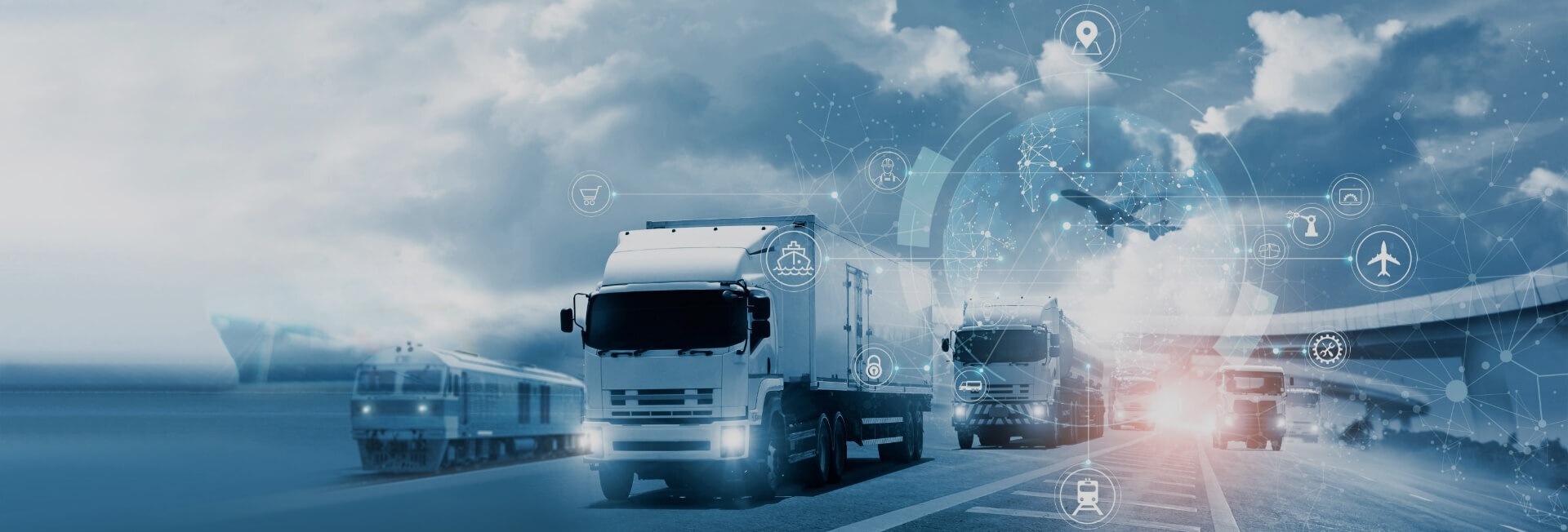
Common methods of fault detection in industrial systems
- Home
- Resources
- CANBus Integration and Application
- Common methods of fault detection in industrial systems
Methods of Fault Detection in Industrial Systems
Industrial systems are complex and require continuous monitoring to ensure their proper functioning. Fault detection is a critical aspect of industrial system management as it helps identify and resolve issues before they cause significant damage or disruption. In this article, we will explore some common methods of fault detection in industrial systems.
1. Vehicle Diagnostics
Vehicle diagnostics is a method of fault detection specifically applicable to automotive systems. It involves the use of vehicle telematics and CANBus communication to monitor and analyze various parameters of the vehicle. By integrating automotive data and performing real-time analysis, vehicle diagnostics systems can detect faults and provide insights into the health of the vehicle.
One of the key components of vehicle diagnostics is the CANBus interface. The CANBus network connects different canbus devices within the vehicle and allows for the exchange of information. By leveraging canbus protocols and solutions, vehicle diagnostics systems can access vital data from different components of the vehicle, such as the engine, transmission, brakes, and more.
Remote vehicle diagnostics is an advanced application of vehicle diagnostics that enables real-time fault detection and monitoring of vehicles remotely. With the help of fleet data integration and vehicle data management systems, remote vehicle diagnostics can provide valuable insights into the health of an entire fleet of vehicles, allowing for proactive maintenance and reducing downtime.
2. Industrial Sensors and Alarms
Industrial sensors and alarms are widely used in various industrial systems to detect faults and abnormal conditions. These sensors are designed to monitor specific parameters, such as temperature, pressure, flow rate, and more. When a parameter exceeds a predefined threshold or deviates from the normal range, the sensor triggers an alarm, indicating a potential fault or issue.
Industrial sensors can be integrated into a centralized control system, which continuously monitors the readings from multiple sensors. By analyzing the data from different sensors, the control system can identify patterns and anomalies that may indicate a fault. This allows for timely intervention and preventive maintenance, reducing the risk of system failures and downtime.
3. Data Analytics and Machine Learning
Data analytics and machine learning techniques can be applied to industrial systems to detect faults and anomalies. By collecting and analyzing large volumes of data from various sensors and sources, data analytics algorithms can identify patterns and trends that indicate potential faults.
Machine learning algorithms can be trained on historical data to recognize known fault patterns and predict the likelihood of future faults. This enables proactive maintenance and reduces the risk of unexpected failures. Additionally, machine learning algorithms can adapt and learn from new data, allowing for continuous improvement in fault detection capabilities.
4. Fault Tree Analysis
Fault tree analysis is a systematic method used to analyze and identify the root causes of faults in complex systems. It involves constructing a graphical representation of the system and its components, along with the potential failure modes and their interdependencies.
By analyzing the fault tree, engineers can identify critical components and failure modes that need to be monitored closely. This allows for targeted fault detection and preventive maintenance. Additionally, fault tree analysis helps in understanding the impact of component failures on the overall system, enabling better decision-making and risk management.
Conclusion
Fault detection is a crucial aspect of industrial system management. By employing methods such as vehicle diagnostics, industrial sensors and alarms, data analytics and machine learning, and fault tree analysis, organizations can proactively detect faults and prevent system failures. Implementing these methods not only improves the reliability and efficiency of industrial systems but also reduces maintenance costs and downtime.