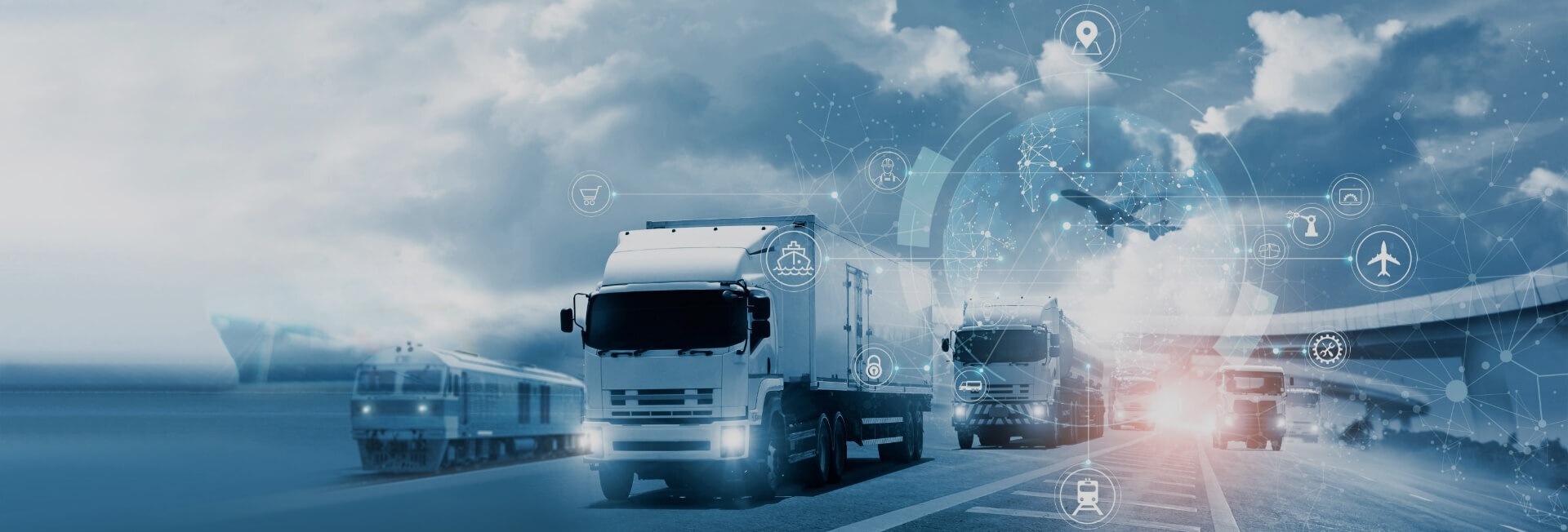
Fault detection in chemical processes
- Home
- Resources
- CANBus Integration and Application
- Fault detection in chemical processes
Fault Detection in Chemical Processes
Fault detection in chemical processes is vital for maintaining the safety and efficiency of these complex systems. Chemical processes involve numerous interconnected components and variables, making it challenging to identify and address issues when they arise. However, with the advancements in technology and the development of sophisticated fault detection systems, it has become easier to detect and diagnose faults in chemical processes.
Understanding Fault Detection
Fault detection refers to the process of identifying abnormalities or deviations from normal operating conditions in a chemical process. These abnormalities can occur due to equipment malfunction, process variations, or external factors. Early detection of faults is crucial as it allows for timely intervention and prevents the escalation of minor issues into major problems.
One of the primary challenges in fault detection is distinguishing between normal process variations and actual faults. Chemical processes often exhibit variability due to factors such as raw material variations, environmental conditions, and equipment wear. Fault detection systems utilize advanced algorithms and statistical techniques to differentiate between normal variations and abnormal conditions.
Importance of Fault Detection in Chemical Processes
Fault detection plays a crucial role in maintaining the safety and productivity of chemical processes. Here are some key reasons why fault detection is important:
1. Safety:
Faults in chemical processes can pose serious safety risks, including the release of hazardous substances, fire, or explosions. Rapid fault detection allows for timely intervention, minimizing the potential for accidents and ensuring the safety of personnel and the surrounding environment.
2. Cost Savings:
Faults in chemical processes can lead to production losses, increased energy consumption, and equipment damage. By detecting faults early on, companies can prevent these issues from escalating, resulting in significant cost savings.
