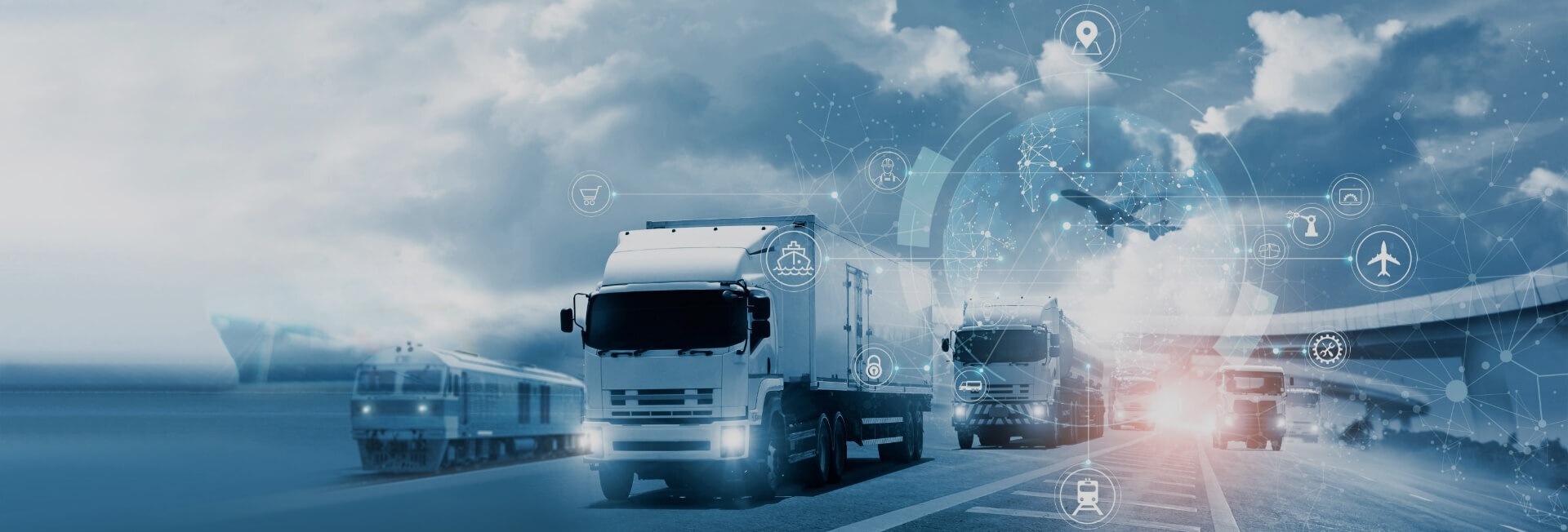
Fault detection techniques in chemical processing plants
- Home
- Resources
- CANBus Integration and Application
- Fault detection techniques in chemical processing plants
Fault Detection Techniques in Chemical Processing Plants
Fault detection is a critical aspect of maintaining the safety and efficiency of chemical processing plants. With the potential for hazardous incidents and costly downtime, it is essential to have robust systems in place to detect and address faults before they escalate. In this article, we will explore some of the techniques commonly used in chemical processing plants for fault detection.
1. Instrumentation and Sensors
One of the primary methods for fault detection in chemical processing plants is through the use of instrumentation and sensors. These devices are strategically placed throughout the plant to monitor various parameters such as temperature, pressure, flow rate, and chemical composition. By continuously monitoring these parameters, any deviations from the normal operating conditions can be quickly detected, indicating a potential fault or abnormality.
Modern sensors are capable of transmitting real-time data to a central control system, where it can be analyzed and compared to predefined thresholds or patterns. This allows for early detection of faults, enabling plant operators to take immediate corrective actions and prevent further damage or accidents.
2. Data Analysis and Machine Learning
With the advent of advanced data analysis techniques and machine learning algorithms, fault detection in chemical processing plants has become even more effective. By analyzing large volumes of sensor data, patterns and trends can be identified, allowing for the detection of subtle changes that may indicate the presence of a fault.
Machine learning algorithms can be trained on historical data to learn normal operating conditions and patterns. Once trained, these algorithms can continuously monitor real-time data and alert operators when deviations occur. This proactive approach to fault detection allows for early intervention, minimizing the impact on plant operations and reducing the risk of accidents.
3. Process Modeling and Simulation
Process modeling and simulation techniques are also widely used for fault detection in chemical processing plants. By creating mathematical models that represent the plant's various processes and equipment, virtual simulations can be performed to predict the expected behavior under different operating conditions.
These models can be used to identify potential faults by comparing the simulated results with the actual plant data. If there are significant discrepancies, it indicates the presence of a fault or abnormality that needs to be investigated further. This approach allows for proactive fault detection and facilitates targeted maintenance activities to prevent unexpected breakdowns or accidents.
4. Alarm Systems and Human-Machine Interfaces
Alarm systems and human-machine interfaces play a crucial role in fault detection in chemical processing plants. These systems provide visual and auditory alerts to plant operators when abnormal conditions are detected. By promptly notifying the operators, they can take immediate action to investigate and address the fault.
Modern alarm systems are designed to prioritize alerts based on severity and provide clear and concise information to aid decision-making. Human-machine interfaces, such as control room displays and operator consoles, provide real-time data visualization and facilitate efficient monitoring of plant operations. These interfaces often incorporate advanced features like trend analysis, historical data viewing, and remote access for enhanced fault detection capabilities.
Conclusion
Fault detection techniques play a crucial role in ensuring the safety and efficiency of chemical processing plants. Through the use of instrumentation and sensors, data analysis and machine learning, process modeling and simulation, as well as alarm systems and human-machine interfaces, potential faults can be detected early, allowing for timely intervention and prevention of accidents or downtime.
By integrating these techniques into the plant's overall control and monitoring systems, operators can gain better insights into the plant's health and take proactive measures to address any deviations from normal operating conditions. This results in improved safety, reduced downtime, and increased productivity in chemical processing plants.