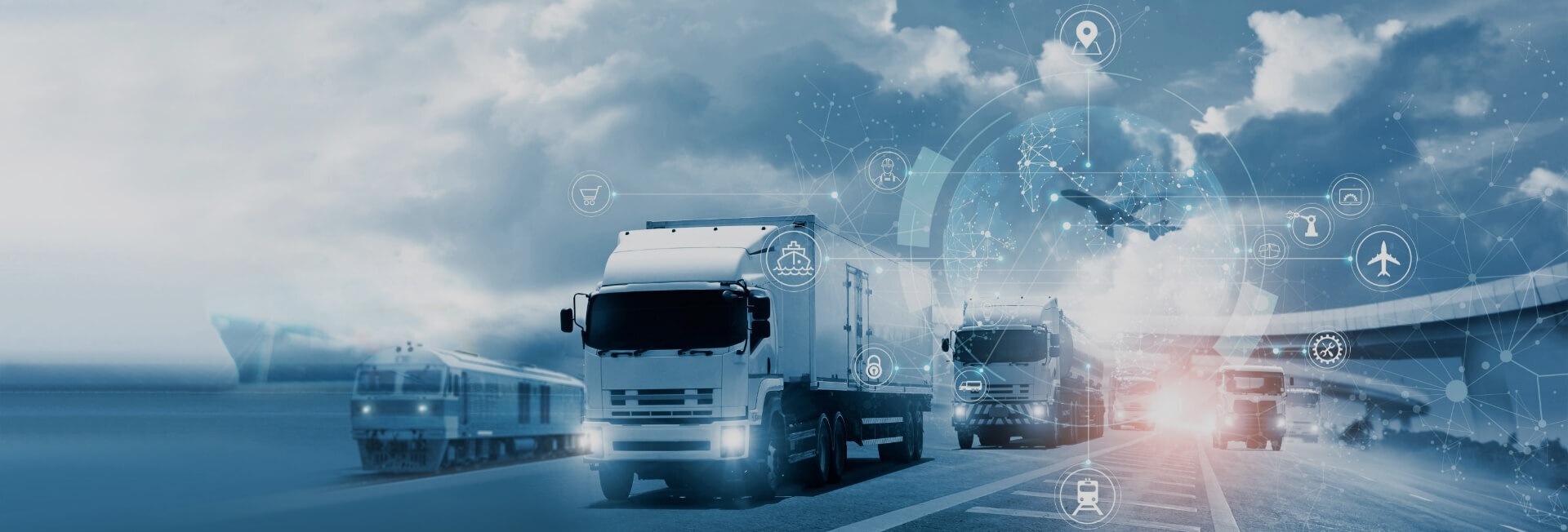
Fault detection in chemical storage facilities
- Home
- Resources
- CANBus Integration and Application
- Fault detection in chemical storage facilities
Fault Detection in Chemical Storage Facilities - Ensuring Safety and Preventing Accidents
Chemical storage facilities play a crucial role in various industries, including manufacturing, pharmaceuticals, and agriculture. These facilities store a wide range of chemicals, some of which can be hazardous if not handled properly. Therefore, it is essential to have robust fault detection systems in place to ensure safety and prevent accidents.
The Importance of Fault Detection
Fault detection systems are designed to monitor various parameters in chemical storage facilities and identify any abnormalities or potential issues. These systems can detect faults such as leaks, temperature fluctuations, pressure imbalances, and other critical indicators that may indicate a potential hazard.
Fault detection is crucial for several reasons:
1. Safety
The primary reason for implementing fault detection systems in chemical storage facilities is to ensure the safety of workers, the surrounding environment, and the general public. Chemical leaks or other faults can lead to fires, explosions, and the release of toxic substances, posing significant risks to human health and the environment.
By continuously monitoring the facility for faults, operators can quickly identify and address any issues before they escalate into major accidents. Fault detection systems can provide real-time alerts and notifications, allowing operators to take immediate action and mitigate potential risks.
