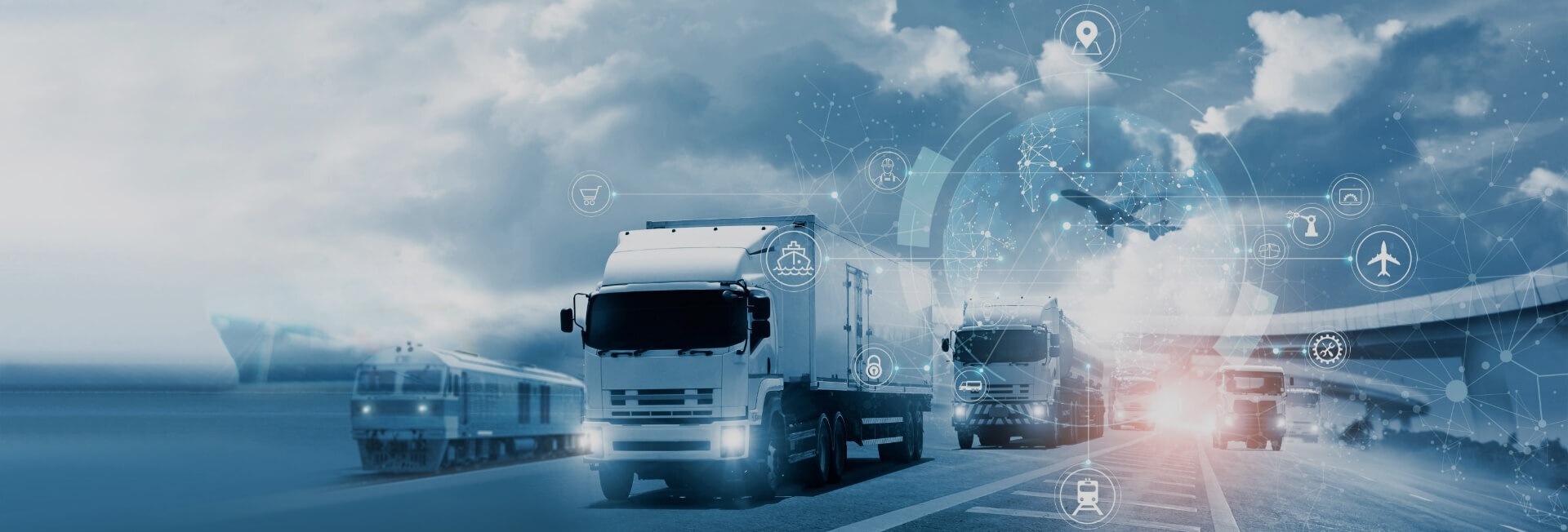
Fault detection in oil refineries
- Home
- Resources
- CANBus Integration and Application
- Fault detection in oil refineries
Fault Detection in Oil Refineries
Oil refineries play a vital role in processing crude oil into various petroleum products that fuel our modern society. These facilities are complex and require careful monitoring to ensure safety, efficiency, and prevent any potential faults or failures. Fault detection systems are crucial in identifying and addressing issues before they escalate into major incidents. In this article, we will explore the importance of fault detection in oil refineries and the various methods and technologies used in the industry.
The Importance of Fault Detection in Oil Refineries
Fault detection in oil refineries is essential for several reasons. First and foremost, it helps to maintain the overall safety of the facility and its personnel. Oil refineries are inherently hazardous environments, with various potential risks such as leaks, fires, and explosions. Detecting and addressing faults promptly can prevent these incidents from occurring and mitigate their consequences.
Secondly, fault detection systems aid in optimizing the efficiency and productivity of oil refineries. By identifying and resolving faults in equipment, processes, or systems, refineries can minimize downtime, reduce energy consumption, and improve overall operational performance. This, in turn, leads to cost savings and increased profitability.
Lastly, fault detection plays a crucial role in meeting regulatory compliance requirements. Oil refineries are subject to stringent regulations and standards imposed by local authorities and industry bodies. By implementing robust fault detection systems, refineries can ensure compliance and avoid costly penalties or shutdowns.
