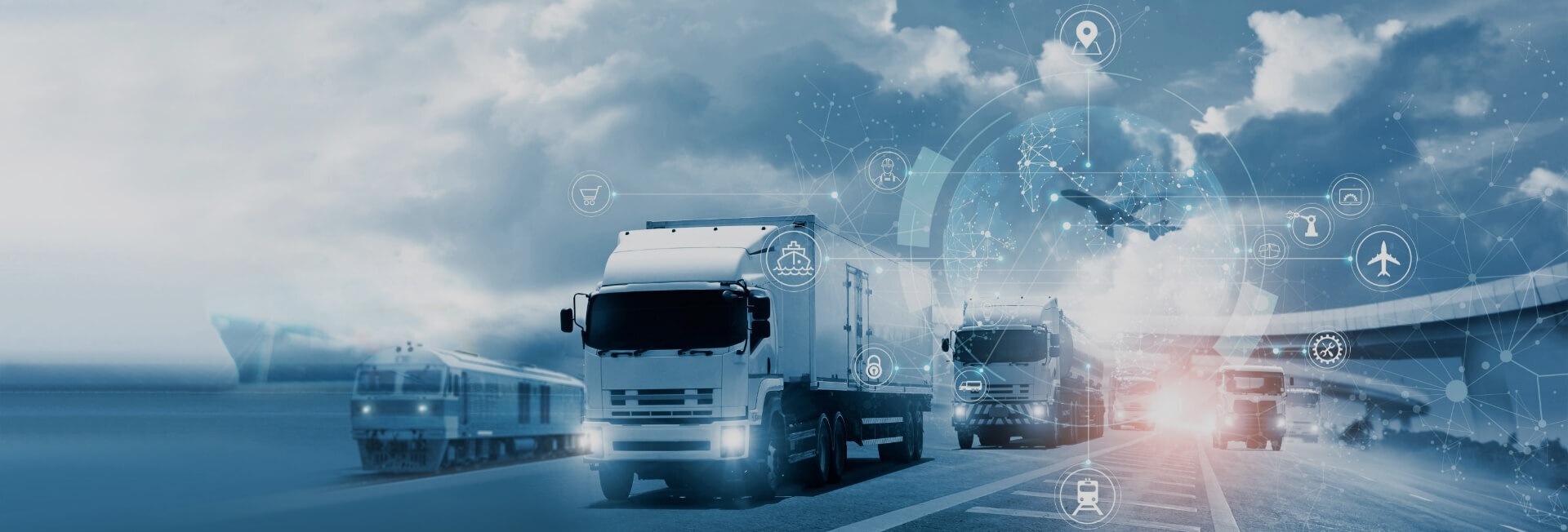
Fault detection in wind turbines
- Home
- Resources
- CANBus Integration and Application
- Fault detection in wind turbines
Fault Detection in Wind Turbines - Ensuring Reliable and Efficient Operations
Wind turbines play a crucial role in generating clean and renewable energy. As the demand for sustainable power sources continues to rise, it is essential to ensure the reliable and efficient operation of these turbines. One of the key aspects of achieving this is fault detection, which involves identifying and addressing any issues or abnormalities that may arise in the turbine system.
The Importance of Fault Detection
Fault detection is vital in wind turbines for several reasons. Firstly, it helps prevent costly and potentially dangerous failures. By identifying and addressing faults early on, operators can avoid major breakdowns that may require extensive repairs or even replacement of components. This not only saves time and money but also ensures the uninterrupted production of clean energy.
Secondly, fault detection allows for proactive maintenance. By continuously monitoring the performance of wind turbines and detecting any deviations from normal operation, operators can schedule maintenance activities in advance. This helps minimize downtime and ensures that the turbines are operating at their optimal efficiency.
Lastly, fault detection contributes to the overall safety of wind turbine operations. Identifying and addressing faults promptly reduces the risk of accidents or malfunctions that can harm both the turbine itself and the personnel working in its vicinity. This is especially important considering the size and complexity of modern wind turbines, which can reach heights of over 100 meters and have multiple moving parts.
