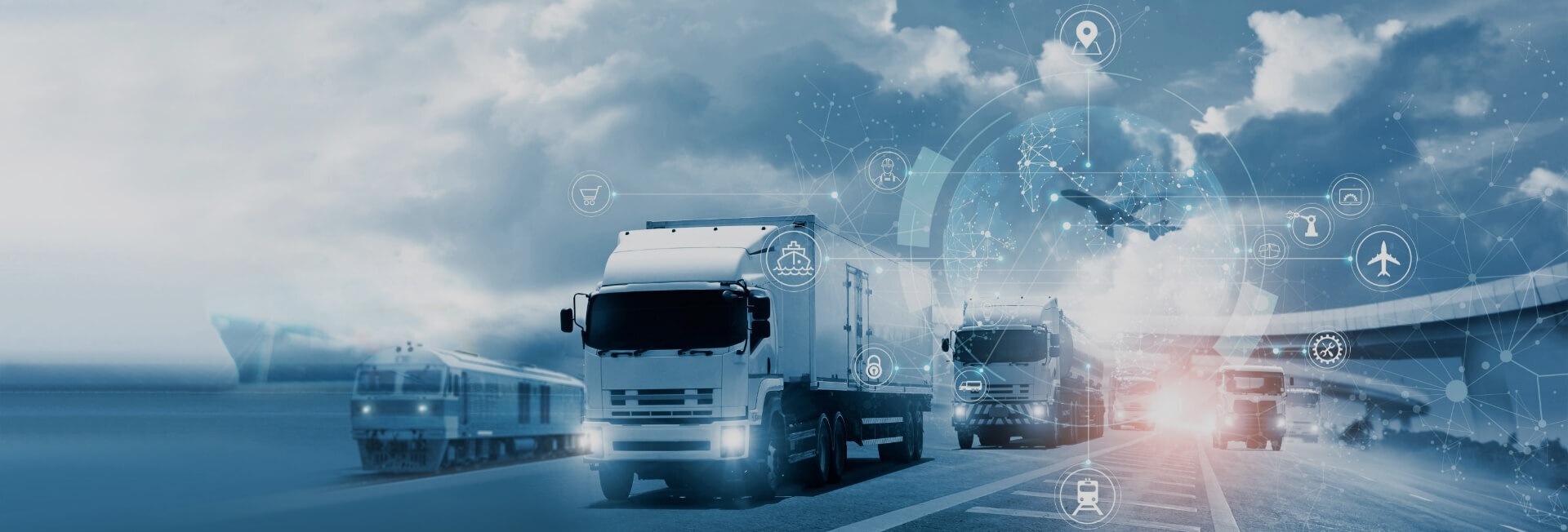
Fault detection in chemical reactors
- Home
- Resources
- CANBus Integration and Application
- Fault detection in chemical reactors
Fault Detection in Chemical Reactors
In the field of chemical engineering, fault detection in chemical reactors plays a crucial role in ensuring safe and efficient operation. Chemical reactors are used in various industrial processes, such as manufacturing pharmaceuticals, producing polymers, and refining petroleum. Detecting faults in these reactors is essential to prevent accidents, optimize production, and minimize downtime.
The Importance of Fault Detection
Fault detection is the process of identifying abnormalities or deviations from normal operating conditions in a chemical reactor. These abnormalities can range from equipment malfunctions to variations in reactant concentrations and reaction rates. Detecting and diagnosing faults in real-time allows operators to take corrective actions and prevent catastrophic failures.
Methods for Fault Detection
There are several methods and techniques used for fault detection in chemical reactors. Some of the commonly employed methods include:
Sensor-Based Approaches
Sensor-based approaches involve monitoring various process variables, such as temperature, pressure, flow rate, and composition, using sensors. These sensors provide real-time data, which is then analyzed using statistical methods or machine learning algorithms to detect anomalies. By comparing the observed values with expected values, faults can be identified and classified.
Model-Based Approaches
Model-based approaches use mathematical models of the chemical reactor to simulate its behavior under normal operating conditions. These models are then used to predict the expected values of process variables. Any deviation between the predicted and observed values indicates the presence of a fault. Model-based approaches are often more accurate but require detailed knowledge of the reactor and its dynamics.
Integration of CANBus Communication
One of the key advancements in fault detection in chemical reactors is the integration of CANBus communication. CANBus, which stands for Controller Area Network, is a communication protocol commonly used in automotive and industrial applications. By connecting various sensors and actuators to a central CANBus network, real-time data can be collected and analyzed for fault detection.
CANBus Interface
A CANBus interface is a device that allows communication between the CANBus network and a computer system. It enables the transfer of data between the sensors and the fault detection software. By integrating a CANBus interface into the chemical reactor system, operators can monitor and analyze process variables in real-time, enabling early fault detection and diagnosis.
Remote Vehicle Diagnostics
Remote vehicle diagnostics, commonly used in the automotive industry, can also be applied to chemical reactors. By implementing remote vehicle diagnostics systems, operators can monitor the health and performance of the reactor from a remote location. Real-time data from the CANBus network can be transmitted to a central monitoring station, where advanced analytics can be applied to detect faults and anomalies.
Benefits of Fault Detection in Chemical Reactors
Implementing a robust fault detection system in chemical reactors offers several benefits:
Enhanced Safety
Fault detection systems help prevent accidents and ensure the safety of personnel working with the reactors. By detecting faults in real-time, operators can take immediate actions to mitigate risks and avoid hazardous situations.
Optimized Production
Faults in chemical reactors can lead to suboptimal production and decreased product quality. By detecting and diagnosing faults early on, operators can make necessary adjustments to optimize production and minimize downtime.
Reduced Maintenance Costs
Timely fault detection allows for proactive maintenance, reducing the risk of equipment failures and costly repairs. By addressing potential issues before they escalate, operators can save on maintenance costs and extend the lifespan of the reactor.
Improved Efficiency
Fault detection systems enable operators to identify and eliminate inefficiencies in the reactor. By continuously monitoring and analyzing process variables, operators can fine-tune the operation to achieve higher efficiency and energy savings.
CANBus Diagnostic Tools
There are various CANBus diagnostic tools available in the market that facilitate fault detection in chemical reactors:
CANBus Analyzers
CANBus analyzers are hardware devices that allow for the capture and analysis of data on the CANBus network. These analyzers provide insights into the communication between sensors, actuators, and the central control system, enabling operators to identify faults and anomalies.
Diagnostic Software
Diagnostic software is used to analyze the data collected from the CANBus network and identify faults. This software often incorporates machine learning algorithms and statistical methods to detect patterns and anomalies in the data. It provides real-time alerts and recommendations for corrective actions.
Conclusion
Fault detection in chemical reactors is essential for safe and efficient operation. By integrating CANBus communication and utilizing advanced fault detection techniques, operators can proactively identify and address faults in real-time. This leads to enhanced safety, optimized production, reduced maintenance costs, and improved efficiency. The availability of CANBus diagnostic tools further facilitates the fault detection process, enabling operators to make data-driven decisions for optimal reactor performance.