Methods and Technologies for Fault Detection
There are several methods and technologies employed in oil refineries for fault detection. Let's explore some of the commonly used ones:
1. Process Monitoring and Control Systems
Process monitoring and control systems are at the heart of fault detection in oil refineries. These systems continuously monitor various parameters such as temperature, pressure, flow rates, and chemical compositions. Deviations from normal operating conditions can indicate potential faults or abnormalities. Advanced algorithms and data analytics are employed to analyze the collected data and identify any anomalies. Once detected, appropriate actions can be taken to address the fault.
2. Vibration Analysis
Vibration analysis is another widely used technique for fault detection in rotating equipment such as pumps, compressors, and turbines. Vibrations can provide valuable insights into the health and condition of these machines. By analyzing vibration patterns, frequencies, and amplitudes, abnormalities or faults can be detected. This allows for timely maintenance and repair, preventing unexpected breakdowns and costly downtime.
3. Infrared Thermography
Infrared thermography involves the use of thermal imaging cameras to detect abnormalities in equipment and systems. By capturing the heat signatures of various components, potential faults such as overheating, insulation breakdown, or electrical issues can be identified. Infrared thermography is non-intrusive and can be performed during normal operation, making it a valuable tool for preventive maintenance and fault detection.
4. Leak Detection Systems
Oil refineries have extensive piping networks carrying various fluids and gases. Detecting leaks in these systems is crucial for preventing environmental contamination, fire hazards, and safety risks. Leak detection systems employ various technologies such as acoustic sensors, flow meters, and pressure sensors to identify leaks and alert operators. Early detection allows for prompt repairs and prevents further damage or accidents.
Integration of Data and Communication Systems
Fault detection in oil refineries is not limited to individual equipment or systems. It often involves the integration of data from multiple sources, such as process monitoring systems, vibration sensors, and infrared cameras. This integration enables a holistic view of the refinery's operations and facilitates comprehensive fault detection.
CANBus communication is commonly used for data integration in oil refineries. CANBus (Controller Area Network) is a robust and reliable communication protocol widely adopted in the automotive industry. Its ability to handle large amounts of data and support real-time communication makes it suitable for complex industrial environments like oil refineries.
CANBus interfaces and devices are used to collect data from various sensors and equipment in the refinery. This data is then transmitted to a central control system, where it is analyzed and processed for fault detection purposes. Advanced algorithms and machine learning techniques are employed to identify patterns, trends, and abnormalities in the collected data.
Remote vehicle diagnostics and fleet data integration solutions are also utilized in some oil refineries. These systems allow for real-time monitoring and fault detection of mobile equipment such as trucks, forklifts, and cranes. By integrating vehicle telematics data with the refinery's overall fault detection system, potential issues with mobile equipment can be identified and addressed promptly.
Benefits of Fault Detection in Oil Refineries
The implementation of robust fault detection systems in oil refineries offers several benefits:
1. Improved Safety
Fault detection systems help in maintaining a safe working environment for refinery personnel. By detecting faults early, potential hazards can be addressed promptly, minimizing the risk of accidents and injuries.
2. Enhanced Operational Efficiency
Fault detection allows refineries to optimize their operations by identifying and resolving issues that may impact efficiency. By minimizing downtime, reducing energy consumption, and improving overall performance, refineries can enhance their productivity and profitability.
3. Cost Savings
Timely detection and resolution of faults prevent costly breakdowns and repairs. By addressing issues proactively, refineries can avoid unplanned downtime and reduce maintenance costs.
4. Regulatory Compliance
Fault detection systems help refineries meet regulatory compliance requirements. By ensuring that equipment and processes are in good working condition, refineries can avoid penalties and maintain their operating licenses.
Conclusion
Fault detection is a critical aspect of maintaining safety, efficiency, and compliance in oil refineries. By employing various methods and technologies such as process monitoring systems, vibration analysis, infrared thermography, and leak detection systems, refineries can detect faults early and take appropriate actions. Integration of data and communication systems, including CANBus interfaces and remote vehicle diagnostics, further enhances fault detection capabilities. The benefits of robust fault detection systems in oil refineries are significant, including improved safety, enhanced operational efficiency, cost savings, and regulatory compliance.