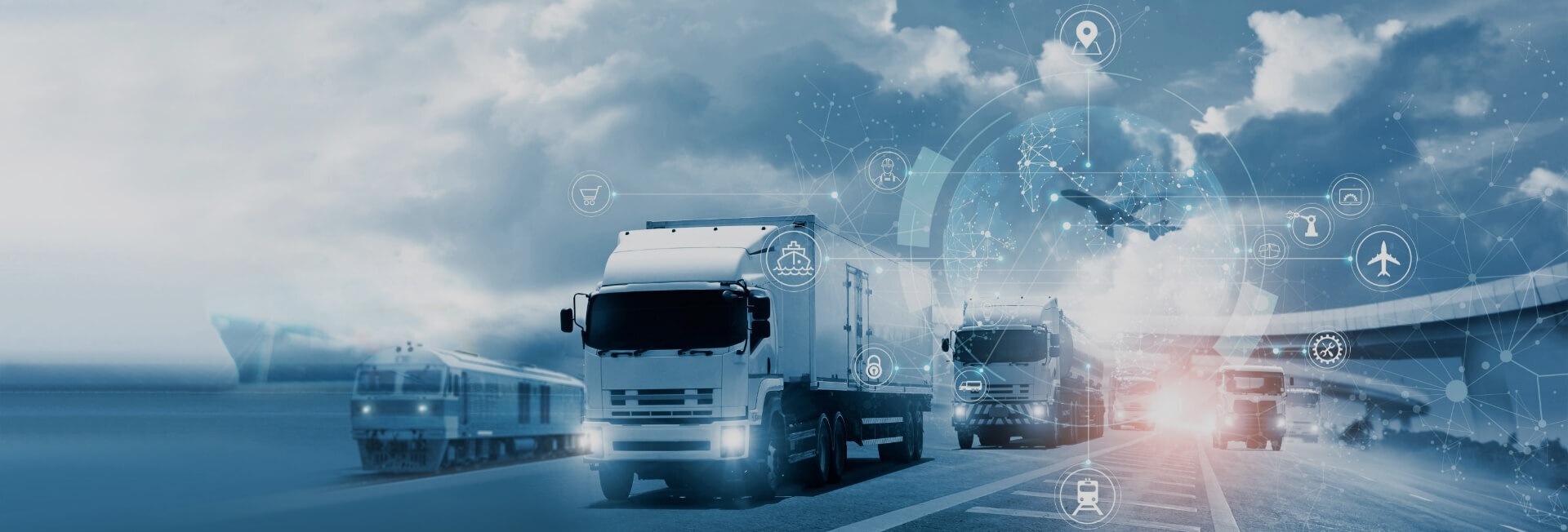
Fault detection in manufacturing processes
- Home
- Resources
- CANBus Integration and Application
- Fault detection in manufacturing processes
Fault Detection in Manufacturing Processes
In any manufacturing industry, maintaining high quality standards and minimizing faults is essential for efficiency and productivity. Fault detection refers to the process of identifying and diagnosing faults in manufacturing processes to ensure that products are produced to meet the desired specifications. With the advancement in technology, various fault detection techniques and tools have been developed to aid manufacturers in improving their processes and reducing defects. In this article, we will explore the importance of fault detection in manufacturing processes and discuss some of the commonly used techniques and tools.
The Importance of Fault Detection
Fault detection plays a crucial role in manufacturing processes for several reasons. Firstly, it helps in ensuring product quality and reliability. By detecting faults early in the production process, manufacturers can prevent defective products from reaching the market, thereby reducing customer complaints and recalls. This not only saves costs but also helps in building a positive reputation for the company.
Secondly, fault detection helps in improving process efficiency. By identifying and resolving faults promptly, manufacturers can optimize their production processes and reduce downtime. This leads to higher productivity and increased profitability. Additionally, fault detection enables manufacturers to identify the root causes of faults and implement corrective measures to prevent similar issues from recurring in the future.
Common Techniques for Fault Detection
There are several techniques that are commonly used for fault detection in manufacturing processes. These techniques can be broadly classified into two categories: statistical process control (SPC) and machine learning-based methods.
Statistical Process Control (SPC)
Statistical process control is a widely used technique for fault detection in manufacturing processes. It involves monitoring and controlling the process variables to ensure that they are within the desired range. SPC relies on statistical methods to analyze process data and identify any deviations from the normal operating conditions. By setting control limits and using control charts, manufacturers can detect and correct any abnormalities in the process, thereby preventing the production of faulty products.
SPC can be applied to various manufacturing processes, such as assembly lines, machining operations, and material handling. It helps in identifying and resolving issues related to machine performance, tool wear, material defects, and environmental factors. By continuously monitoring the process variables, manufacturers can make data-driven decisions and optimize their processes for maximum efficiency.
Machine Learning-Based Methods
Machine learning-based methods have gained popularity in recent years for fault detection in manufacturing processes. These methods involve training algorithms on historical process data to learn patterns and anomalies. Once trained, the algorithms can analyze real-time data and detect any deviations from the normal behavior of the process.
Machine learning-based methods can be used for both supervised and unsupervised fault detection. In supervised detection, the algorithms are trained on labeled data, where each data point is associated with a known fault condition. The algorithms learn to classify new data points based on the patterns observed in the training data. On the other hand, unsupervised detection does not require labeled data. The algorithms learn the normal behavior of the process and flag any deviations as potential faults.
Machine learning-based methods can be applied to various types of data, including sensor data, image data, and time series data. They can detect faults related to equipment malfunction, process drift, and component failure. By leveraging the power of machine learning, manufacturers can proactively identify faults and take corrective actions before they impact the product quality.
Fault Detection Tools
There are several tools available in the market that can aid manufacturers in fault detection. These tools are designed to collect and analyze data from various sources, such as sensors, control systems, and production equipment. By integrating these tools into the manufacturing processes, manufacturers can monitor the process variables in real-time and detect any faults or abnormalities.
One commonly used tool for fault detection is the CANBus interface. CANBus stands for Controller Area Network Bus, and it is a communication protocol used in automotive and industrial applications. By connecting the manufacturing equipment to the CANBus network, manufacturers can collect real-time data about the process variables and analyze them for fault detection.
Another tool for fault detection is remote vehicle diagnostics. This tool allows manufacturers to monitor and diagnose the performance of their vehicles remotely. By integrating telematics devices into the vehicles, manufacturers can collect data about various parameters, such as engine performance, fuel consumption, and emissions. This data can be analyzed to detect any faults or issues in the vehicles and take appropriate actions to resolve them.
Fleet data integration is another tool that can be used for fault detection. By integrating the data from the entire fleet of vehicles, manufacturers can analyze the performance and health of the vehicles on a larger scale. This helps in identifying any common faults or trends across the fleet and implementing preventive measures to address them.
Conclusion
Fault detection is a critical aspect of manufacturing processes that helps in ensuring product quality, improving process efficiency, and reducing costs. By using techniques such as statistical process control and machine learning-based methods, manufacturers can detect and diagnose faults in real-time, leading to higher productivity and customer satisfaction. Additionally, by using tools like CANBus interfaces, remote vehicle diagnostics, and fleet data integration, manufacturers can collect and analyze data to identify faults and take proactive measures to prevent them. Incorporating fault detection into manufacturing processes is essential for maintaining high standards and staying competitive in today's market.