2. Compliance
Chemical storage facilities are subject to various regulations and standards to ensure the safe handling and storage of hazardous materials. Fault detection systems can help facilities comply with these regulations by providing accurate monitoring and reporting capabilities.
By having a robust fault detection system in place, facility operators can demonstrate their commitment to safety and compliance to regulatory authorities. Regular monitoring and reporting can also help identify any areas for improvement and implement necessary measures to maintain compliance.
3. Cost Savings
Accidents in chemical storage facilities can have severe financial implications. The cost of cleanup, legal liabilities, and potential business disruptions can be significant. Fault detection systems can help prevent accidents and minimize the associated costs.
Early detection of faults allows operators to take immediate action and prevent incidents from escalating. By addressing issues promptly, operators can avoid costly cleanup operations, legal battles, and potential fines imposed by regulatory authorities.
Common Fault Detection Methods
There are several common methods used for fault detection in chemical storage facilities:
1. Sensor-Based Monitoring
Sensor-based monitoring involves the use of various sensors to measure parameters such as temperature, pressure, humidity, and gas concentrations. These sensors are strategically placed throughout the facility to provide comprehensive coverage.
The data collected from the sensors is continuously analyzed by a central monitoring system. Any deviations from the normal range trigger alerts, allowing operators to take immediate action. Sensor-based monitoring is highly effective in detecting leaks, temperature fluctuations, and other critical faults.
2. Video Surveillance
Video surveillance systems can also be used for fault detection in chemical storage facilities. High-resolution cameras are installed in key areas to monitor for any signs of leaks, spills, or other abnormalities.
Advanced video analytics software can analyze the live video feed and identify potential faults in real-time. This allows for quick response and minimizes the risk of accidents or incidents going unnoticed.
3. Remote Monitoring
Remote monitoring systems enable facility operators to monitor the status of their chemical storage facilities from a centralized location. These systems use advanced communication technologies, such as CANBus communication, to collect data from various sensors and devices.
Operators can access real-time data and receive instant alerts on their computers or mobile devices. This allows for proactive fault detection and timely response, even if the operators are not physically present at the facility.
Implementing a Fault Detection System
Implementing a fault detection system in a chemical storage facility requires careful planning and consideration. Here are some steps to follow:
1. Identify Critical Parameters
Start by identifying the critical parameters that need to be monitored in your facility. This could include temperature, pressure, humidity, gas concentrations, and any other relevant factors.
Consider the specific requirements of your facility and the chemicals you store to determine the most appropriate parameters to monitor.
2. Select the Right Sensors and Devices
Once you have identified the critical parameters, choose the appropriate sensors and devices to monitor them. There are various options available in the market, so make sure to select reliable and accurate devices that meet your specific needs.
3. Design the Monitoring System
Design a monitoring system that integrates all the sensors and devices effectively. Consider the layout of your facility, the placement of sensors, and the communication protocols required for data collection and analysis.
If you are implementing a remote monitoring system, ensure that you have the necessary infrastructure and technology in place to support secure and reliable communication.
4. Integrate with Existing Systems
If you have existing systems in place, such as a SCADA (Supervisory Control and Data Acquisition) system, ensure that your fault detection system can integrate seamlessly with these systems. This will allow for centralized monitoring and streamlined data analysis.
5. Train Operators
Train your operators on how to effectively use the fault detection system and interpret the data collected. They should understand the different fault indicators and know how to respond appropriately to alerts and notifications.
Conclusion
Fault detection systems are essential for ensuring the safety of chemical storage facilities. By continuously monitoring critical parameters and detecting faults in real-time, these systems can prevent accidents, minimize risks, and help facilities comply with regulations.
Implementing a fault detection system requires careful planning, selection of the right sensors and devices, and integration with existing systems. By following the necessary steps and investing in a robust system, chemical storage facilities can enhance safety, reduce costs, and protect the environment.