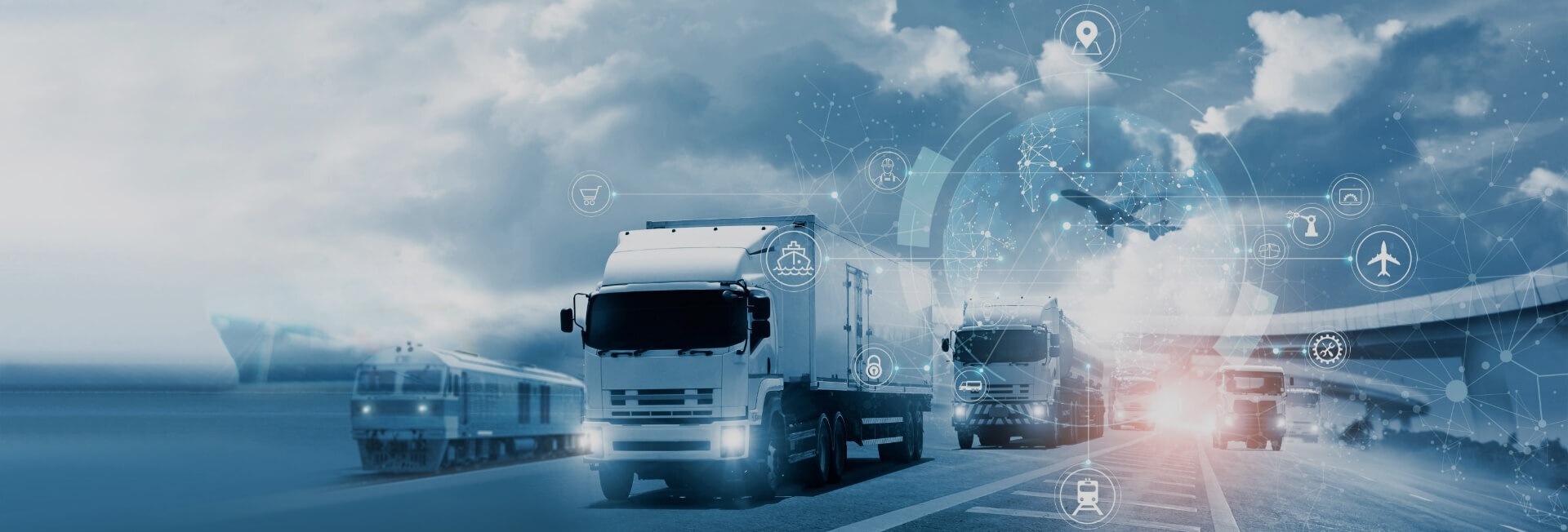
Fault detection in robotics systems
- Home
- Resources
- CANBus Integration and Application
- Fault detection in robotics systems
Fault Detection in Robotics Systems
In today's world, robotics systems are becoming increasingly complex and are being used in a wide range of applications. Whether it's autonomous vehicles, manufacturing robots, or even drones, these systems rely on advanced technology to operate efficiently and safely. However, just like any other mechanical or electronic system, robotics systems are prone to faults and failures. In order to ensure optimal performance and prevent costly breakdowns, fault detection plays a crucial role.
What is Fault Detection?
Fault detection is the process of identifying and diagnosing faults or abnormalities in a system. In the context of robotics systems, fault detection involves monitoring various parameters and signals to detect any deviations from normal operating conditions. By continuously monitoring the system, faults can be detected early on, allowing for timely repairs and maintenance.
Importance of Fault Detection in Robotics Systems
Fault detection in robotics systems is of utmost importance for several reasons:
- Preventing System Failures: Faults in robotics systems can lead to system failures, resulting in costly repairs and downtime. By detecting faults early on, preventive measures can be taken to avoid major failures.
- Ensuring Safety: In certain applications, such as autonomous vehicles, faults can lead to safety hazards. Fault detection helps in identifying potential safety risks and taking appropriate actions to mitigate them.
- Optimizing Performance: Faults can impact the performance and efficiency of robotics systems. By detecting and addressing faults, optimal performance can be maintained, leading to improved productivity and reduced energy consumption.
Methods of Fault Detection
There are several methods and techniques used for fault detection in robotics systems. Some of the commonly used methods include:
1. Vehicle Diagnostics
Vehicle diagnostics is a process of identifying, diagnosing, and resolving faults in automotive systems. It involves the use of advanced diagnostic tools and techniques to analyze the vehicle's performance and identify any potential issues. Vehicle diagnostics can be performed manually by trained technicians or can be done remotely using vehicle telematics and remote vehicle diagnostics systems.
2. CANBus Communication
CANBus (Controller Area Network) is a communication protocol used in vehicles and robotics systems to enable communication between various electronic control units (ECUs). It allows for the exchange of information and data between different components of the system, including sensors, actuators, and control units. By monitoring the CANBus communication, faults and abnormalities can be detected, enabling timely repairs and maintenance.
3. Automotive Data Integration
Automotive data integration involves the collection and integration of data from various sensors and systems in a vehicle. By analyzing this data, faults and abnormalities can be detected, allowing for proactive maintenance and repairs. This can be done using advanced data analytics techniques and machine learning algorithms.
4. CANBus Diagnostic Tools
CANBus diagnostic tools are specialized devices used for monitoring and diagnosing faults in CANBus networks. These tools allow for real-time monitoring of CANBus communication, detection of faults, and analysis of data. They provide valuable insights into the state of the system and help in identifying potential issues before they escalate into major failures.
Benefits of Fault Detection in Robotics Systems
Fault detection in robotics systems offers several benefits:
- Cost Savings: By detecting faults early on, costly breakdowns and repairs can be avoided. This helps in reducing maintenance costs and improving the overall lifespan of the system.
- Improved Safety: Fault detection helps in identifying potential safety hazards and taking appropriate actions to mitigate them. This ensures the safety of operators and other individuals working in the vicinity of robotics systems.
- Enhanced Performance: By addressing faults and abnormalities, the performance and efficiency of robotics systems can be optimized. This leads to improved productivity and reduced energy consumption.
- Proactive Maintenance: Fault detection enables proactive maintenance, allowing for timely repairs and replacements. This helps in minimizing downtime and maximizing the availability of the system.
- Data-Driven Decision Making: Fault detection systems generate a wealth of data that can be used for data-driven decision making. By analyzing this data, insights can be gained into the performance and health of the system, enabling informed decision making.
Conclusion
Fault detection plays a critical role in ensuring the optimal performance and safety of robotics systems. By continuously monitoring the system and detecting faults early on, proactive measures can be taken to prevent major failures and breakdowns. Whether it's vehicle diagnostics, CANBus communication, or advanced data integration, fault detection techniques offer valuable insights into the health of robotics systems. By leveraging these techniques, organizations can improve the reliability, efficiency, and safety of their robotics systems, leading to better overall performance and reduced costs.