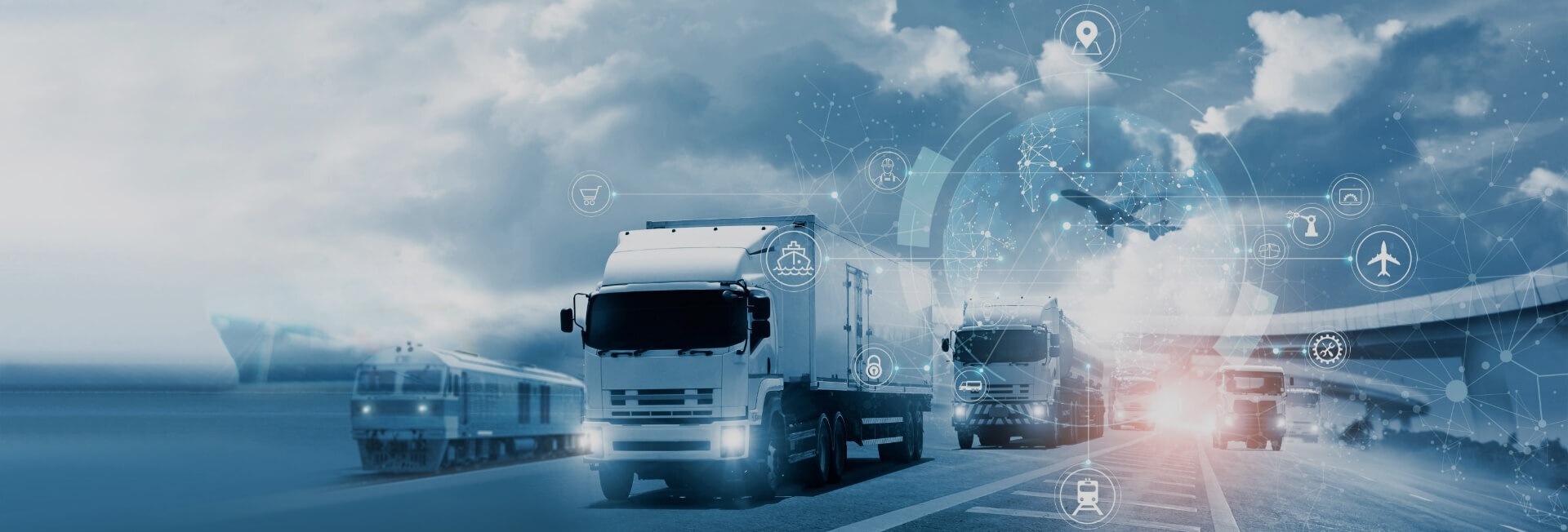
Fault detection in food processing systems
- Home
- Resources
- CANBus Integration and Application
- Fault detection in food processing systems
Fault Detection in Food Processing Systems
In the food processing industry, ensuring the quality and safety of food products is of utmost importance. Fault detection plays a crucial role in this process by identifying and addressing any issues that may arise during the production and processing of food. In this article, we will explore the importance of fault detection in food processing systems and how it can help in maintaining high standards of quality and safety.
What is Fault Detection?
Fault detection refers to the process of identifying and diagnosing faults or abnormalities in a system. In the context of food processing systems, fault detection involves monitoring various parameters such as temperature, pressure, humidity, and other relevant variables to ensure that the production process is running smoothly and that the final product meets the required standards.
By implementing fault detection systems, food processing companies can detect and address potential issues in real-time, minimizing the risk of product defects, contamination, and other quality-related problems. This not only helps in maintaining the reputation of the company but also ensures the safety of consumers.
Importance of Fault Detection in Food Processing Systems
Fault detection is crucial in food processing systems for several reasons:
1. Ensuring Product Quality
With the increasing demand for high-quality food products, it is essential for food processing companies to maintain consistent standards. Fault detection systems enable real-time monitoring of critical parameters, allowing companies to identify and address any deviations from the desired specifications. This ensures that the final product meets the expected quality standards and is safe for consumption.
2. Preventing Contamination
Contamination is a major concern in the food processing industry. Fault detection systems can help identify potential sources of contamination, such as equipment malfunctions or improper handling of raw materials. By detecting these issues early on, companies can take immediate corrective actions to prevent contamination and ensure the safety of the final product.
3. Minimizing Downtime
Unexpected equipment failures can lead to costly downtime in food processing plants. Fault detection systems can monitor the performance of various equipment and machinery, detecting any abnormalities or signs of potential failures. By identifying these issues in advance, maintenance and repair can be scheduled proactively, minimizing downtime and optimizing productivity.
4. Compliance with Regulations
The food processing industry is subject to various regulations and standards to ensure the safety and quality of food products. Fault detection systems can help companies comply with these regulations by providing real-time monitoring and documentation of critical parameters. This ensures that the production process is in line with the required standards and reduces the risk of non-compliance.
How Fault Detection Systems Work
Fault detection systems in food processing typically involve the use of sensors and data analysis algorithms to monitor and analyze various parameters. These systems can be integrated into the existing infrastructure of the food processing plant, allowing for seamless monitoring and control.
One common technology used in fault detection systems is the CANBus communication protocol. CANBus, short for Controller Area Network Bus, is a widely used protocol for communication between various devices in automotive and industrial applications. It allows for real-time data transmission and is highly reliable and robust.
By integrating CANBus devices and protocols into food processing systems, companies can collect and analyze data from various sensors and equipment in real-time. This enables the detection of abnormalities or deviations from the desired parameters, triggering alerts or automated corrective actions.
For example, in a food processing plant, temperature is a critical parameter that needs to be monitored to ensure food safety. A fault detection system using CANBus communication can continuously monitor the temperature of different processing stages and compare it to the desired range. If any deviations are detected, the system can immediately send an alert to the operators or automatically adjust the temperature settings to bring it back within the acceptable range.
Benefits of Fault Detection in Food Processing Systems
Fault detection systems offer several benefits for food processing companies:
1. Improved Productivity
By minimizing downtime and optimizing the performance of equipment, fault detection systems help improve overall productivity in food processing plants. Real-time monitoring and proactive maintenance allow companies to identify and address issues before they cause major disruptions, ensuring smooth operations and efficient production processes.
2. Enhanced Product Quality
Fault detection systems play a crucial role in maintaining consistent product quality. By monitoring and controlling critical parameters, companies can ensure that the final product meets the desired standards and is free from defects or contamination. This helps in building customer trust and loyalty, ultimately leading to increased sales and market share.
3. Cost Savings
Early detection and resolution of faults can help companies save significant costs associated with product recalls, rework, and customer complaints. By preventing issues from escalating, fault detection systems minimize the risk of producing and distributing substandard or unsafe food products, thereby reducing the financial impact on the company.
Conclusion
Fault detection plays a critical role in ensuring the quality and safety of food products in the processing industry. By implementing fault detection systems, companies can monitor and control various parameters, detect potential issues in real-time, and take immediate corrective actions. This helps in maintaining consistent product quality, preventing contamination, minimizing downtime, and complying with regulations. Fault detection systems, particularly those utilizing CANBus communication, offer numerous benefits, including improved productivity, enhanced product quality, and cost savings. In an industry where consumer trust and safety are paramount, fault detection is an essential tool for food processing companies.