Methods of Fault Detection
There are several methods and technologies employed for fault detection in wind turbines:
1. Vibration Analysis
Vibration analysis is a common technique used to detect faults in rotating machinery, including wind turbines. By monitoring vibrations in various components such as bearings, gearboxes, and generators, operators can identify any abnormal patterns or frequencies that may indicate a fault. This method is particularly effective in detecting issues such as misalignment, unbalance, and mechanical wear.
2. Temperature Monitoring
Temperature monitoring is another valuable tool for fault detection in wind turbines. By continuously measuring the temperature of critical components such as bearings and electrical connections, operators can identify overheating or abnormal temperature rises that may indicate a fault. This method is particularly effective in detecting issues related to lubrication, cooling, and electrical resistance.
3. Oil Analysis
Oil analysis involves regularly sampling and testing the lubricating oil used in wind turbine gearboxes. By analyzing the oil for various parameters such as viscosity, contamination, and wear metals, operators can detect any signs of degradation or abnormality. This method is particularly effective in detecting gearbox faults and can help prevent major breakdowns or catastrophic failures.
4. Condition Monitoring Systems
Condition monitoring systems (CMS) are comprehensive solutions that combine various sensors, data acquisition systems, and analytics tools to continuously monitor the condition of wind turbines. These systems collect data from multiple sources, such as vibration sensors, temperature sensors, and oil analysis results, and use advanced algorithms to detect and diagnose faults. They provide real-time insights into the health of the turbine system and enable operators to take proactive measures to address any issues.
Integration of Fault Detection Systems
Integrating fault detection systems into wind turbines involves connecting various sensors and monitoring devices to a centralized control system. This allows for real-time data collection, analysis, and decision-making. One commonly used method for integration is the use of a Controller Area Network (CANBus) communication protocol.
CANBus is a widely adopted communication standard in the automotive and industrial sectors. It enables the exchange of data between various components and subsystems of a wind turbine, including sensors, actuators, and control units. By integrating fault detection systems with the turbine's existing CANBus network, operators can access real-time data from multiple sources and implement advanced analytics algorithms for fault detection.
Benefits of CANBus Integration
Integrating fault detection systems with the wind turbine's CANBus network offers several benefits:
1. Real-Time Monitoring
By leveraging the existing CANBus infrastructure, operators can collect real-time data from various sensors and monitoring devices installed in the turbine. This enables them to monitor the health and performance of critical components continuously. Any anomalies or deviations from normal operation can be detected promptly, allowing for timely intervention.
2. Enhanced Diagnostic Capabilities
CANBus integration allows for the integration of advanced diagnostic tools and algorithms. By combining data from multiple sources and applying analytics techniques, operators can gain deeper insights into the condition of the turbine system. This enables them to identify potential faults or issues that may not be apparent through individual sensor readings.
3. Remote Monitoring and Diagnostics
Integration with the CANBus network enables remote monitoring and diagnostics of wind turbines. Operators can access real-time data and diagnostic information from anywhere, allowing for prompt decision-making and intervention. This is particularly beneficial for offshore wind farms or remote turbine locations where physical access may be challenging or time-consuming.
4. Predictive Maintenance
By continuously monitoring the condition of wind turbines and detecting any early signs of faults, operators can implement predictive maintenance strategies. This involves scheduling maintenance activities based on the actual condition of the turbine rather than predefined time intervals. Predictive maintenance helps optimize maintenance costs, minimize downtime, and extend the lifespan of turbine components.
Conclusion
Fault detection is a critical aspect of ensuring the reliable and efficient operation of wind turbines. By detecting and addressing faults early on, operators can prevent costly breakdowns, minimize downtime, and extend the lifespan of turbine components. Integrating fault detection systems with the turbine's existing CANBus network provides real-time monitoring, enhanced diagnostic capabilities, remote monitoring and diagnostics, and enables predictive maintenance strategies. With the increasing adoption of renewable energy sources, fault detection in wind turbines will continue to play a vital role in meeting the growing demand for clean and sustainable power.