3. Process Optimization:
Fault detection systems provide valuable insights into the performance of chemical processes. By identifying and analyzing faults, companies can optimize their processes, improve efficiency, and reduce waste.
Fault Detection Methods
Various methods and techniques are used for fault detection in chemical processes. Here are some commonly employed approaches:
1. Statistical Process Control (SPC):
SPC is a widely used method for real-time monitoring and fault detection in chemical processes. It involves the continuous monitoring of process variables and the use of statistical techniques to identify deviations from normal operating conditions. SPC can detect both gradual and sudden changes in process behavior, enabling proactive intervention.
2. Pattern Recognition:
Pattern recognition techniques involve analyzing historical process data to identify patterns associated with normal and faulty conditions. These patterns are then used to classify current process behavior and detect anomalies. Pattern recognition methods are particularly effective for detecting complex faults that may not be easily identifiable using other techniques.
3. Artificial Intelligence (AI) and Machine Learning:
AI and machine learning algorithms are increasingly being utilized for fault detection in chemical processes. These algorithms can analyze large volumes of data and identify patterns and correlations that may go unnoticed by human operators. AI-based fault detection systems can continuously learn and adapt to changing process conditions, improving their accuracy over time.
4. Model-Based Approaches:
Model-based approaches involve developing mathematical models of the chemical process and comparing the actual process behavior with the expected behavior predicted by the model. Deviations between the predicted and actual behavior indicate the presence of faults. Model-based approaches are particularly effective when detailed knowledge about the process dynamics is available.
Integration of Fault Detection Systems
Integrating fault detection systems into chemical processes requires careful planning and consideration. Here are some key factors to consider:
1. Sensor Selection:
The selection of appropriate sensors is critical for accurate fault detection. Sensors should be able to measure relevant process variables with high precision and reliability. Different types of sensors may be required depending on the specific process and fault detection requirements.
2. Data Acquisition and Preprocessing:
Data acquisition involves collecting data from sensors and other sources in real-time. The acquired data may require preprocessing to filter out noise, remove outliers, and normalize the variables. Preprocessing ensures that the data is suitable for analysis and improves the accuracy of fault detection algorithms.
3. Algorithm Selection:
Choosing the right fault detection algorithm is crucial for effective fault detection. Different algorithms have varying strengths and weaknesses, and their suitability depends on the specific process and fault characteristics. It is important to evaluate and compare different algorithms to determine the most appropriate one for a given application.
4. Integration with Process Control Systems:
Fault detection systems are most effective when integrated with process control systems. Integration allows for real-time monitoring and control, enabling immediate response to detected faults. Integration also facilitates the implementation of corrective actions and the optimization of process performance.
Future Trends in Fault Detection
The field of fault detection in chemical processes is continuously evolving, driven by advancements in technology and industry requirements. Here are some future trends to watch out for:
1. Advanced Analytics:
Advancements in data analytics and machine learning techniques will enable more sophisticated fault detection algorithms. These algorithms will be capable of handling larger volumes of data and identifying complex patterns and correlations.
2. Integration of IoT and Industrial Automation:
The integration of the Internet of Things (IoT) and industrial automation will enable the collection of real-time data from a wide range of sensors and devices. This data can be utilized for fault detection, enabling proactive intervention and optimization of chemical processes.
3. Remote Monitoring and Diagnostics:
Remote monitoring and diagnostics will become more prevalent in fault detection. This approach allows for the monitoring of chemical processes from remote locations, facilitating timely fault detection and intervention. Remote monitoring also reduces the need for physical presence, improving safety and efficiency.
4. Cloud-Based Solutions:
Cloud-based fault detection solutions offer several advantages, including scalability, accessibility, and cost-effectiveness. These solutions enable real-time monitoring and analysis of process data from anywhere, making them suitable for both large-scale and small-scale chemical processes.
Conclusion
Fault detection is a critical aspect of maintaining the safety and efficiency of chemical processes. By utilizing advanced fault detection systems and techniques, companies can detect and diagnose faults in real-time, enabling timely intervention and preventing potential accidents and losses. The integration of fault detection systems with process control systems and the adoption of emerging trends will further enhance the accuracy and effectiveness of fault detection in chemical processes.