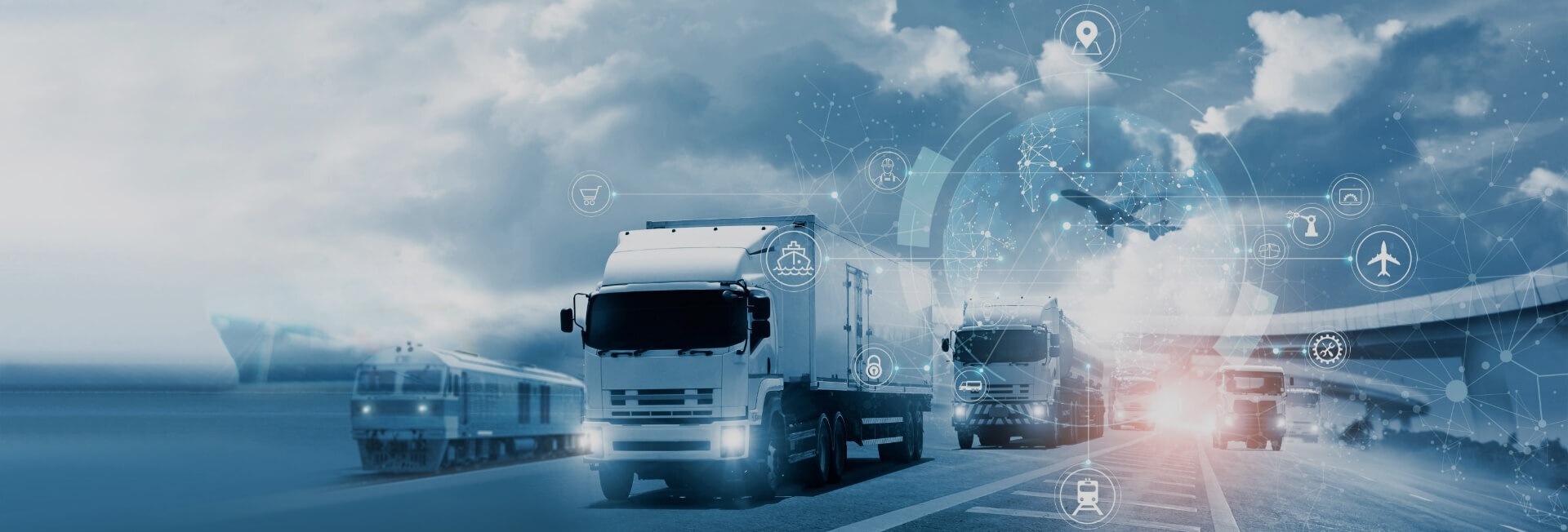
Fault detection in railway signaling systems
- Home
- Resources
- CANBus Integration and Application
- Fault detection in railway signaling systems
Fault Detection in Railway Signaling Systems - Ensuring Safety and Efficiency
Railway signaling systems play a critical role in ensuring the safe and efficient operation of trains. These systems, consisting of various components and subsystems, are responsible for controlling train movements, maintaining safe distances between trains, and preventing collisions. However, like any complex system, railway signaling systems are prone to faults and failures. Detecting and resolving these faults in a timely manner is crucial to maintain the safety and reliability of the railway network.
The Importance of Fault Detection
Fault detection in railway signaling systems is essential to prevent accidents and ensure the smooth operation of trains. A fault in the signaling system can lead to incorrect train movements, collisions, or even derailments, putting the lives of passengers and railway staff at risk. Additionally, a faulty signaling system can cause delays and disruptions in train schedules, leading to inconvenience for passengers and financial losses for railway operators.
Traditionally, fault detection in railway signaling systems relied heavily on manual inspections and visual observations. However, this approach is time-consuming, error-prone, and not always effective in identifying hidden or intermittent faults. To overcome these limitations, modern railway signaling systems are equipped with advanced fault detection mechanisms, including vehicle diagnostics and telematics.
Vehicle Diagnostics and Telematics
Vehicle diagnostics and telematics technology have revolutionized the way faults are detected and managed in railway signaling systems. By integrating sensors, data loggers, and communication modules into trains, it is now possible to continuously monitor the health and performance of various signaling system components in real-time.
Vehicle telematics systems collect and transmit data from the train's onboard sensors and systems to a central monitoring station. This data includes crucial information about the condition of signaling system components, such as switches, signals, track circuits, and interlockings. By analyzing this data, railway operators can proactively detect potential faults and take timely corrective actions, preventing accidents and minimizing disruptions.
CANBus Communication and Fault Detection
A key component of vehicle diagnostics and telematics in railway signaling systems is the Controller Area Network (CANBus) communication. CANBus is a standardized communication protocol used in modern trains to enable the exchange of data between various onboard systems and components. It allows for real-time monitoring and control of critical functions, including fault detection and diagnostics.
Through CANBus communication, the onboard sensors and systems continuously transmit data about the health and performance of signaling system components to a central control unit. This data can include parameters such as voltage levels, current flows, temperature readings, and error codes. By analyzing this data, railway operators can identify abnormal behavior, potential faults, or signs of imminent failures.
Furthermore, CANBus communication enables remote vehicle diagnostics, which allows for the monitoring and analysis of signaling system components from a central location. This eliminates the need for manual inspections and reduces the downtime required for fault detection and resolution. Remote vehicle diagnostics also enable railway operators to manage their fleet more efficiently and allocate resources effectively.
Integrating Automotive Data for Effective Fault Detection
In addition to CANBus communication, integrating automotive data from various sources can enhance the effectiveness of fault detection in railway signaling systems. By integrating data from other onboard systems, such as the traction control system, braking system, and propulsion system, railway operators can gain a comprehensive view of the train's overall health and performance.
Automotive data integration allows for the correlation of data from different systems, enabling the detection of complex faults and interdependencies between subsystems. For example, a fault in the braking system may affect the performance of the signaling system, and vice versa. By analyzing integrated data, railway operators can identify these interdependencies and take appropriate corrective actions.
CANBus Interface and Fault Detection Tools
To effectively utilize CANBus communication and integrate automotive data, railway operators require specialized tools and interfaces. CANBus diagnostic tools provide the capability to monitor, analyze, and interpret the data transmitted over the CANBus network. These tools can capture and display real-time data, generate diagnostic reports, and provide alerts for potential faults or abnormal conditions.
Additionally, CANBus interface devices allow for seamless integration of automotive data from various sources. These devices act as gateways between the onboard systems and the central monitoring station, enabling the transmission of data in a standardized format. They also provide the necessary protocols and interfaces to communicate with different types of onboard systems and components.
Conclusion
Fault detection in railway signaling systems is of utmost importance to ensure the safety and efficiency of the railway network. Vehicle diagnostics, telematics, and CANBus communication play a crucial role in this process, allowing for real-time monitoring, analysis, and proactive fault detection. By integrating automotive data and utilizing specialized tools and interfaces, railway operators can effectively manage the health and performance of signaling system components, preventing accidents and minimizing disruptions.